- お役立ち記事
- The difference between Equipment Diagnosis and Equipment Evaluation
The difference between Equipment Diagnosis and Equipment Evaluation
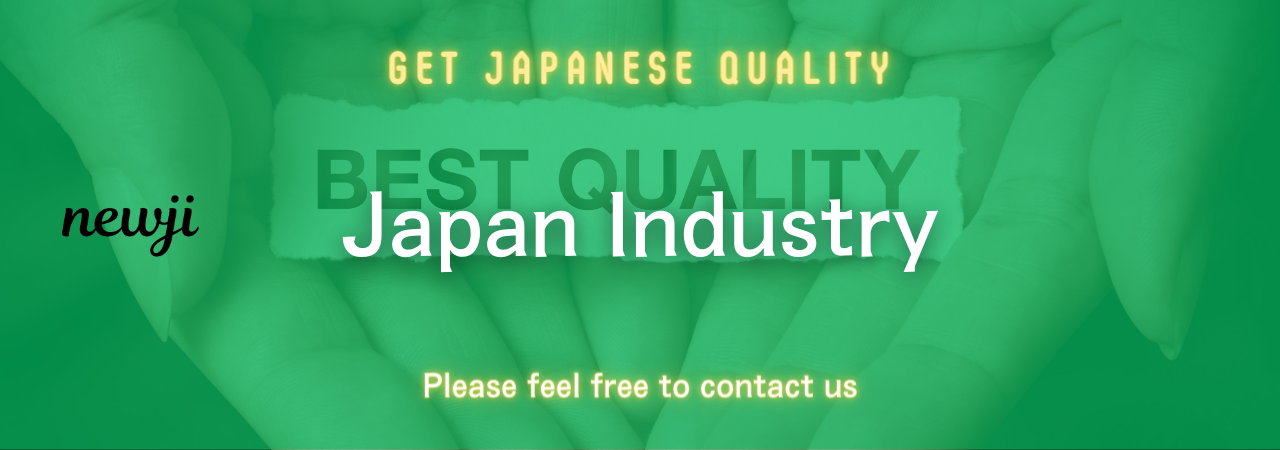
In the world of industrial maintenance and quality assurance, two terms often arise: equipment diagnosis and equipment evaluation. Although these terms might seem interchangeable, they refer to distinctly different processes. To get a clearer understanding, let’s dive into the fundamental differences between equipment diagnosis and equipment evaluation, and why each is crucial in their own right.
目次
What Is Equipment Diagnosis?
Equipment diagnosis is akin to a medical diagnosis for machinery. It involves identifying the root cause of a machine’s malfunction or a decrease in its performance. Imagine a technician acting as a doctor for machines. They examine every aspect, test various components, and pinpoint exactly what’s wrong.
Purpose of Equipment Diagnosis
The primary goal of equipment diagnosis is to detect issues as soon as they arise. By identifying the problem early, it prevents minor faults from escalating into more severe, costly repairs. Immediate identification also helps in minimizing downtime, keeping production schedules on track.
Methods Used in Equipment Diagnosis
Various techniques and tools are employed in equipment diagnosis. Some common methods include:
1. **Visual inspection**: Technicians look for visible signs of wear and tear or damage.
2. **Performance testing**: Monitoring the machine’s output to spot anomalies.
3. **Condition monitoring**: Using sensors and diagnostic software to continuously assess machine health.
4. **Non-destructive testing (NDT)**: Techniques like ultrasound or X-rays to inspect internal components without causing damage.
Benefits of Equipment Diagnosis
The advantages of conducting equipment diagnosis are numerous:
– **Extended Equipment Life**: Early detection of issues enables timely repairs, prolonging the lifespan of machinery.
– **Cost Reduction**: Preventative measures and minor fixes are less expensive than major overhauls or replacements.
– **Safety Improvement**: Faulty machines can pose significant safety risks. Diagnosis ensures that equipment operates safely.
– **Efficiency Boost**: Well-maintained machinery operates more efficiently, leading to better productivity.
What Is Equipment Evaluation?
While equipment diagnosis focuses on identifying existing problems, equipment evaluation is more about assessing the overall performance and value of machinery. It’s like appraising a piece of equipment to gauge its worth and functionality over its lifespan.
Purpose of Equipment Evaluation
The aim of equipment evaluation is to determine the current state, the performance efficiency, and the remaining useful life of equipment. It’s a comprehensive assessment that aids in making informed decisions about maintenance schedules, upgrades, or replacements.
Methods Used in Equipment Evaluation
Equipment evaluation employs a different set of techniques compared to diagnosis. Key methods include:
1. **Performance benchmarking**: Comparing the machinery’s performance against industry standards or similar equipment.
2. **Historical data analysis**: Reviewing maintenance logs, repair records, and usage history.
3. **Efficiency testing**: Measuring energy consumption, output rates, and other performance metrics.
4. **Economic analysis**: Assessing the cost-effectiveness of the equipment in terms of operational costs and potential return on investment (ROI).
Benefits of Equipment Evaluation
Conducting thorough equipment evaluations has several benefits:
– **Informed Decision-Making**: Helps in planning replacements, purchasing new equipment, or upgrading existing machinery.
– **Optimized Budget Allocation**: Prioritizes spending on the most critical and impactful repairs or upgrades.
– **Improved Performance**: Identifies areas for improvement, helping to enhance efficiency and productivity.
– **Risk Management**: Evaluates potential risks and helps in developing strategies to mitigate them.
Key Differences Between Equipment Diagnosis and Equipment Evaluation
Understanding the distinction between equipment diagnosis and equipment evaluation is crucial for effective industrial maintenance and management.
Focus Areas
Equipment diagnosis zeroes in on identifying specific issues affecting machinery’s performance or causing faults.
In contrast, equipment evaluation takes a broader view, assessing the overall performance, efficiency, and value of the machinery.
Timing
Diagnosis is typically performed on a reactive basis when issues arise, or as part of routine maintenance checks.
Evaluation, on the other hand, is usually proactive, conducted as part of a strategic plan for asset management and lifecycle planning.
Outcome
The result of a diagnosis is a detailed understanding of the cause of problems, leading to targeted repairs.
Evaluation provides a comprehensive performance report, offering insights into when to maintain, upgrade, or replace equipment.
Choosing the Right Approach
Deciding between equipment diagnosis and equipment evaluation sometimes depends on the specific needs of the business and the machinery in question.
When to Opt for Equipment Diagnosis
Diagnosis is essential when machinery begins to show signs of malfunction or when there is an unexplained drop in performance. It’s also crucial during regular maintenance routines to ensure that minor issues are caught early.
When to Conduct Equipment Evaluation
Evaluation is particularly useful during audits, before making large investments, or when creating long-term maintenance plans. It’s also valuable when equipment is aging, helping businesses decide between continued maintenance or replacement.
Integrating Diagnosis and Evaluation
Both equipment diagnosis and equipment evaluation play pivotal roles in maintaining optimal machine performance and longevity. Integrating both approaches can yield the best results – regular diagnostic checks can catch and fix issues early, while periodic evaluations ensure that the equipment remains effective and cost-efficient throughout its lifecycle.
Successful integration requires a strategic maintenance plan that includes both reactive and proactive measures. By doing so, businesses can ensure that their machinery operates at peak performance, downtime is minimized, and long-term costs are reduced.
In conclusion, while equipment diagnosis and equipment evaluation serve different purposes, they are both essential in the world of industrial maintenance.
By understanding their distinct roles and benefits, businesses can implement a comprehensive maintenance strategy that not only addresses current issues but also plans for future needs and optimizes overall performance. This balanced approach ultimately supports longevity, efficiency, and cost-effectiveness in machinery management.
資料ダウンロード
QCD調達購買管理クラウド「newji」は、調達購買部門で必要なQCD管理全てを備えた、現場特化型兼クラウド型の今世紀最高の購買管理システムとなります。
ユーザー登録
調達購買業務の効率化だけでなく、システムを導入することで、コスト削減や製品・資材のステータス可視化のほか、属人化していた購買情報の共有化による内部不正防止や統制にも役立ちます。
NEWJI DX
製造業に特化したデジタルトランスフォーメーション(DX)の実現を目指す請負開発型のコンサルティングサービスです。AI、iPaaS、および先端の技術を駆使して、製造プロセスの効率化、業務効率化、チームワーク強化、コスト削減、品質向上を実現します。このサービスは、製造業の課題を深く理解し、それに対する最適なデジタルソリューションを提供することで、企業が持続的な成長とイノベーションを達成できるようサポートします。
オンライン講座
製造業、主に購買・調達部門にお勤めの方々に向けた情報を配信しております。
新任の方やベテランの方、管理職を対象とした幅広いコンテンツをご用意しております。
お問い合わせ
コストダウンが利益に直結する術だと理解していても、なかなか前に進めることができない状況。そんな時は、newjiのコストダウン自動化機能で大きく利益貢献しよう!
(Β版非公開)