- お役立ち記事
- Unlocking the Future of Manufacturing: How “Reaction Injection Molding” (反応注射成形) Revolutionizes Japanese Industry
Unlocking the Future of Manufacturing: How “Reaction Injection Molding” (反応注射成形) Revolutionizes Japanese Industry
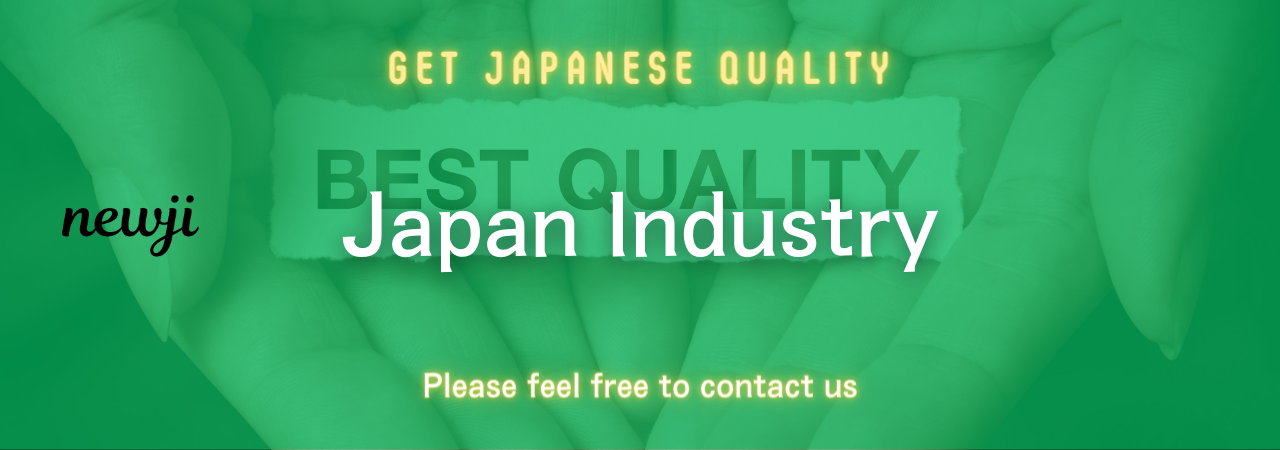
目次
Introduction to Reaction Injection Molding
Reaction Injection Molding (RIM) is a process that has been increasingly adopted by various industries, especially the automotive and aerospace sectors, due to its efficiency and versatility.
Developed initially in the 1960s, RIM has undergone several advancements, making it a viable method for producing lightweight, durable, and complex components.
In Japan, this technology has been particularly revolutionary for the manufacturing industry, transforming traditional production methods and bringing numerous benefits.
Understanding the Basics of Reaction Injection Molding
What is Reaction Injection Molding?
RIM involves mixing two liquid reactants, typically a polyol and an isocyanate, which react chemically and expand to form a polymer while inside a mold.
Unlike traditional injection molding, which uses thermoplastic materials, RIM employs thermosetting polymers that set into a hard, durable form once the chemical reaction is complete.
The process involves several key steps:
– Mixing the reactants in a controlled environment
– Injecting the mixture into a mold
– Allowing the chemical reaction to occur and harden
– Demolding the finished product.
Advantages of Reaction Injection Molding
There are several advantages to using RIM, particularly for high-volume, high-precision manufacturing:
– **Lightweight Components**: The materials used in RIM are typically lighter compared to metals and traditional plastics, making them ideal for industries where weight is a critical factor.
– **Design Flexibility**: RIM allows for complex shapes and designs that would be difficult or impossible to achieve with other molding processes.
– **Durability and Strength**: The polymers used in RIM are known for their toughness and resistance to impact, making them suitable for robust applications.
– **Cost-Effective for Low to Medium Volume Production**: RIM is generally more cost-effective for producing smaller quantities of parts, as the molds are cheaper to produce compared to those used in traditional injection molding.
The Role of Reaction Injection Molding in Japanese Industry
Automotive Sector
In Japan, the automotive industry has embraced RIM for its ability to produce lightweight yet durable components.
The reduction in weight contributes to improved fuel efficiency and lower emissions, which align with global sustainability goals.
Components such as bumpers, dashboards, and interior panels are often produced using RIM, benefiting from the ability to implement complex designs and integrated features.
Japanese manufacturers have also leveraged RIM to enhance the aesthetic appeal of vehicles, offering more sophisticated and customizable designs.
Aerospace Industry
The aerospace industry is another sector where RIM has made significant inroads in Japan.
The need for lightweight and durable components is even more critical due to the higher costs associated with aerospace operations.
RIM allows for the production of complex parts that minimize aircraft weight while maximizing strength and durability.
This translates to better fuel efficiency and more economically viable operations.
Consumer Electronics
The consumer electronics industry benefits from RIM by producing durable housings and components that can withstand daily wear and tear.
Japanese companies are known for their emphasis on quality and reliability, and RIM plays a crucial role in meeting these standards.
The versatility of RIM allows for sleek and ergonomic designs, essential for consumer appeal in products such as laptops, smartphones, and gaming consoles.
Practical Applications and Innovation
Customization and Prototyping
One of the most significant advantages of RIM is its suitability for customization and prototyping.
Japanese manufacturers often require small batches of custom-designed parts for specialized applications or new product launches.
RIM enables rapid prototyping and fine-tuning of designs without incurring the high costs and long lead times associated with traditional molding techniques.
Integration with Automation
In the context of factory automation, RIM integrates seamlessly with modern manufacturing systems.
Japanese facilities, known for their high levels of automation, have adapted RIM into their automated production lines.
This not only enhances efficiency but also reduces the risk of human error, ensuring consistent quality and precision in the finished products.
Challenges and Disadvantages
Initial Cost and Investment
While RIM offers several benefits, the initial setup costs can be significant.
The machinery and technology required for RIM can represent a substantial investment, particularly for small to medium-sized enterprises.
Material Limitations
RIM is generally limited to thermosetting polymers, which may not be suitable for all applications.
Additionally, finding the right material formulation can be complex and may require extensive testing and development.
Cycle Time
The cycle time for RIM can be longer compared to traditional injection molding processes.
This may be a limiting factor for high-volume production runs where speed is of the essence.
Supplier Negotiation Techniques
Understanding the Supplier Landscape
Effective supplier negotiation starts with a thorough understanding of the supplier landscape.
In Japan, this means recognizing the importance of relationship-building and mutual respect.
Japanese suppliers tend to place a high value on long-term partnerships and reliability, which can work to the advantage of procurement professionals who invest time in building trust.
Leveraging Innovation
Demonstrating a commitment to innovation can be a compelling negotiation strategy.
Japanese suppliers are often at the forefront of technological advancements, and showing an interest in incorporating innovative techniques like RIM can foster collaborative partnerships.
Focus on Quality
Japanese manufacturing is synonymous with high quality.
Highlighting a shared commitment to quality standards can create a strong foundation for negotiation.
Procurement professionals should emphasize their dedication to maintaining and even exceeding these standards to align with the supplier’s values.
Market Conditions and Future Trends
Growing Demand for Lightweight Materials
The global trend towards lightweight materials, driven by the need for fuel efficiency and sustainability, is likely to continue boosting the demand for RIM.
Japanese manufacturers are well-positioned to capitalize on this trend by leveraging their expertise in RIM to deliver high-quality, lightweight components.
Technological Advancements
Ongoing advancements in RIM technology, including improved materials and more efficient processes, will further enhance its viability and appeal.
Japanese companies are expected to remain at the cutting edge, continually refining and advancing RIM applications across various industries.
Sustainability Initiatives
Sustainability is becoming an increasingly critical factor in manufacturing.
RIM aligns well with these initiatives, offering a method for producing components that are not only lightweight but also durable, thereby reducing waste and promoting long-term use.
Japanese manufacturers, with their strong focus on sustainability, are likely to adopt and expand the use of RIM as part of their broader environmental strategies.
Best Practices for Implementing RIM
Collaborative Development
Success in using RIM often depends on collaboration between various stakeholders, including suppliers, engineers, and designers.
Japanese manufacturing culture, which highly values teamwork and collective problem-solving, is particularly conducive to this collaborative approach.
Emphasis on Training
Ensuring that all personnel involved in the RIM process are thoroughly trained is essential for maintaining high standards of quality and efficiency.
Japanese companies typically invest heavily in training, ensuring that their workforce is skilled and knowledgeable about the latest techniques and technologies.
Continuous Improvement
The principle of kaizen, or continuous improvement, is deeply ingrained in Japanese manufacturing philosophy.
Applying this principle to RIM involves regular reviews and assessments to identify areas for enhancement and implement incremental improvements over time.
Conclusion
Reaction Injection Molding is a transformative technology with the potential to revolutionize not only the Japanese manufacturing industry but also global manufacturing practices.
Its ability to produce lightweight, durable, and complex components makes it an invaluable tool in sectors ranging from automotive to aerospace and consumer electronics.
By understanding the intricacies of RIM, recognizing its advantages and limitations, and adopting best practices, companies can unlock its full potential.
As the demand for high-quality, sustainable, and efficiently produced components grows, RIM will undoubtedly play a pivotal role in shaping the future of manufacturing.
資料ダウンロード
QCD調達購買管理クラウド「newji」は、調達購買部門で必要なQCD管理全てを備えた、現場特化型兼クラウド型の今世紀最高の購買管理システムとなります。
ユーザー登録
調達購買業務の効率化だけでなく、システムを導入することで、コスト削減や製品・資材のステータス可視化のほか、属人化していた購買情報の共有化による内部不正防止や統制にも役立ちます。
NEWJI DX
製造業に特化したデジタルトランスフォーメーション(DX)の実現を目指す請負開発型のコンサルティングサービスです。AI、iPaaS、および先端の技術を駆使して、製造プロセスの効率化、業務効率化、チームワーク強化、コスト削減、品質向上を実現します。このサービスは、製造業の課題を深く理解し、それに対する最適なデジタルソリューションを提供することで、企業が持続的な成長とイノベーションを達成できるようサポートします。
オンライン講座
製造業、主に購買・調達部門にお勤めの方々に向けた情報を配信しております。
新任の方やベテランの方、管理職を対象とした幅広いコンテンツをご用意しております。
お問い合わせ
コストダウンが利益に直結する術だと理解していても、なかなか前に進めることができない状況。そんな時は、newjiのコストダウン自動化機能で大きく利益貢献しよう!
(Β版非公開)