- お役立ち記事
- The difference between Intermediate Inventory and Work-in-progress Inventory
The difference between Intermediate Inventory and Work-in-progress Inventory
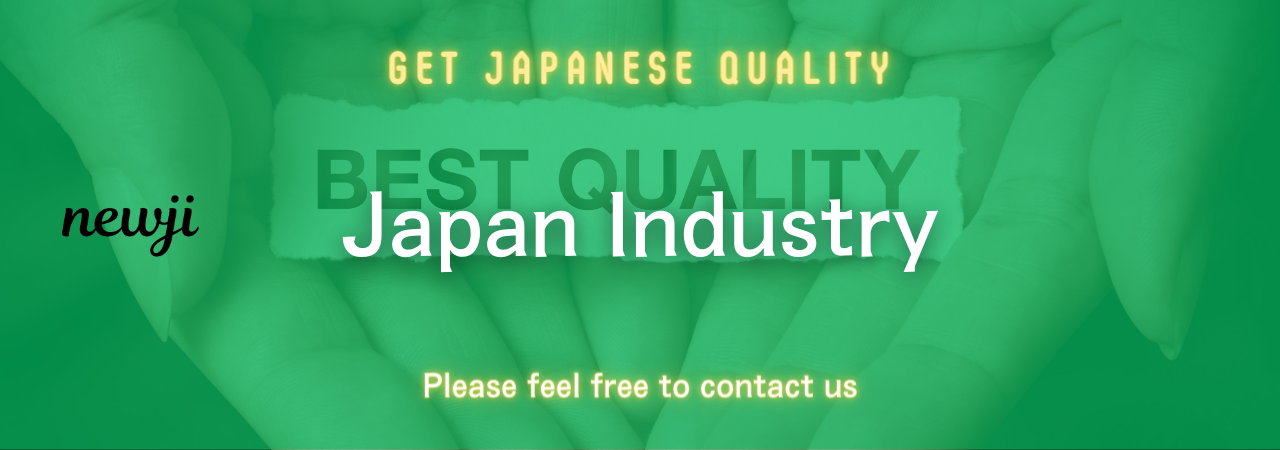
Understanding inventory management is essential in any business involving the production of goods.
Two key concepts often arising in such discussions are intermediate inventory and work-in-progress inventory.
These terms may sound similar but hold distinct meanings.
目次
What is Intermediate Inventory?
Intermediate inventory represents partially processed goods or materials that are not yet in a final form but have passed several stages in the production process.
It bridges the gap between raw materials and finished products, sometimes referred to as semi-finished products.
Characteristics of Intermediate Inventory
Unlike raw materials, intermediate inventory has undergone some form of transformation.
However, unlike finished goods, they cannot be sold directly to consumers.
They often require additional processing or assembly before reaching their final state.
Intermediate inventory might include components like partially assembled electronics or pre-processed food ingredients.
What is Work-in-progress Inventory?
Work-in-progress (WIP) inventory represents items currently moving through the production process.
They have started their journey as raw materials and are at various stages toward becoming finished goods.
This category includes everything from the inception of production until the item reaches the completion stage.
Characteristics of Work-in-progress Inventory
WIP inventory fluctuates as projects and operations advance.
These items are often still in active production lines, encompassing several stages ranging from initial processing to near-completion.
Examples include a car chassis on an assembly line or bread dough in a bakery.
Key Differences
Position in the Production Cycle
One major difference lies in their position within the production cycle.
Intermediate inventory is found between raw materials and work-in-progress inventory.
It’s usually more refined than raw materials but not as developed as WIP items.
On the other hand, WIP inventory spans several stages of active production until the products are nearly complete.
Completion Status
Intermediate inventory typically requires additional processes to become a part of finished goods, while WIP inventory is in the midst of these processes.
For example, if producing a smartphone, intermediate inventory might consist of microchips, whereas WIP inventory would include a nearly assembled smartphone.
Representation of Costs
Intermediate inventory often involves lower costs due to fewer stages of production transited.
WIP inventory usually embodies higher costs as they have absorbed several production stages.
Production costs increase as items transition from raw materials to finished goods.
Importance in Business Management
Understanding these inventory types is crucial for effective business management.
They provide insightful data for managing materials, labor, and production timelines.
Production Planning Accuracy
Proper identification and management of intermediate and WIP inventories enable more accurate production planning.
Businesses can better predict the time required for each production stage.
This improved understanding helps companies minimize production delays and optimize schedules.
Cost Management and Efficiency
Knowing which items fall into intermediate or WIP categories allows companies to track production costs more precisely.
It helps in identifying areas where cost-saving opportunities exist.
For example, businesses can determine whether to outsource certain stages or keep them in-house based on cost analysis.
Optimizing Storage and Space
Proper categorization aids in the efficient use of storage space.
Intermediate inventory typically takes up less space and requires different storage conditions compared to work-in-progress items.
Efficient storage strategies prevent bottlenecks and streamline production flow.
Conclusion
Intermediate inventory and work-in-progress inventory are integral components of the production process.
Understanding their differences helps in effective business and inventory management.
Correctly identifying and tracking these inventories streamline operations, enhance cost management, and improve production efficiency.
Grasping these concepts will undeniably present advantages in managing production-related challenges.
資料ダウンロード
QCD調達購買管理クラウド「newji」は、調達購買部門で必要なQCD管理全てを備えた、現場特化型兼クラウド型の今世紀最高の購買管理システムとなります。
ユーザー登録
調達購買業務の効率化だけでなく、システムを導入することで、コスト削減や製品・資材のステータス可視化のほか、属人化していた購買情報の共有化による内部不正防止や統制にも役立ちます。
NEWJI DX
製造業に特化したデジタルトランスフォーメーション(DX)の実現を目指す請負開発型のコンサルティングサービスです。AI、iPaaS、および先端の技術を駆使して、製造プロセスの効率化、業務効率化、チームワーク強化、コスト削減、品質向上を実現します。このサービスは、製造業の課題を深く理解し、それに対する最適なデジタルソリューションを提供することで、企業が持続的な成長とイノベーションを達成できるようサポートします。
オンライン講座
製造業、主に購買・調達部門にお勤めの方々に向けた情報を配信しております。
新任の方やベテランの方、管理職を対象とした幅広いコンテンツをご用意しております。
お問い合わせ
コストダウンが利益に直結する術だと理解していても、なかなか前に進めることができない状況。そんな時は、newjiのコストダウン自動化機能で大きく利益貢献しよう!
(Β版非公開)