- お役立ち記事
- The difference between Visual Inspection and Dimensional Inspection
The difference between Visual Inspection and Dimensional Inspection
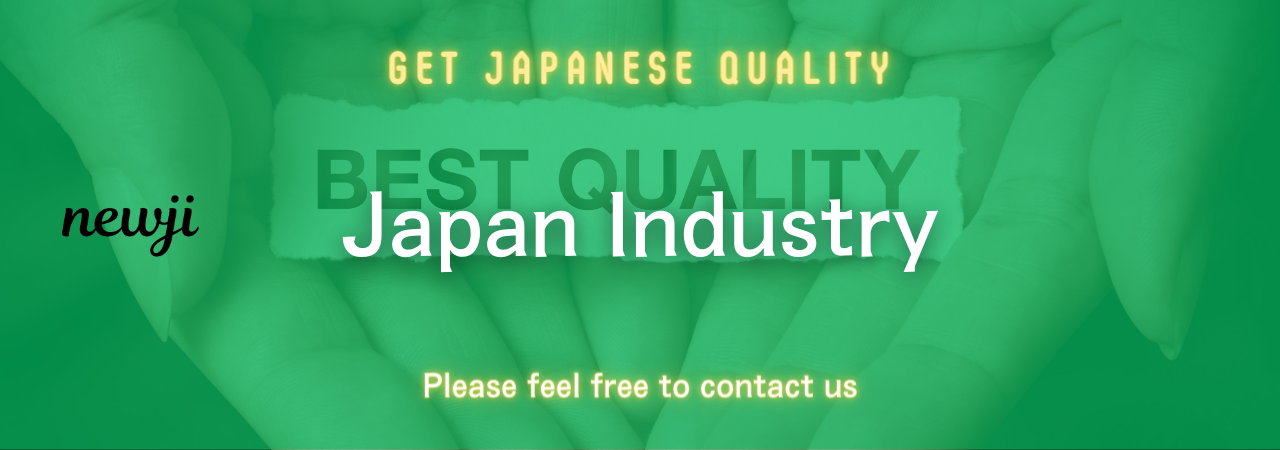
When it comes to ensuring the quality and consistency of manufactured products, quality control is paramount.
There are several methods in place to ensure that products meet certain standards and specifications.
Among these, visual inspection and dimensional inspection are two fundamental techniques employed across various industries.
Understanding the difference between these two inspection methods is crucial for anyone involved in manufacturing and quality control.
Let’s dive deeper into how visual inspection and dimensional inspection differ and the roles they play.
目次
What is Visual Inspection?
Visual inspection is exactly what it sounds like: examining an item with the naked eye to check for defects.
This method is one of the oldest and most straightforward forms of inspection.
Quality control personnel use their eyes to look for surface flaws, such as scratches, dents, discoloration, and any other visible imperfections.
Applications of Visual Inspection
Visual inspection is commonly used in industries such as automotive, aerospace, and electronics, where surface appearance can be critical.
For example, a scratch on a car’s paint job or a blemish on a smartphone screen can be noticeable and unacceptable to consumers.
Therefore, these industries rely heavily on visual inspection to ensure that their products look perfect.
Advantages of Visual Inspection
One of the main advantages of visual inspection is its simplicity.
It doesn’t require expensive equipment or extensive training, making it a cost-effective method for detecting surface-level defects.
Additionally, visual inspection can often be done quickly, allowing for rapid processing of items on a production line.
Another advantage is its versatility.
Visual inspection can be applied to a wide range of products, from small electronic components to large industrial machinery.
Limitations of Visual Inspection
Despite its benefits, visual inspection has limitations.
It relies on the human eye, which means it is subjective and can suffer from inconsistencies.
Different inspectors might have varying opinions on what constitutes a defect.
Additionally, visual inspection only identifies surface defects; it doesn’t provide any information about internal or structural issues.
What is Dimensional Inspection?
Dimensional inspection, on the other hand, involves measuring the physical dimensions of a product to ensure they meet specified criteria.
This method is more precise and objective compared to visual inspection.
Applications of Dimensional Inspection
Dimensional inspection is frequently used in industries like engineering, machining, and manufacturing, where precise measurements are essential.
For example, in the aerospace industry, even the smallest deviation from specified measurements could compromise the safety and functionality of an aircraft.
Thus, dimensional inspection is crucial for ensuring that each component meets exact specifications.
Advantages of Dimensional Inspection
One of the primary advantages of dimensional inspection is its accuracy.
Using tools such as calipers, micrometers, and coordinate measuring machines (CMM), inspectors can obtain highly precise measurements.
Another benefit is consistency.
Unlike visual inspection, dimensional inspection provides objective data, reducing the likelihood of discrepancies and human error.
Furthermore, dimensional inspection can detect internal and structural issues that visual inspection might miss.
Limitations of Dimensional Inspection
Dimensional inspection also has its drawbacks.
The process can be time-consuming and may require specialized equipment and trained personnel, leading to higher costs.
Additionally, while dimensional inspection is excellent for checking measurements, it doesn’t account for aesthetic aspects, such as surface defects that visual inspection can catch.
Comparing Visual and Dimensional Inspection
Now that we’ve covered what visual and dimensional inspection entail, let’s compare the two methods directly.
Scope of Inspection
Visual inspection primarily focuses on surface-level defects.
It’s effective for identifying issues that affect the appearance of a product.
In contrast, dimensional inspection is concerned with the physical measurements of a product, ensuring that components fit together properly and function as intended.
Both methods serve different purposes and are often used together in a comprehensive quality control process.
Tools Required
Visual inspection generally requires minimal tools, perhaps a magnifying glass for closer examination.
The primary tool is the human eye.
Dimensional inspection, however, requires specialized equipment, such as calipers, gauges, and CMMs, to obtain precise measurements.
Human Factors
Visual inspection is highly dependent on the inspector’s experience and judgment.
This can introduce variability and subjectivity into the process.
Dimensional inspection, on the other hand, minimizes human factors by providing objective, quantifiable data.
However, it still requires skilled personnel to operate the measuring equipment and interpret the results.
Cost and Time
Visual inspection is usually faster and less expensive due to its simplicity and minimal equipment requirements.
Dimensional inspection, while more accurate, can be more time-consuming and costly due to the need for specialized tools and trained inspectors.
Accuracy and Reliability
When it comes to accuracy, dimensional inspection has the upper hand.
It provides precise measurements, ensuring that products meet exact specifications.
Visual inspection, though effective for surface defects, is less reliable for ensuring dimensional accuracy and structural integrity.
When to Use Each Method
Knowing when to use visual inspection versus dimensional inspection can make a significant difference in the quality control process.
Use Visual Inspection When:
– You need a quick, preliminary check for obvious surface defects.
– The appearance of the product is a critical quality aspect.
– Budget constraints limit the use of specialized equipment.
– Speed is more important than precise measurements.
Use Dimensional Inspection When:
– Exact measurements are crucial for product functionality and safety.
– Consistency and objectivity are required to meet stringent quality standards.
– You need to identify internal or structural defects that aren’t visible.
– The costs and time associated with specialized equipment are justified by the importance of accuracy.
Conclusion
Both visual inspection and dimensional inspection play vital roles in quality control.
Each method has its strengths and limitations, and the best approach often involves using both in tandem.
Visual inspection quickly identifies surface-level defects, while dimensional inspection provides the precision needed for ensuring exact measurements and structural integrity.
By understanding the differences and applications of these inspection methods, you can make informed decisions that enhance the quality and reliability of your products.
資料ダウンロード
QCD調達購買管理クラウド「newji」は、調達購買部門で必要なQCD管理全てを備えた、現場特化型兼クラウド型の今世紀最高の購買管理システムとなります。
ユーザー登録
調達購買業務の効率化だけでなく、システムを導入することで、コスト削減や製品・資材のステータス可視化のほか、属人化していた購買情報の共有化による内部不正防止や統制にも役立ちます。
NEWJI DX
製造業に特化したデジタルトランスフォーメーション(DX)の実現を目指す請負開発型のコンサルティングサービスです。AI、iPaaS、および先端の技術を駆使して、製造プロセスの効率化、業務効率化、チームワーク強化、コスト削減、品質向上を実現します。このサービスは、製造業の課題を深く理解し、それに対する最適なデジタルソリューションを提供することで、企業が持続的な成長とイノベーションを達成できるようサポートします。
オンライン講座
製造業、主に購買・調達部門にお勤めの方々に向けた情報を配信しております。
新任の方やベテランの方、管理職を対象とした幅広いコンテンツをご用意しております。
お問い合わせ
コストダウンが利益に直結する術だと理解していても、なかなか前に進めることができない状況。そんな時は、newjiのコストダウン自動化機能で大きく利益貢献しよう!
(Β版非公開)