- お役立ち記事
- Manufacturing Process of Electric Interdental Brushes and Vibration Adjustment Improvements
Manufacturing Process of Electric Interdental Brushes and Vibration Adjustment Improvements
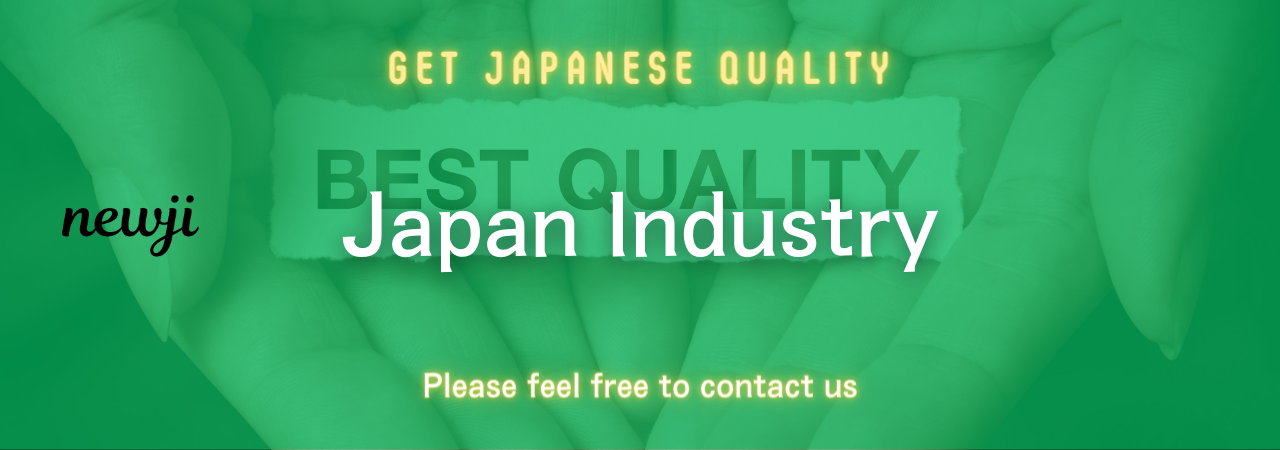
目次
Introduction to Electric Interdental Brushes
Electric interdental brushes are small devices designed to clean the spaces between your teeth more effectively than regular toothbrushes.
These innovative tools have become popular due to their efficiency in maintaining oral hygiene.
In this article, we’ll explore the manufacturing process of electric interdental brushes and learn about improvements in vibration adjustments.
The Manufacturing Process
The creation of electric interdental brushes involves several steps.
Here, we’ll break down the process from the initial design to the final product.
Design and Planning
Before production begins, engineers and designers collaborate to create a detailed plan.
They focus on the brush’s size, shape, and electric components.
The goal is to produce a device that is both functional and comfortable for the user.
Prototyping
Once the design is completed, a prototype is created.
This early model helps engineers identify any potential issues.
Prototyping is a crucial step because it allows for adjustments before mass production begins.
Component Manufacturing
Electric interdental brushes consist of several key components: the handle, bristles, motor, and battery.
Each part is manufactured separately.
The handle is usually made from durable plastic, molded into the desired shape using injection molding.
Bristles are made from nylon and attached to a small metal or plastic head.
The motor, which generates the vibrations, is produced in specialized facilities.
Lastly, the battery, typically a rechargeable lithium-ion cell, is assembled.
Assembly Line
In the assembly line, these components come together.
Workers or automated machines attach the bristle head to the handle.
Then, they insert the motor and battery into the handle.
Wiring is connected to ensure the electrical components function correctly.
Quality Control
Quality control is a vital part of the manufacturing process.
Each brush undergoes rigorous testing to ensure it meets safety and performance standards.
Any defective units are identified and removed from the production line.
Packaging and Distribution
Once the brushes pass quality control, they are packaged.
Packaging involves placing the brushes in protective cases and adding user manuals.
Finally, the packaged brushes are distributed to retailers and online stores.
Vibration Adjustment Improvements
One of the key features of electric interdental brushes is their vibrating function.
Recent advancements have led to significant improvements in vibration adjustment.
Why Vibration Matters
Vibration helps to dislodge food particles and plaque from between the teeth.
The right amount of vibration can enhance cleaning efficiency without causing discomfort.
Technology Enhancements
Modern electric interdental brushes come equipped with advanced vibration technology.
Microcontrollers are integrated into the brushes to precisely control vibration patterns and intensity.
This allows users to choose from different settings based on their comfort level and cleaning needs.
Another innovation is the use of smart sensors.
These sensors detect the pressure applied against the teeth and adjust the vibration accordingly.
This prevents potential damage to the gums and ensures a more gentle yet effective cleaning process.
Battery Life
Enhancements in battery technology have also contributed to better vibration control.
Newer models feature high-capacity batteries that provide consistent power output.
This consistency helps maintain a steady vibration throughout the cleaning session.
Customizable Settings
Manufacturers have introduced customizable settings to cater to individual preferences.
Users can now select different vibration modes, such as gentle, standard, and intense.
These settings can be easily adjusted, often with a simple press of a button.
Silent Operation
Noise reduction is another area where improvements have been made.
Quieter motors and better insulation mean that modern electric interdental brushes operate with minimal noise.
This makes the brushing experience more pleasant, especially for those who are sensitive to loud sounds.
User Feedback
Feedback from users has played a significant role in driving these improvements.
Manufacturers regularly collect and analyze user reviews.
This data helps them understand what works well and identify areas for enhancement.
Conclusion
The manufacturing process of electric interdental brushes is a complex yet fascinating journey.
From design and prototyping to assembly and quality control, each step ensures the final product is effective and reliable.
Advancements in vibration adjustment technology have made these brushes more efficient and user-friendly.
As technology continues to evolve, we can expect even more innovations in the future.
Understanding the manufacturing process and the improvements in vibration adjustment helps us appreciate the engineering marvel behind electric interdental brushes.
The next time you use one, you’ll know there’s much more to it than meets the eye.
資料ダウンロード
QCD調達購買管理クラウド「newji」は、調達購買部門で必要なQCD管理全てを備えた、現場特化型兼クラウド型の今世紀最高の購買管理システムとなります。
ユーザー登録
調達購買業務の効率化だけでなく、システムを導入することで、コスト削減や製品・資材のステータス可視化のほか、属人化していた購買情報の共有化による内部不正防止や統制にも役立ちます。
NEWJI DX
製造業に特化したデジタルトランスフォーメーション(DX)の実現を目指す請負開発型のコンサルティングサービスです。AI、iPaaS、および先端の技術を駆使して、製造プロセスの効率化、業務効率化、チームワーク強化、コスト削減、品質向上を実現します。このサービスは、製造業の課題を深く理解し、それに対する最適なデジタルソリューションを提供することで、企業が持続的な成長とイノベーションを達成できるようサポートします。
オンライン講座
製造業、主に購買・調達部門にお勤めの方々に向けた情報を配信しております。
新任の方やベテランの方、管理職を対象とした幅広いコンテンツをご用意しております。
お問い合わせ
コストダウンが利益に直結する術だと理解していても、なかなか前に進めることができない状況。そんな時は、newjiのコストダウン自動化機能で大きく利益貢献しよう!
(Β版非公開)