- お役立ち記事
- The difference between Reorder Point System and Periodic Reorder System
The difference between Reorder Point System and Periodic Reorder System
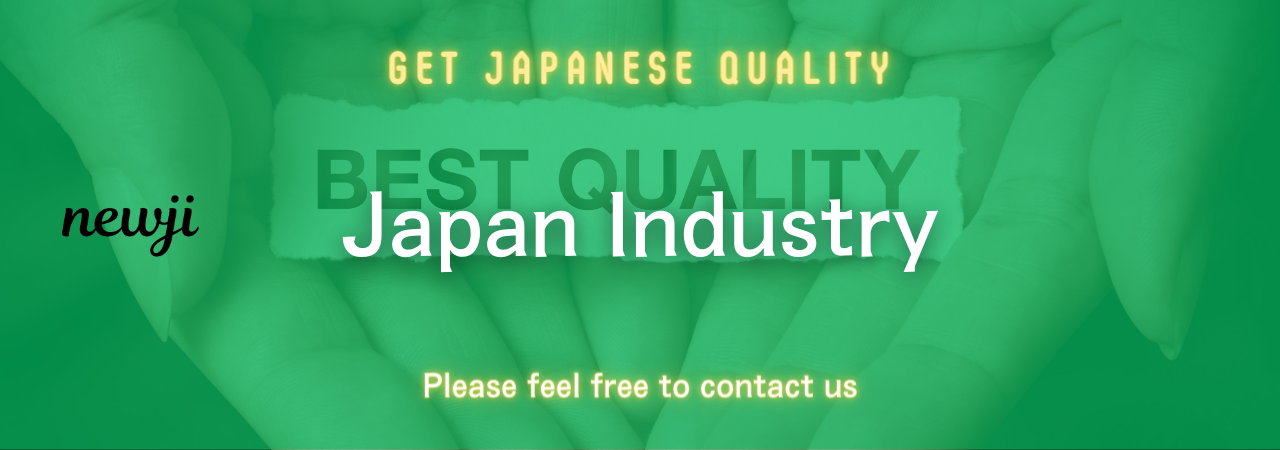
Understanding the difference between the Reorder Point System and the Periodic Reorder System is essential for businesses managing inventory.
These two inventory control systems each have their own methods and benefits, and choosing the right one can enhance operational efficiency.
Let’s dive into these topics:
目次
What is the Reorder Point System?
The Reorder Point System helps businesses determine the optimal time to restock inventory.
A reorder point (ROP) is a predefined level of inventory that triggers the need to reorder.
Businesses calculate this point by considering the average daily usage and lead time.
This method ensures that stock levels never fall below the critical threshold necessary to meet customer demand.
How the Reorder Point is Calculated
To calculate the reorder point, you need to know two things: average daily usage and lead time.
Average daily usage is the amount of inventory used each day.
Lead time is the time it takes for a new order to arrive once it’s placed.
The formula for the reorder point is:
Reorder Point = (Average Daily Usage) x (Lead Time)
For example, if your average daily usage is 50 units and the lead time is 5 days, your reorder point would be 250 units.
When your inventory level reaches 250 units, it’s time to place a new order.
Advantages of the Reorder Point System
One significant advantage of the Reorder Point System is that it allows for continuous monitoring of inventory levels.
This continuous monitoring helps prevent stockouts and overstock situations.
Additionally, it is relatively simple to implement and understand, making it an excellent choice for businesses of all sizes.
What is the Periodic Reorder System?
The Periodic Reorder System operates on a fixed schedule rather than a specific inventory level.
In this system, inventory levels are checked at regular intervals, such as weekly or monthly.
During these checks, any inventory that falls below a predetermined level is replenished.
How to Implement a Periodic Reorder System
To implement this system, businesses first define the interval at which they will review inventory levels.
Next, a target inventory level is determined.
During each review period, the business assesses its current inventory and places an order to bring stock levels back up to the target.
For example, if a business reviews inventory every month and aims to maintain an inventory level of 1,000 units, it will reorder monthly to reach that target level.
Advantages of the Periodic Reorder System
One of the primary benefits of the Periodic Reorder System is its simplicity.
Because inventory is reviewed at regular intervals, businesses can plan their ordering schedules more precisely.
This system also allows for bulk ordering, which can result in cost savings due to economies of scale.
Comparing the Two Systems
When deciding between the Reorder Point System and the Periodic Reorder System, businesses must consider their specific needs and circumstances.
Both systems offer unique benefits and can be effective in different situations.
Flexibility vs. Routine
The Reorder Point System is highly flexible, allowing businesses to place orders whenever inventory levels reach the reorder point.
This flexibility helps prevent stockouts and ensures a continuous supply of products.
Conversely, the Periodic Reorder System relies on a fixed schedule.
While this can be less responsive to fluctuations in demand, it offers the advantage of predictability.
Businesses can prepare for orders at regular intervals, which helps streamline processes.
Stock Levels
The Reorder Point System focuses on maintaining minimum stock levels to meet demand.
It can help reduce carrying costs and storage requirements by avoiding excess inventory.
However, this system requires constant monitoring, which can be resource-intensive.
On the other hand, the Periodic Reorder System aims to maintain a consistent target inventory level.
This can lead to higher inventory levels overall, but it simplifies the ordering process and reduces the need for continuous monitoring.
Responding to Demand
If your business experiences highly variable demand, the Reorder Point System may be more appropriate.
It allows for a quicker response to changes in customer needs.
In contrast, the Periodic Reorder System may be more suitable for businesses with stable and predictable demand patterns.
Regular intervals for ordering can be more manageable and less reactive.
Choosing the Right System for Your Business
To choose the right inventory control system, evaluate your inventory patterns, demand variability, and resource availability.
Consider whether flexibility or routine is more important for your operations.
Both systems have their strengths, and some businesses may even use a hybrid approach that combines elements of each.
Implementing and Adjusting
Once you choose a system, implementation involves setting up the necessary calculations, schedules, or monitoring processes.
Be prepared to review and adjust your strategy as needed to ensure it continues to meet your business needs.
Regular audits and performance checks can help identify areas for improvement and ensure optimal inventory management.
Conclusion
The Reorder Point System and the Periodic Reorder System both play vital roles in managing inventory effectively.
Understanding the difference between the two can help you make an informed decision that aligns with your business goals.
By carefully considering your specific requirements, you can select the system that best supports your operations, ensuring efficient and cost-effective inventory management.
資料ダウンロード
QCD調達購買管理クラウド「newji」は、調達購買部門で必要なQCD管理全てを備えた、現場特化型兼クラウド型の今世紀最高の購買管理システムとなります。
ユーザー登録
調達購買業務の効率化だけでなく、システムを導入することで、コスト削減や製品・資材のステータス可視化のほか、属人化していた購買情報の共有化による内部不正防止や統制にも役立ちます。
NEWJI DX
製造業に特化したデジタルトランスフォーメーション(DX)の実現を目指す請負開発型のコンサルティングサービスです。AI、iPaaS、および先端の技術を駆使して、製造プロセスの効率化、業務効率化、チームワーク強化、コスト削減、品質向上を実現します。このサービスは、製造業の課題を深く理解し、それに対する最適なデジタルソリューションを提供することで、企業が持続的な成長とイノベーションを達成できるようサポートします。
オンライン講座
製造業、主に購買・調達部門にお勤めの方々に向けた情報を配信しております。
新任の方やベテランの方、管理職を対象とした幅広いコンテンツをご用意しております。
お問い合わせ
コストダウンが利益に直結する術だと理解していても、なかなか前に進めることができない状況。そんな時は、newjiのコストダウン自動化機能で大きく利益貢献しよう!
(Β版非公開)