- お役立ち記事
- The difference between Factory Layout and Cell Production
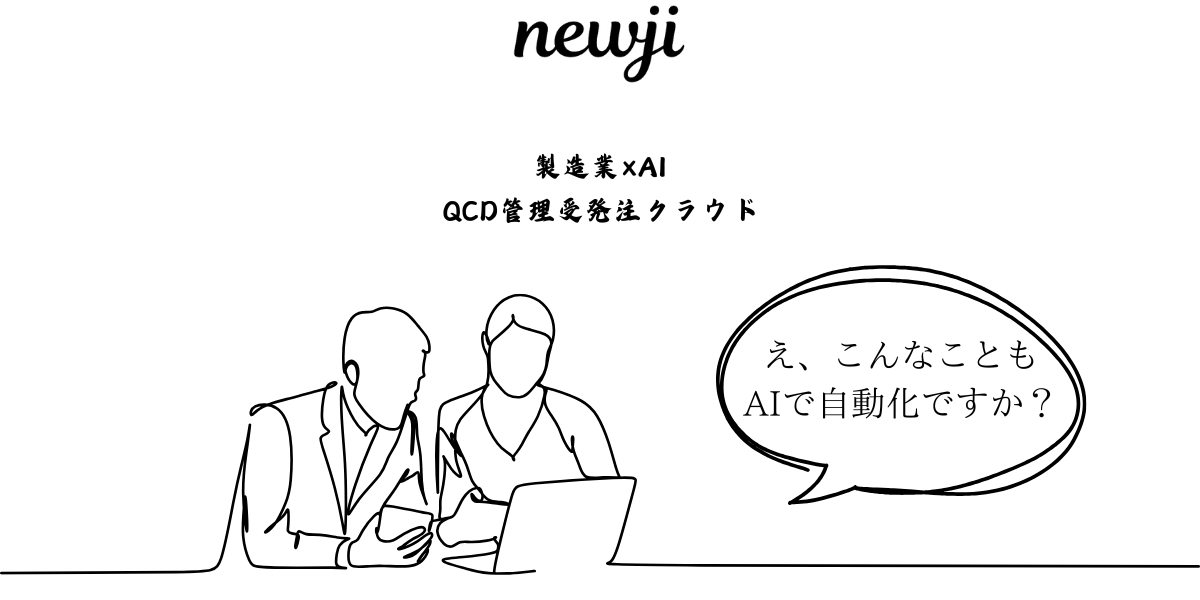
The difference between Factory Layout and Cell Production
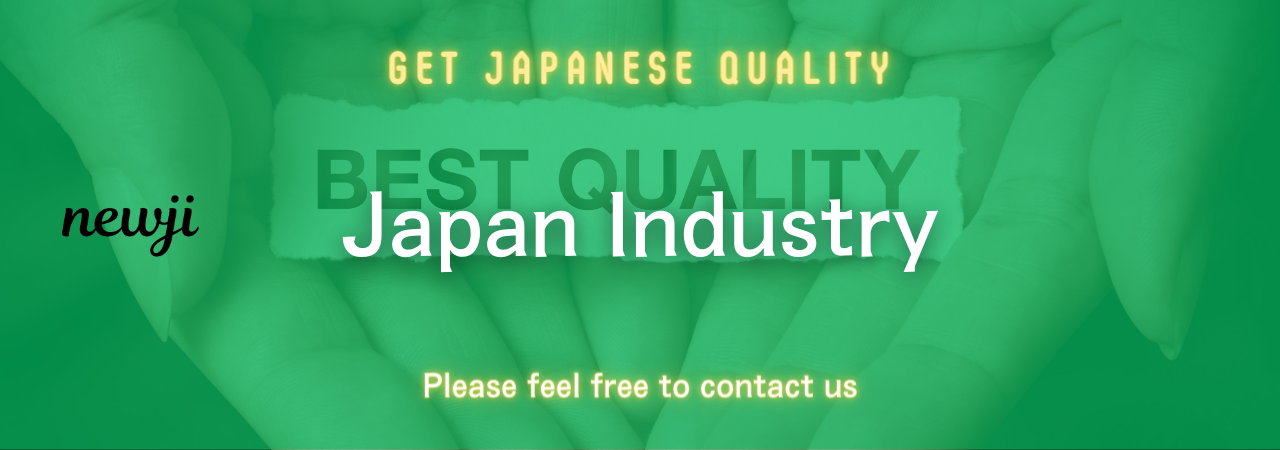
In the world of manufacturing, two popular production methods often come into discussion: factory layout and cell production.
These methods play a significant role in how goods are produced and can greatly impact efficiency, flexibility, and overall productivity.
Understanding the difference between these two production strategies can help businesses make informed decisions to optimize their operations.
目次
Understanding Factory Layout
Factory layout, also known as traditional manufacturing or process layout, refers to the arrangement of various machines, equipment, and work areas within a manufacturing facility.
This layout is typically designed to manage the flow of materials and products through the production process.
Key Characteristics of Factory Layout
A factory layout often involves grouping similar machines or processes in dedicated areas.
For instance, all assembly machines might be located in one section, while all packaging machines are in another.
This organization allows for specialization, as workers and machinery in each section can focus on specific tasks.
Another characteristic is the linear or sequential flow of production.
Materials move from one section to the next in a set order, which can create a smooth and predictable manufacturing process.
However, this type of layout can be less flexible.
Changing the production line or adding new products often requires significant reconfiguration, which can be time-consuming and costly.
Benefits of Factory Layout
One of the main advantages of a factory layout is efficiency in handling large-scale and repetitive production tasks.
Since similar processes are grouped together, it allows for streamlined operations and easy maintenance of equipment.
This layout also supports economies of scale, as producing a large quantity of similar items can reduce costs per unit.
Additionally, a factory layout can result in clear lines of responsibility among workers, which can enhance accountability and quality control.
Drawbacks of Factory Layout
Despite its benefits, the factory layout is not without its challenges.
A significant drawback is the lack of flexibility.
If customer demands change or customization is required, reconfiguring the existing layout can be difficult.
Furthermore, this setup can create bottlenecks if one section of the production process encounters issues, potentially halting the entire operation.
Understanding Cell Production
In contrast to the factory layout, cell production is a more flexible approach to manufacturing.
It involves organizing the production floor into self-contained units or “cells,” each responsible for a specific set of tasks.
Key Characteristics of Cell Production
Cell production breaks down the entire production process into smaller, manageable segments.
Each cell is equipped with all the necessary tools, machines, and workers to complete its portion of the job.
This can include anything from assembly to quality control to packaging.
Rather than moving through a linear process, products in cell production often flow through various cells in a dynamic and unpredictable manner.
This setup allows for greater customization and adaptability in response to changing demands.
Another key feature of cell production is teamwork.
Employees in each cell work closely together, often cross-training to handle multiple tasks.
This fosters a collaborative environment and can lead to greater job satisfaction.
Benefits of Cell Production
One of the main advantages of cell production is its flexibility.
Businesses can easily adapt to changes in customer demand or introduce new products without significant restructuring.
This method can also improve efficiency by minimizing the need for material transport between distant sections of a facility.
Cell production can reduce the likelihood of bottlenecks, as problems within one cell are less likely to impact other areas of production.
Additionally, the collaborative nature of this approach can lead to higher quality products, as workers in each cell take ownership and responsibility for their work.
Drawbacks of Cell Production
However, cell production is not without its challenges.
This approach can require a higher initial investment in training and equipment, as each cell needs to be adequately equipped and staffed.
Additionally, managing multiple cells can be complex, requiring careful coordination and oversight.
Another potential drawback is the need for skilled workers.
Since employees in each cell need to perform a variety of tasks, they must be well-trained and versatile, which can be a challenge in some labor markets.
Comparing Factory Layout and Cell Production
While both factory layout and cell production aim to streamline manufacturing, they do so in fundamentally different ways.
Efficiency vs. Flexibility
Factory layouts excel in efficiency for large-scale, repetitive production tasks.
Grouping similar processes and maintaining a linear flow can reduce costs and simplify maintenance.
On the other hand, cell production provides greater flexibility.
This method allows for easy adaptation to new products and changing customer demands.
Each cell operates independently, which can minimize the impact of disruptions and reduce bottlenecks.
Specialization vs. Collaboration
Factory layouts promote specialization.
Workers and machinery focus on specific tasks, often leading to improved proficiency and speed in those areas.
In contrast, cell production emphasizes collaboration.
Employees in each cell handle various tasks and work closely together, which can enhance job satisfaction and product quality.
Cost Considerations
Factory layouts may have lower initial costs.
Once set up, they benefit from economies of scale and predictable production flows.
Cell production, while potentially more complex and costly to establish, can offer long-term savings and efficiencies through its adaptable nature.
It also enables businesses to respond more quickly to market changes, which can be a competitive advantage.
Choosing the Right Approach for Your Business
Selecting between factory layout and cell production depends largely on the specific needs and goals of a business.
For companies focusing on high-volume, standardized products with minimal variation, a factory layout may be the most cost-effective and efficient choice.
This method leverages specialization and economies of scale to maximize productivity.
Conversely, for businesses that require flexibility, customization, and the ability to respond quickly to market changes, cell production might be the better option.
The collaborative and adaptable nature of cell production can provide a competitive edge in industries where customer preferences and product lines frequently evolve.
Ultimately, the choice between factory layout and cell production is not always clear-cut.
Some businesses may find a hybrid approach, combining elements of both methods, to be the most effective solution.
By carefully analyzing production needs, customer demands, and market dynamics, businesses can make an informed decision to optimize their manufacturing operations for success.
資料ダウンロード
QCD調達購買管理クラウド「newji」は、調達購買部門で必要なQCD管理全てを備えた、現場特化型兼クラウド型の今世紀最高の購買管理システムとなります。
ユーザー登録
調達購買業務の効率化だけでなく、システムを導入することで、コスト削減や製品・資材のステータス可視化のほか、属人化していた購買情報の共有化による内部不正防止や統制にも役立ちます。
NEWJI DX
製造業に特化したデジタルトランスフォーメーション(DX)の実現を目指す請負開発型のコンサルティングサービスです。AI、iPaaS、および先端の技術を駆使して、製造プロセスの効率化、業務効率化、チームワーク強化、コスト削減、品質向上を実現します。このサービスは、製造業の課題を深く理解し、それに対する最適なデジタルソリューションを提供することで、企業が持続的な成長とイノベーションを達成できるようサポートします。
オンライン講座
製造業、主に購買・調達部門にお勤めの方々に向けた情報を配信しております。
新任の方やベテランの方、管理職を対象とした幅広いコンテンツをご用意しております。
お問い合わせ
コストダウンが利益に直結する術だと理解していても、なかなか前に進めることができない状況。そんな時は、newjiのコストダウン自動化機能で大きく利益貢献しよう!
(Β版非公開)