- お役立ち記事
- Manufacturing Process of Driveshafts and Durability Reinforcement
Manufacturing Process of Driveshafts and Durability Reinforcement
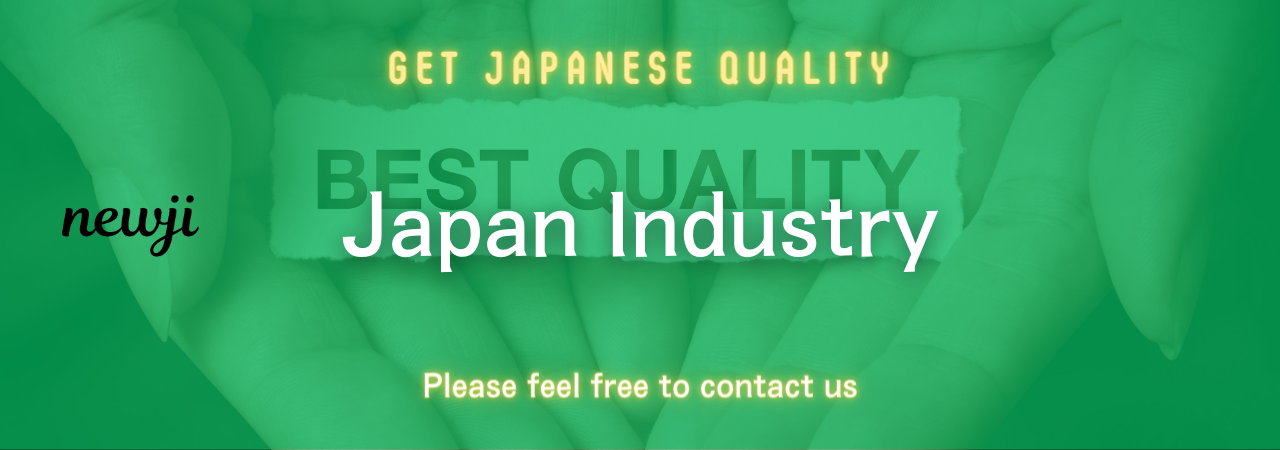
The driveshaft is a crucial component in the automotive industry, responsible for transmitting torque and rotation to the wheels, ensuring the vehicle’s smooth operation.
Understanding the intricacies of its manufacturing process and how its durability can be reinforced is essential for optimizing performance and longevity.
目次
Raw Material Selection
The process begins with the careful selection of raw materials.
Steel or aluminum are commonly chosen due to their strength and lightweight properties, respectively.
The quality of these materials directly impacts the driveshaft’s performance, making it imperative to source high-grade metals.
These materials are then subjected to rigorous quality checks, ensuring they meet industry standards.
Forming and Shaping
Once the raw materials are approved, they move on to the forming and shaping stage.
This involves multiple processes, including:
Rolling
The metal is passed through rollers that shape it into a tube.
This stage is vital for achieving the desired diameter and thickness, which are critical for the driveshaft’s performance.
Drawing
Drawing involves pulling the metal through a die to reduce its diameter and increase its length.
This process enhances the metal’s tensile strength, making it more durable.
Heat Treatment
Heat treatment is essential for enhancing the material’s mechanical properties.
It involves heating the metal to high temperatures before cooling it rapidly.
This process, known as quenching, significantly improves the driveshaft’s strength and toughness.
Precision Machining
After forming and shaping, the driveshaft undergoes precision machining.
This stage involves several steps:
CNC Machining
Computer Numerical Control (CNC) machines are used to achieve high levels of precision during this phase.
These machines cut, drill, and shape the driveshaft to exact specifications, ensuring each unit is uniform.
Balancing
Balancing is a critical step to ensure smooth operation.
Any imbalance can lead to vibrations and uneven wear, compromising the driveshaft’s performance.
Specialized equipment is used to detect imbalances and correct them, ensuring the driveshaft operates smoothly.
Welding and Assembly
Welding connects different parts of the driveshaft, such as the yokes and flanges.
High-quality welding techniques, such as friction welding and MIG welding, are employed to ensure strong and durable joints.
After welding, the components are assembled.
This includes attaching universal joints (U-joints) or constant velocity (CV) joints, which allow the driveshaft to transmit torque at different angles.
Proper assembly ensures the driveshaft functions effectively under various operating conditions.
Quality Control and Testing
Quality control is integral to the manufacturing process.
Each driveshaft undergoes a series of tests to ensure it meets specified standards:
Non-Destructive Testing (NDT)
NDT methods, such as ultrasonic testing and magnetic particle inspection, are used to detect any internal defects without damaging the driveshaft.
Fatigue Testing
Fatigue testing involves subjecting the driveshaft to repeated stress cycles to evaluate its durability.
This test helps identify potential failure points and ensures the driveshaft can withstand prolonged use.
Torsional Testing
Torsional testing measures the driveshaft’s ability to transmit torque without twisting or deforming.
This test ensures the driveshaft can handle the required power output.
Durability Reinforcement
To enhance the durability of driveshafts, several reinforcement techniques are employed:
Surface Treatment
Surface treatments, such as shot peening and nitriding, are used to strengthen the driveshaft’s surface.
Shot peening involves bombarding the surface with small spherical particles to induce compressive stress, increasing fatigue resistance.
Nitriding introduces nitrogen into the surface, forming a hard, wear-resistant layer.
Protective Coatings
Protective coatings, such as zinc plating and epoxy coatings, are applied to prevent corrosion and wear.
These coatings extend the driveshaft’s lifespan, especially in harsh operating environments.
Composite Materials
In some cases, composite materials, like carbon fiber, are used to manufacture driveshafts.
These materials offer superior strength-to-weight ratios, enhancing performance and durability.
Final Inspection and Packaging
Once all manufacturing and reinforcement processes are completed, the driveshaft undergoes a final inspection.
This ensures all specifications and quality standards are met.
Any deviations are corrected before packaging.
Proper packaging is essential to protect the driveshaft during transportation and storage.
Each driveshaft is carefully packed to avoid damage, ensuring it reaches its destination in optimal condition.
The manufacturing process of driveshafts is a complex series of meticulously controlled steps, from raw material selection to final inspection.
Employing advanced techniques and stringent quality control measures ensure the production of high-performance, durable driveshafts.
By understanding and implementing these processes, manufacturers can produce driveshafts capable of withstanding the rigors of automotive applications, ensuring reliability and safety for the end users.
資料ダウンロード
QCD調達購買管理クラウド「newji」は、調達購買部門で必要なQCD管理全てを備えた、現場特化型兼クラウド型の今世紀最高の購買管理システムとなります。
ユーザー登録
調達購買業務の効率化だけでなく、システムを導入することで、コスト削減や製品・資材のステータス可視化のほか、属人化していた購買情報の共有化による内部不正防止や統制にも役立ちます。
NEWJI DX
製造業に特化したデジタルトランスフォーメーション(DX)の実現を目指す請負開発型のコンサルティングサービスです。AI、iPaaS、および先端の技術を駆使して、製造プロセスの効率化、業務効率化、チームワーク強化、コスト削減、品質向上を実現します。このサービスは、製造業の課題を深く理解し、それに対する最適なデジタルソリューションを提供することで、企業が持続的な成長とイノベーションを達成できるようサポートします。
オンライン講座
製造業、主に購買・調達部門にお勤めの方々に向けた情報を配信しております。
新任の方やベテランの方、管理職を対象とした幅広いコンテンツをご用意しております。
お問い合わせ
コストダウンが利益に直結する術だと理解していても、なかなか前に進めることができない状況。そんな時は、newjiのコストダウン自動化機能で大きく利益貢献しよう!
(Β版非公開)