- お役立ち記事
- Manufacturing Process of Heat Exchange Fins and Durability Reinforcement
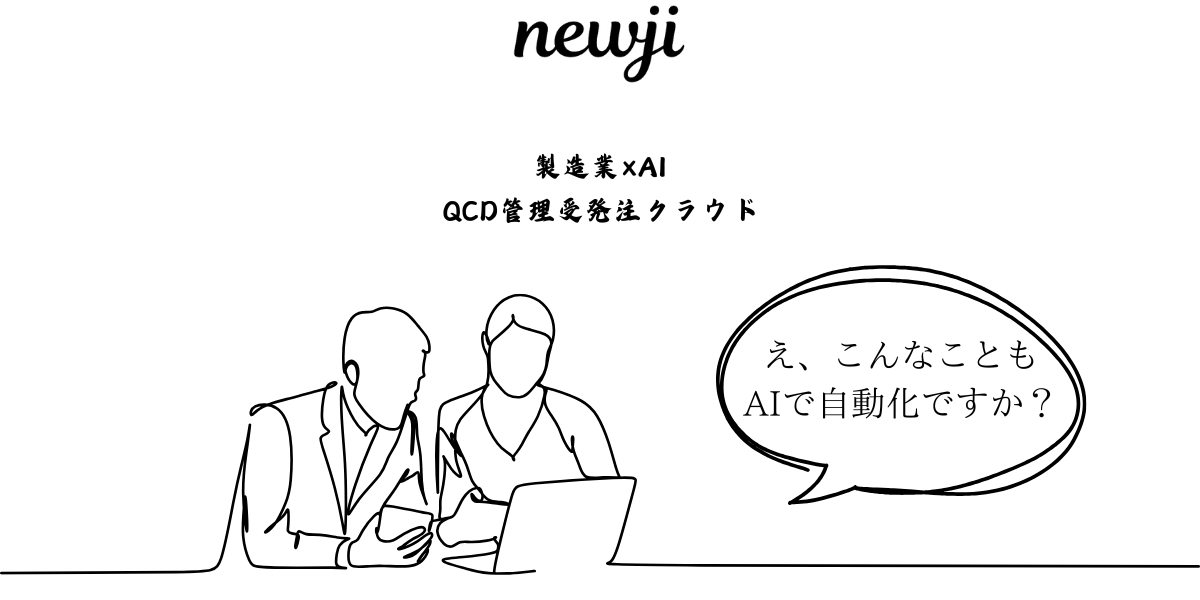
Manufacturing Process of Heat Exchange Fins and Durability Reinforcement
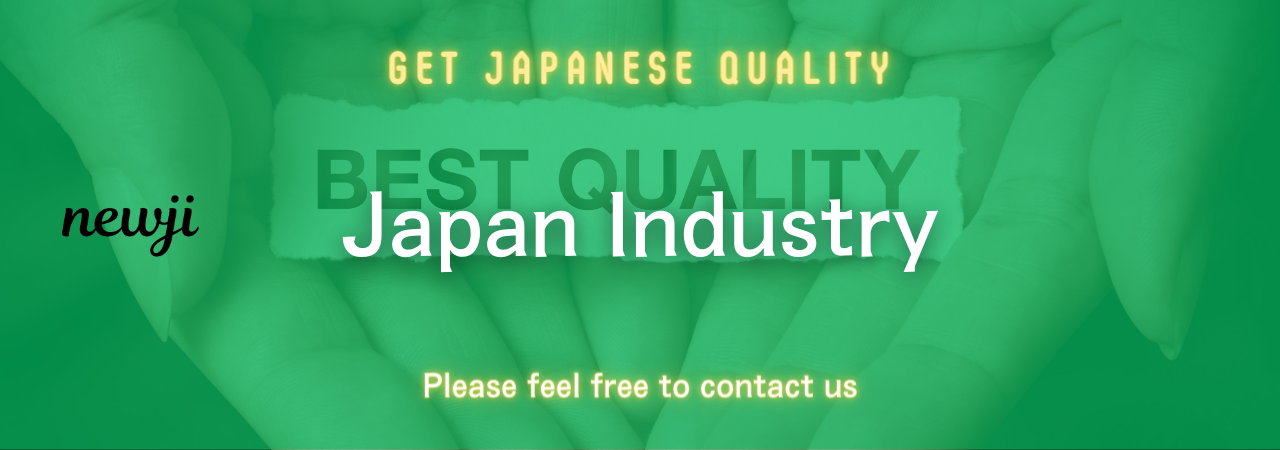
Heat exchange fins are critical components in many industries, playing a pivotal role in the efficiency and performance of heat exchangers.
These fins help manage temperature by transferring heat between media, ensuring optimal working conditions in various applications, from automotive radiators to air conditioning systems.
Understanding the manufacturing process of heat exchange fins and how their durability is reinforced can provide valuable insights into their functionality and reliability.
目次
Materials Used in Manufacturing Heat Exchange Fins
The choice of materials is the first important step in the manufacturing of heat exchange fins.
Common materials include aluminum, copper, and stainless steel.
Each material comes with its advantages depending on the end-use.
Aluminum
Aluminum is lightweight, corrosion-resistant, and has excellent thermal conductivity.
These properties make it perfect for applications where weight is a crucial factor, such as in automotive and aerospace industries.
Copper
Copper has the highest thermal conductivity among commonly used materials.
It is ideal for high-performance environments needing superior heat transfer capabilities, though it is heavier and more expensive than aluminum.
Stainless Steel
Stainless steel is used in applications that require higher strength and durability.
While its thermal conductivity isn’t as high as aluminum or copper, its resistance to corrosion and high strength-to-weight ratio make it a valuable option in aggressive environments.
Manufacturing Process of Heat Exchange Fins
The manufacturing process involves several stages, each crucial in ensuring the efficiency and durability of the fins.
Design and Precision Engineering
The first step involves meticulous design and precision engineering.
Engineers calculate the surface area needed for optimal heat transfer and design the fin’s shape accordingly.
Computational Fluid Dynamics (CFD) models are often employed to simulate airflow and heat exchange properties.
Material Cutting
Once the design is finalized, the selected material is cut into fin strips.
Advanced cutting technologies, like laser cutting or water jet cutting, are often used to ensure precision and minimize waste.
These technologies allow for intricate designs that enhance heat transfer efficiency.
Forming and Shaping
The next step is forming and shaping the cut material into fin structures.
Techniques like stamping, rolling, and corrugation are used to create the desired fin patterns.
The forming process directly influences the surface area and, consequently, the heat exchange efficiency.
Precision dies and molds ensure consistent and accurate shaping.
Surface Treatment
Surface treatment is critical in enhancing the durability and performance of heat exchange fins.
Processes like anodizing, electroplating, or powder coating are employed to improve corrosion resistance and thermal conductivity.
For example, aluminum fins may undergo anodization to form a protective oxide layer, whereas copper fins could be electroplated to enhance their durability.
Assembly
Once treated, the fins are assembled into the heat exchanger core.
This involves stacking or attaching the fins to tubes or plates that carry the fluid or gas.
Assembly must be precise to ensure optimal spacing and secure attachment.
Brazing, welding, or adhesive bonding techniques are commonly used to achieve this.
Reinforcing Durability
Durability is a critical factor for heat exchange fins, especially in demanding applications.
Several strategies enhance their longevity and resistance to harsh conditions.
Protective Coatings
Applying protective coatings is one of the most effective ways to reinforce durability.
These coatings not only protect against corrosion and wear but also enhance thermal performance.
Epoxy coatings, for instance, are widely used for their ability to withstand high temperatures and aggressive chemicals.
Corrosion Resistance
Materials inherently resistant to corrosion are also chosen to increase durability.
For example, aluminum, when anodized, forms a tough oxide layer that significantly improves its resistance to corrosion.
Copper-nickel alloys are another option for highly corrosive environments, combining excellent thermal conductivity with superior corrosion resistance.
Mechanical Strengthening
Increasing the mechanical strength of the fins can also reinforce durability.
This can be achieved through material treatments such as work hardening or heat treatments, which improve the structural integrity.
Fin geometry and thickness are also optimized to balance strength with thermal performance.
Quality Control
Quality control is paramount throughout the manufacturing process.
Each fin undergoes stringent inspections to ensure it meets design specifications and performance criteria.
Non-destructive testing methods, like X-ray or ultrasonic inspections, are often employed to detect any flaws or defects that could compromise durability.
Environmental Considerations
Manufacturers increasingly integrate environmental considerations into producing heat exchange fins.
This includes using eco-friendly materials and coatings, optimizing resource efficiency, and implementing recycling processes.
Sustainable practices enhance the product’s durability and reduce the overall environmental footprint.
Conclusion
The manufacturing process of heat exchange fins is a complex and precise operation, involving careful material selection, advanced cutting and forming techniques, and rigorous quality control.
Understanding these steps offers valuable insight into how these critical components function effectively and reliably in various applications.
Durability reinforcement strategies, from protective coatings to mechanical strengthening, ensure that heat exchange fins can withstand the demanding conditions they often face, ensuring long-term efficiency and performance.
資料ダウンロード
QCD調達購買管理クラウド「newji」は、調達購買部門で必要なQCD管理全てを備えた、現場特化型兼クラウド型の今世紀最高の購買管理システムとなります。
ユーザー登録
調達購買業務の効率化だけでなく、システムを導入することで、コスト削減や製品・資材のステータス可視化のほか、属人化していた購買情報の共有化による内部不正防止や統制にも役立ちます。
NEWJI DX
製造業に特化したデジタルトランスフォーメーション(DX)の実現を目指す請負開発型のコンサルティングサービスです。AI、iPaaS、および先端の技術を駆使して、製造プロセスの効率化、業務効率化、チームワーク強化、コスト削減、品質向上を実現します。このサービスは、製造業の課題を深く理解し、それに対する最適なデジタルソリューションを提供することで、企業が持続的な成長とイノベーションを達成できるようサポートします。
オンライン講座
製造業、主に購買・調達部門にお勤めの方々に向けた情報を配信しております。
新任の方やベテランの方、管理職を対象とした幅広いコンテンツをご用意しております。
お問い合わせ
コストダウンが利益に直結する術だと理解していても、なかなか前に進めることができない状況。そんな時は、newjiのコストダウン自動化機能で大きく利益貢献しよう!
(Β版非公開)