- お役立ち記事
- Selecting Materials and Tools for 5S Initiatives
Selecting Materials and Tools for 5S Initiatives
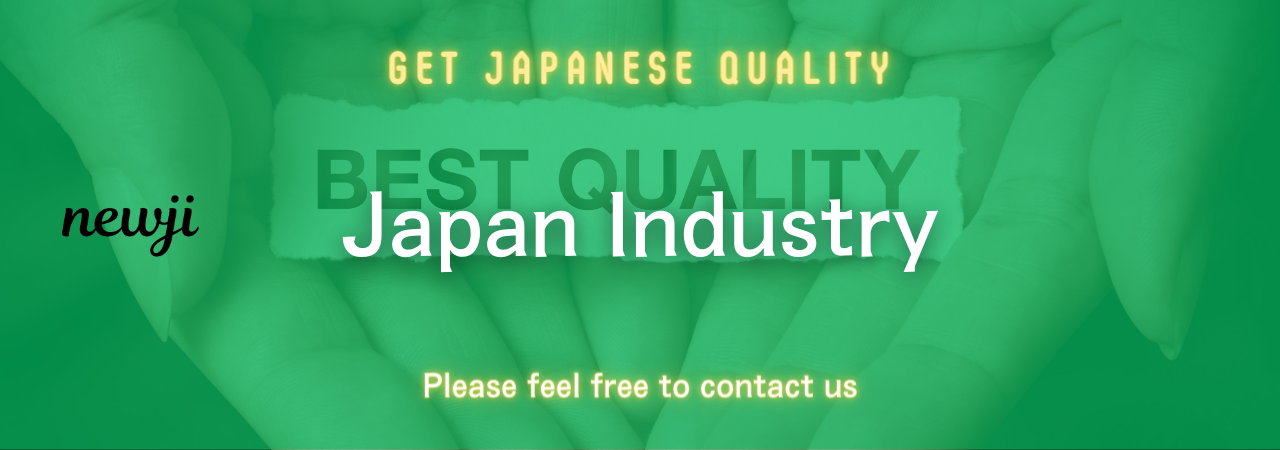
The 5S methodology stands as a cornerstone of workplace organization and efficiency.
Prominent in numerous industries, from manufacturing to healthcare, this framework involves five essential steps: Sort, Set in Order, Shine, Standardize, and Sustain.
Central to the success of 5S initiatives is the selection of appropriate materials and tools.
These elements can greatly influence the outcome of your organizational goals.
This article delves into how to choose the best materials and tools for your 5S initiatives.
目次
Understanding 5S Methodology
Before diving into the material selection, it’s crucial to briefly recap what each step of the 5S methodology entails.
Understanding these steps will enable you to choose the right tools that align with each phase.
Sort
This step involves distinguishing between necessary and unnecessary items in the work area.
Items not needed are removed.
Set in Order
Once you’ve sorted, the next step is to arrange necessary items so they are easy to find and use.
Shine
This phase involves cleaning the workspace and keeping everything orderly.
Standardize
The practices from the first three steps are standardized into regular tasks and routines.
Sustain
The final step involves maintaining and reviewing standards to ensure the success of the 5S program.
Choosing Materials for 5S
The choice of materials can make or break the efficacy of a 5S initiative.
Here are some key points to consider.
Durability
One of the primary factors to consider is the durability of the materials.
Choosing long-lasting materials ensures that the organization and cleaning efforts remain effective over time.
For example, heavy-duty plastic bins are more durable compared to cardboard boxes.
Visibility
Materials that enhance visibility can help immensely in the Set in Order phase.
For instance, clear plastic containers make it easy to identify contents at a glance.
Label holders, adhesive labels, or color-coded systems can also help in this regard.
Standardization
While selecting materials, consider items that can easily be standardized.
Standardized bins, shelves, and labels make it easier to maintain consistency across various areas.
They simplify the process of keeping items in their designated places.
Choosing Tools for 5S
Similarly, choosing the right tools is crucial for effective implementation.
These tools facilitate the different phases of 5S.
Labeling Tools
An effective labeling system is indispensable for the Set in Order and Standardize phases.
Label printers, adhesive labels, and tag holders are vital tools.
They help in easily identifying and categorizing items.
Cleaning Equipment
The Shine phase requires high-quality cleaning tools.
Microfiber cloths, cleaning sprays, floor cleaning machines, and even air blowers can ensure that the workspace remains spotless.
Storage Solutions
Efficient storage solutions are central to maintaining an organized workspace.
Racks, shelves, cabinets, and bins with clear labeling systems help in easy access and storage of items.
Software Tools
Digital tools can also support 5S initiatives.
Software programs for inventory management and routine checklists can streamline the Standardize and Sustain phases.
These tools help in maintaining records and scheduling regular audits.
Implementing 5S with the Right Tools and Materials
Choosing the right materials and tools is half the battle.
Implementing them effectively is equally important.
Initial Assessment
Before implementing 5S, conduct an initial assessment of the workspace.
Identify areas that require immediate attention and list the necessary materials and tools.
This will guide your initial purchases and planning.
Training Employees
Equip your team with the knowledge to use the selected materials and tools effectively.
Training sessions can include demonstrations and hands-on practice.
Training ensures everyone is on the same page, making the transition smoother.
Regular Audits
Regular audits help in assessing the effectiveness of the 5S program.
Using checklists and digital tools can simplify this process.
Audits ensure that the chosen materials and tools are used effectively and adjustments are made when needed.
Feedback Mechanisms
Establish feedback mechanisms to gauge the practicality and efficiency of the selected materials and tools.
This can help in making necessary adjustments, ensuring the program’s long-term success.
Case Studies and Success Stories
Learning from successful 5S initiatives can provide insights into effective material and tool selection.
For example, a renowned automobile manufacturing company implemented 5S using color-coded bins, label printers, and an integrated inventory management software.
Their operational efficiency improved, leading to better time management and reduced waste.
Another example is a hospital that successfully implemented 5S through durable, labeled storage solutions and routine training.
They saw a significant improvement in inventory management and quicker access to medical supplies.
Conclusion
Selecting the right materials and tools for 5S initiatives is a pivotal step toward achieving organizational efficiency.
By focusing on durability, visibility, and standardization, and implementing the right tools for labeling, cleaning, and storage, companies can optimize their workspaces.
Regular audits, employee training, and feedback mechanisms further enhance the effectiveness of the 5S program.
By drawing inspiration from successful case studies, companies can better tailor their 5S initiatives to meet specific goals.
The journey toward an organized, efficient workspace begins with the right choices—starting with your materials and tools.
資料ダウンロード
QCD調達購買管理クラウド「newji」は、調達購買部門で必要なQCD管理全てを備えた、現場特化型兼クラウド型の今世紀最高の購買管理システムとなります。
ユーザー登録
調達購買業務の効率化だけでなく、システムを導入することで、コスト削減や製品・資材のステータス可視化のほか、属人化していた購買情報の共有化による内部不正防止や統制にも役立ちます。
NEWJI DX
製造業に特化したデジタルトランスフォーメーション(DX)の実現を目指す請負開発型のコンサルティングサービスです。AI、iPaaS、および先端の技術を駆使して、製造プロセスの効率化、業務効率化、チームワーク強化、コスト削減、品質向上を実現します。このサービスは、製造業の課題を深く理解し、それに対する最適なデジタルソリューションを提供することで、企業が持続的な成長とイノベーションを達成できるようサポートします。
オンライン講座
製造業、主に購買・調達部門にお勤めの方々に向けた情報を配信しております。
新任の方やベテランの方、管理職を対象とした幅広いコンテンツをご用意しております。
お問い合わせ
コストダウンが利益に直結する術だと理解していても、なかなか前に進めることができない状況。そんな時は、newjiのコストダウン自動化機能で大きく利益貢献しよう!
(Β版非公開)