- お役立ち記事
- Methods to Improve Customer Satisfaction in Manufacturing
Methods to Improve Customer Satisfaction in Manufacturing
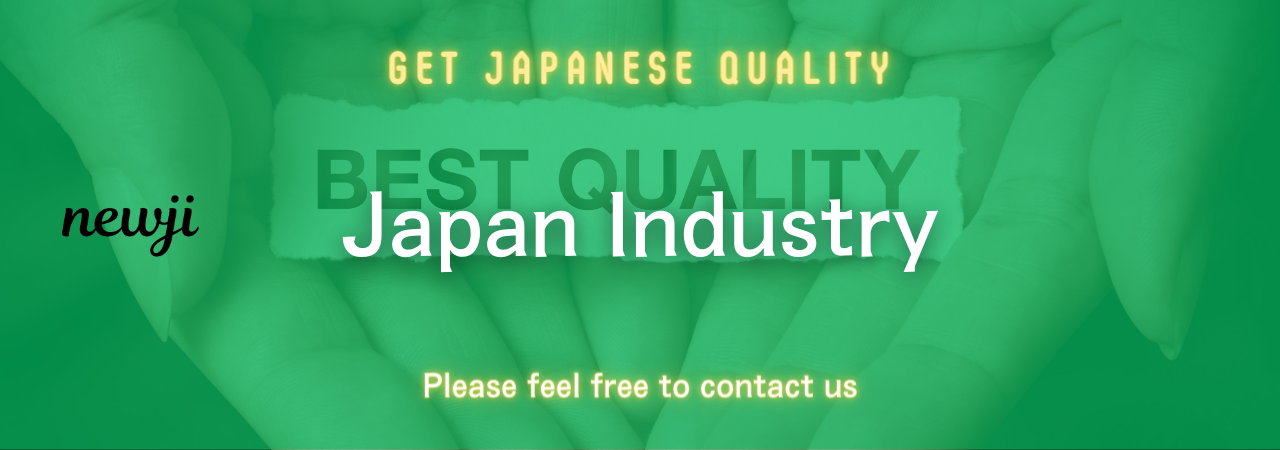
In the competitive world of manufacturing, customer satisfaction is a key factor for success. Achieving high customer satisfaction ensures repeat business and fosters positive word-of-mouth referrals. This article will explore various methods to improve customer satisfaction in the manufacturing industry.
目次
Understanding Customer Needs
Conducting Market Research
Market research is foundational to understanding customer needs. It provides insights into what customers are looking for in products and services. By conducting surveys, focus groups, and interviews, manufacturers can gather valuable feedback directly from their target audience. This data helps in tailoring products to meet customer expectations.
Analyzing Customer Feedback
Customer feedback is a goldmine of information. It offers direct insights into what customers like and dislike about your products and services. Manufacturers should implement systems to regularly gather and analyze feedback. This can be done through post-purchase surveys, online reviews, and social media interactions. By addressing the feedback promptly, businesses can improve customer satisfaction significantly.
Enhancing Product Quality
Implementing Quality Control Measures
Quality control is essential for maintaining high standards. By instituting rigorous quality control processes, manufacturers can ensure that every product meets the required specifications. Regular quality audits and inspections at various stages of production can help in identifying and rectifying issues before the products reach the customers.
Investing in Technology
Technology plays a vital role in improving product quality. Advanced manufacturing technologies such as automation, Artificial Intelligence (AI), and Internet of Things (IoT) can enhance precision and efficiency. By leveraging these technologies, manufacturers can produce high-quality products consistently, thereby boosting customer satisfaction.
Streamlining Supply Chain Management
Optimizing Inventory Management
Effective inventory management is crucial for meeting customer demands without delays. By optimizing inventory levels, manufacturers can ensure the availability of products when customers need them. Techniques such as Just-In-Time (JIT) inventory and demand forecasting can significantly enhance inventory management.
Improving Logistics
Efficient logistics are instrumental in ensuring timely delivery of products. By collaborating with reliable logistics partners and employing advanced tracking systems, manufacturers can streamline their supply chain operations. This reduces delivery times and enhances the overall customer experience.
Building Strong Customer Relationships
Providing Excellent Customer Service
Customer service is a critical component of customer satisfaction. Manufacturers should train their customer service teams to be responsive, empathetic, and knowledgeable. A prompt and effective resolution of customer issues can leave a lasting positive impression on the customers.
Engaging with Customers
Building strong relationships with customers requires active engagement. Manufacturers can engage with their customers through various channels such as social media, email newsletters, and events. Regular communication helps in building trust and loyalty, which are key factors in improving customer satisfaction.
Implementing Continuous Improvement Processes
Adopting Lean Manufacturing Principles
Lean manufacturing principles focus on eliminating waste and enhancing efficiency. By adopting these principles, manufacturers can streamline their processes and improve productivity. This not only reduces costs but also ensures that products are delivered to customers quickly and efficiently.
Encouraging Innovation
Innovation is key to staying ahead in the competitive manufacturing landscape. By fostering a culture of innovation, manufacturers can continuously improve their products and processes. This helps in meeting the evolving needs of customers and ensuring their satisfaction.
Ensuring Regulatory Compliance
Adhering to Industry Standards
Compliance with industry standards is crucial for maintaining product quality and safety. Manufacturers should stay updated with the latest regulations and ensure that their products comply with all relevant standards. This not only prevents legal issues but also enhances customer trust and satisfaction.
Implementing Environmental Practices
Sustainability is becoming increasingly important for customers. By adopting environmentally friendly practices, manufacturers can appeal to eco-conscious customers. This can include reducing waste, recycling, and using sustainable materials in the production process. Such practices can significantly boost customer satisfaction and brand reputation.
Utilizing Data Analytics
Monitoring Customer Behavior
Data analytics provides valuable insights into customer behavior and preferences. By monitoring customer interactions and purchase patterns, manufacturers can tailor their products and services to meet customer needs more effectively. This personalized approach enhances customer satisfaction.
Predictive Analytics
Predictive analytics helps in forecasting future trends and customer demands. By leveraging predictive models, manufacturers can anticipate customer needs and proactively address them. This not only improves product development but also enhances customer satisfaction by ensuring that their needs are met promptly.
Conclusion
Improving customer satisfaction in manufacturing requires a comprehensive approach. By understanding customer needs, enhancing product quality, streamlining supply chain management, building strong customer relationships, implementing continuous improvement processes, ensuring regulatory compliance, and utilizing data analytics, manufacturers can significantly boost their customer satisfaction levels. Prioritizing these methods will not only enhance customer loyalty but also drive long-term business success.
資料ダウンロード
QCD調達購買管理クラウド「newji」は、調達購買部門で必要なQCD管理全てを備えた、現場特化型兼クラウド型の今世紀最高の購買管理システムとなります。
ユーザー登録
調達購買業務の効率化だけでなく、システムを導入することで、コスト削減や製品・資材のステータス可視化のほか、属人化していた購買情報の共有化による内部不正防止や統制にも役立ちます。
NEWJI DX
製造業に特化したデジタルトランスフォーメーション(DX)の実現を目指す請負開発型のコンサルティングサービスです。AI、iPaaS、および先端の技術を駆使して、製造プロセスの効率化、業務効率化、チームワーク強化、コスト削減、品質向上を実現します。このサービスは、製造業の課題を深く理解し、それに対する最適なデジタルソリューションを提供することで、企業が持続的な成長とイノベーションを達成できるようサポートします。
オンライン講座
製造業、主に購買・調達部門にお勤めの方々に向けた情報を配信しております。
新任の方やベテランの方、管理職を対象とした幅広いコンテンツをご用意しております。
お問い合わせ
コストダウンが利益に直結する術だと理解していても、なかなか前に進めることができない状況。そんな時は、newjiのコストダウン自動化機能で大きく利益貢献しよう!
(Β版非公開)