- お役立ち記事
- The difference between Logistics and Supply Chain
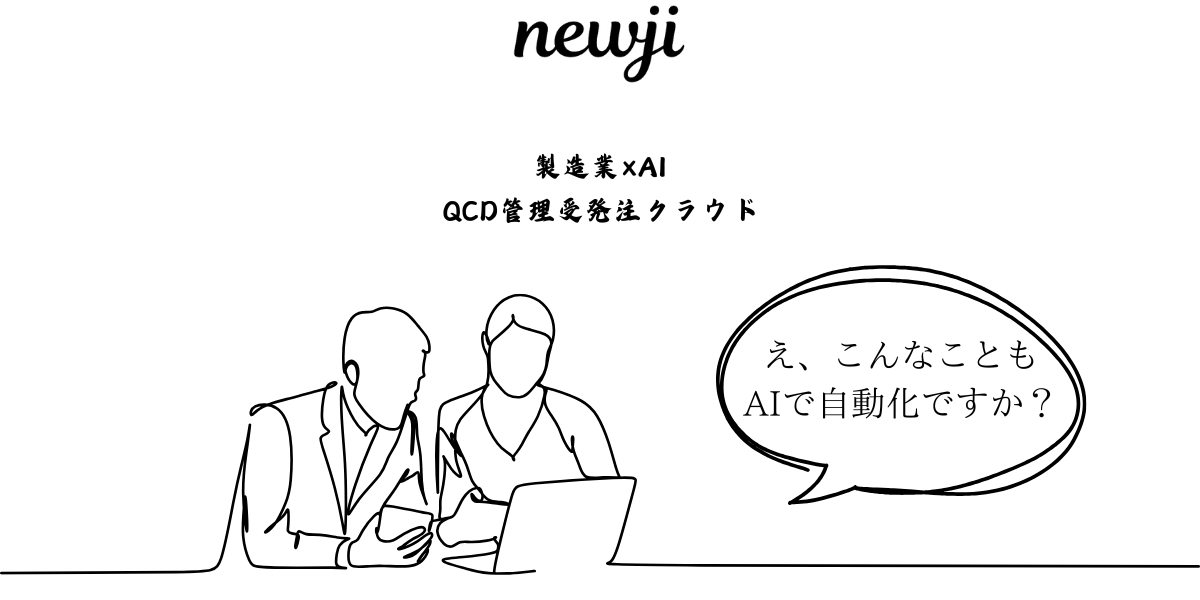
The difference between Logistics and Supply Chain
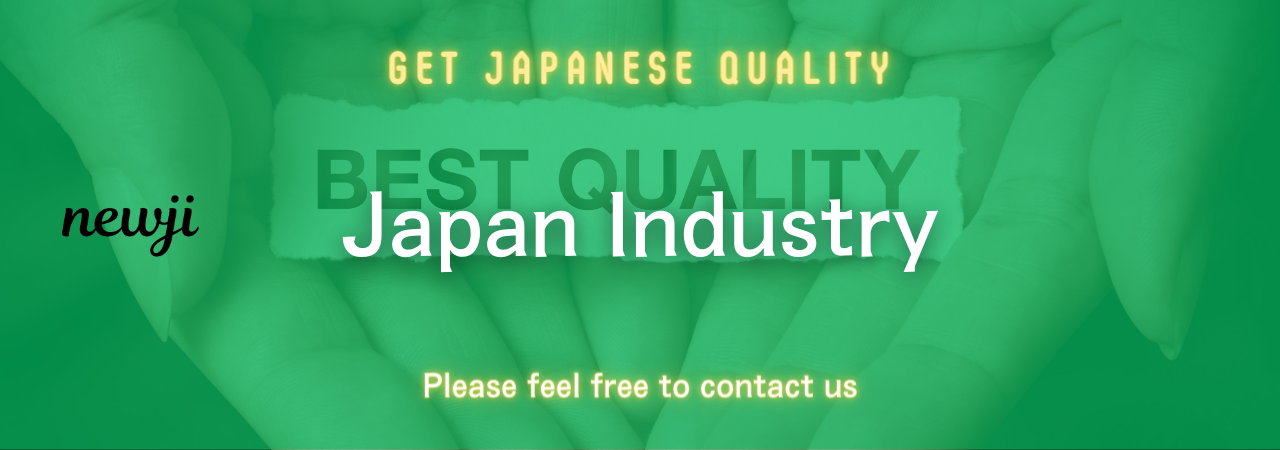
Understanding how products get from the factory into your hands can sometimes feel like a big mystery. Terms like “logistics” and “supply chain” are often thrown around, but what do they mean, and how do they affect what you buy or use every day? Let’s break it down in a way that’s easy to understand.
目次
What is Logistics?
Logistics is like the planning part of a big trip but for products. It involves everything needed to move goods from one place to another. Think of it as the detailed steps required to make sure products get from where they are made to where they are sold.
Transporting Goods
One of the main parts of logistics is transportation. This includes all the trucks, ships, trains, and planes used to move products around. Imagine the truck that brings fresh milk to your local grocery store. That’s a part of logistics.
Storage and Warehousing
After a product leaves the factory, it might need to be stored before it reaches the store. Warehouses act as big storage rooms that keep these products safe and organized. Cold storage is also used for things that need to stay cool, like ice cream and vegetables.
Managing Inventory
Another important part of logistics is managing inventory. This means keeping track of all the products in storage. Imagine a bookstore knowing exactly how many copies of a popular book they have left. Good inventory management helps prevent problems like running out of stock or having too many products that aren’t selling.
Customer Service
Customer service is also a part of logistics. If there’s a problem with a shipment, like if a product arrives late or damaged, good customer service can help solve these issues quickly. This makes sure that customers get what they paid for and are happy with their purchase.
What is the Supply Chain?
The term “supply chain” is broader than logistics. It includes all the steps involved in producing and delivering a product, from start to finish. Think of it like a chain with many links, each link representing a different stage in the production and distribution process.
Raw Materials
The supply chain starts with raw materials. These are the basic ingredients needed to make a product. For example, to make a chocolate bar, you need cocoa beans, sugar, and milk. These raw materials have to be collected from different places around the world.
Manufacturing
After raw materials are gathered, the next step in the supply chain is manufacturing. This is where raw materials are turned into finished products. In our chocolate bar example, this would be the factory where the cocoa beans, sugar, and milk are combined and transformed into delicious chocolate bars.
Packaging
Once products are made, they need to be packaged. Packaging protects the product and makes it ready for transport and sale. Proper packaging makes sure that products remain fresh and undamaged, and it also includes important information like expiration dates and ingredients.
Distribution
The distribution part of the supply chain involves moving the finished products to different locations where they will be sold. This can include transporting goods to warehouses, stores, or directly to the end customer. Efficient distribution methods help ensure products reach their destination on time.
Retail
Finally, products are sold to customers in retail stores or online shops. This is where most people come into contact with the supply chain. A well-functioning supply chain makes sure that the right products are available for you to buy whenever you need them.
The Relationship Between Logistics and Supply Chain
You may be wondering how logistics and supply chain relate to each other. Simply put, logistics is a crucial part of the supply chain. While the supply chain covers the entire process from raw materials to finished products, logistics focuses on the transportation, storage, and handling of these products.
Coordination is Key
Both logistics and supply chain management require careful coordination. This means making sure that every part of the process works smoothly together. If one part of the supply chain has problems, like a delay in transportation, it can affect the entire process.
Technology and Innovation
Technology plays a big role in both logistics and supply chain management. Things like GPS tracking and warehouse automation make the movement and storage of products more efficient. These technologies help companies track shipments in real-time and manage inventory more accurately.
Customer Expectations
Today’s customers expect fast delivery and high-quality products. This means that both logistics and supply chain managers have to work extra hard to meet these expectations. Companies that have efficient logistics and supply chains are better able to provide quick delivery times and better customer service.
Why It Matters to You
Understanding the difference between logistics and supply chain can help you appreciate the complex processes involved in getting products to you. The next time you buy something, you’ll know that a lot of planning and coordination went into making sure it was available for you to buy.
Better Choices
With this knowledge, you can make better choices as a consumer. For example, you can look for companies that prioritize sustainable sourcing, efficient transportation, and good customer service. This can help you support businesses that are working to improve their logistics and supply chains in positive ways.
Reduced Costs and Improved Quality
Efficient logistics and supply chains can also lead to reduced costs and improved product quality. When companies streamline their processes, they can save money, which could be passed on to you as lower prices. Similarly, better logistics can lead to fewer damaged products and faster deliveries.
Understanding the difference between logistics and supply chain can make you a more informed consumer. The next time you see a product on a store shelf or delivered to your home, you’ll know about the complex journey it went through to get there. This knowledge can help you make wiser purchasing decisions and appreciate the intricate systems that make modern shopping possible.
資料ダウンロード
QCD調達購買管理クラウド「newji」は、調達購買部門で必要なQCD管理全てを備えた、現場特化型兼クラウド型の今世紀最高の購買管理システムとなります。
ユーザー登録
調達購買業務の効率化だけでなく、システムを導入することで、コスト削減や製品・資材のステータス可視化のほか、属人化していた購買情報の共有化による内部不正防止や統制にも役立ちます。
NEWJI DX
製造業に特化したデジタルトランスフォーメーション(DX)の実現を目指す請負開発型のコンサルティングサービスです。AI、iPaaS、および先端の技術を駆使して、製造プロセスの効率化、業務効率化、チームワーク強化、コスト削減、品質向上を実現します。このサービスは、製造業の課題を深く理解し、それに対する最適なデジタルソリューションを提供することで、企業が持続的な成長とイノベーションを達成できるようサポートします。
オンライン講座
製造業、主に購買・調達部門にお勤めの方々に向けた情報を配信しております。
新任の方やベテランの方、管理職を対象とした幅広いコンテンツをご用意しております。
お問い合わせ
コストダウンが利益に直結する術だと理解していても、なかなか前に進めることができない状況。そんな時は、newjiのコストダウン自動化機能で大きく利益貢献しよう!
(Β版非公開)