- お役立ち記事
- Key Quality Control Points for Success in the Thermal Spraying Industry
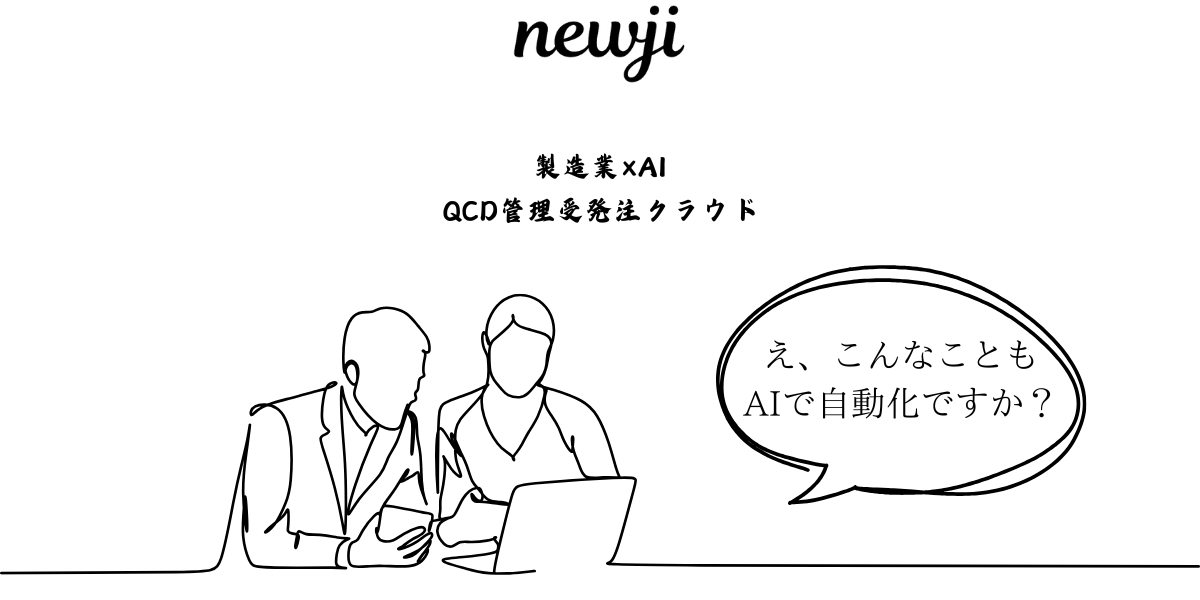
Key Quality Control Points for Success in the Thermal Spraying Industry
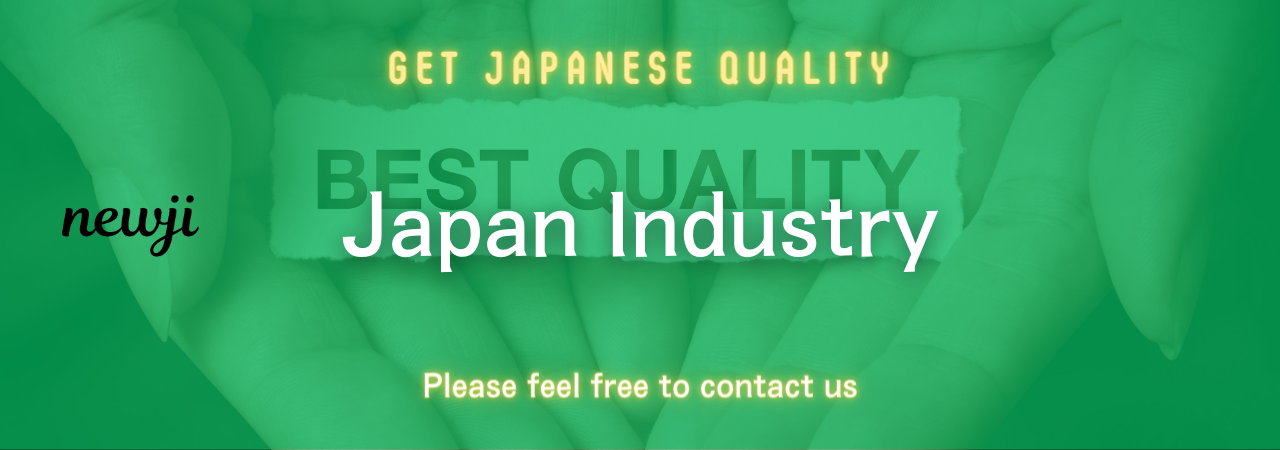
Thermal spraying is a crucial process in various industries, employing a variety of materials to coat surfaces and enhance or restore their properties.
Ensuring the success of thermal spraying applications requires strict attention to quality control points.
Identifying these key points can help in achieving optimal results and long-lasting performance.
目次
Understanding Thermal Spraying
Thermal spraying is an industrial process that involves the deposition of materials onto surfaces.
It is typically used for coating components to improve wear resistance, corrosion resistance, and temperature resistance.
Industries such as aerospace, automotive, and manufacturing heavily rely on this technique.
The Basic Process
The thermal spraying process includes the heating of a material, which can be in the form of a powder or wire, until it becomes molten or semi-molten.
This material is then sprayed onto the surface using a high-velocity gas stream.
The coating material adheres to the surface, forming a strong bond upon cooling.
Key Stages in Thermal Spraying
Understanding the basic stages in thermal spraying helps in identifying critical quality control points.
Here are the primary stages and their significance:
1. Surface Preparation
Effective thermal spraying starts with thorough surface preparation.
The surface to be coated must be clean, free of contaminants, and adequately roughened to ensure effective adhesion.
Surface preparation typically involves:
– **Cleaning:** Removing oils, greases, and other contaminants.
– **Roughening:** Creating an appropriate surface texture using blasting media.
– **Inspection:** Ensuring the surface meets all pre-specified conditions.
2. Material Selection
Choosing the right material for thermal spraying is essential for the coating’s effectiveness and longevity.
Factors to consider include:
– **Compatibility:** The material must be compatible with the substrate and end-use environment.
– **Properties:** Desired properties such as hardness, thermal resistance, and corrosion resistance must align with the application.
– **Availability:** Material availability and cost can influence the selection process.
3. Parameter Settings
The success of the thermal spraying process heavily depends on precise parameter control.
Key parameters include:
– **Spray Distance:** The distance between the spray gun and the target surface affects the coating’s quality.
– **Feed Rate:** The rate at which the material is fed into the spray gun.
– **Temperature:** Accurately controlling the temperature to achieve ideal material melting or semi-melting.
– **Velocity:** Proper gas velocity ensures efficient material transfer and adhesion.
Key Quality Control Points
Ensuring successful thermal spraying involves rigorous quality control measures at each stage.
Adhering to these key points helps in achieving optimal performance and meeting industry standards.
1. Consistent Surface Preparation
Quality control begins with ensuring consistent and effective surface preparation.
Variations in cleaning and roughening can lead to adhesion issues and coating failures.
Regular checks and standard operating procedures must be established to maintain uniformity.
2. Material Certification and Testing
Using certified materials that meet industry specifications is vital.
In-house testing of materials for properties like particle size distribution, purity, and composition ensures that only high-quality materials are utilized.
Random sampling during the process helps in maintaining consistency.
3. Accurate Parameter Monitoring
Continuous monitoring and adjustment of process parameters are necessary to maintain coating quality.
Using automated systems to monitor spray distance, feed rate, temperature, and velocity ensures that deviations are promptly corrected.
Regular calibration of equipment is also crucial.
4. Operator Training and Certification
Skilled operators play a significant role in the effectiveness of thermal spraying.
Regular training and certification programs ensure that operators are proficient in handling equipment and adhering to quality standards.
Refresher courses and skills assessments help in maintaining operator competence.
5. Coating Inspection and Testing
Post-spraying inspection and testing are essential for verifying coating quality and performance.
Common inspection methods include:
– **Visual Inspection:** Identifying visible defects like cracks, uneven coating, or poor adhesion.
– **Thickness Measurement:** Ensuring the coating meets specified thickness requirements using instruments like micrometers or ultrasonic gauges.
– **Adhesion Testing:** Performing tests to measure the bond strength between the substrate and the coating.
– **Hardness Testing:** Assessing the coating’s hardness to ensure it meets the desired properties.
Implementing Continuous Improvement
Quality control in thermal spraying is not a one-time task.
It requires continuous improvement and adaptation to new technologies and methods.
Implementing a continuous improvement strategy involves:
1. Regular Audits and Reviews
Conducting regular audits and reviews of the thermal spraying process helps in identifying areas for improvement.
Feedback from these audits can be used to update standard practices and quality control measures.
2. Technological Advancements
Keeping abreast of technological advancements in thermal spraying equipment and materials can enhance process efficiency and coating quality.
Investing in advanced spray systems and monitoring tools can lead to better control and performance.
3. Customer Feedback
Customer feedback provides valuable insights into the performance of thermal spray coatings in real-world applications.
Using this feedback to refine processes and material choices ensures that coatings meet or exceed customer expectations.
4. Documentation and Record-Keeping
Maintaining detailed records of all quality control activities, material certifications, and process parameters helps in traceability and accountability.
These records can be invaluable during troubleshooting and process optimization.
Conclusion
Ensuring success in the thermal spraying industry hinges on meticulous attention to quality control points across all stages of the process.
Consistent surface preparation, precise parameter control, thorough material testing, and skilled operators are fundamental to achieving durable and high-performance coatings.
By adopting a continuous improvement mindset and leveraging technological advances, industry professionals can maintain high standards and meet the evolving demands of their clients.
With these practices in place, the thermal spraying industry can continue to deliver reliable and effective solutions across various applications.
資料ダウンロード
QCD調達購買管理クラウド「newji」は、調達購買部門で必要なQCD管理全てを備えた、現場特化型兼クラウド型の今世紀最高の購買管理システムとなります。
ユーザー登録
調達購買業務の効率化だけでなく、システムを導入することで、コスト削減や製品・資材のステータス可視化のほか、属人化していた購買情報の共有化による内部不正防止や統制にも役立ちます。
NEWJI DX
製造業に特化したデジタルトランスフォーメーション(DX)の実現を目指す請負開発型のコンサルティングサービスです。AI、iPaaS、および先端の技術を駆使して、製造プロセスの効率化、業務効率化、チームワーク強化、コスト削減、品質向上を実現します。このサービスは、製造業の課題を深く理解し、それに対する最適なデジタルソリューションを提供することで、企業が持続的な成長とイノベーションを達成できるようサポートします。
オンライン講座
製造業、主に購買・調達部門にお勤めの方々に向けた情報を配信しております。
新任の方やベテランの方、管理職を対象とした幅広いコンテンツをご用意しております。
お問い合わせ
コストダウンが利益に直結する術だと理解していても、なかなか前に進めることができない状況。そんな時は、newjiのコストダウン自動化機能で大きく利益貢献しよう!
(Β版非公開)