- お役立ち記事
- The difference between Die Forging and Open Forging
The difference between Die Forging and Open Forging
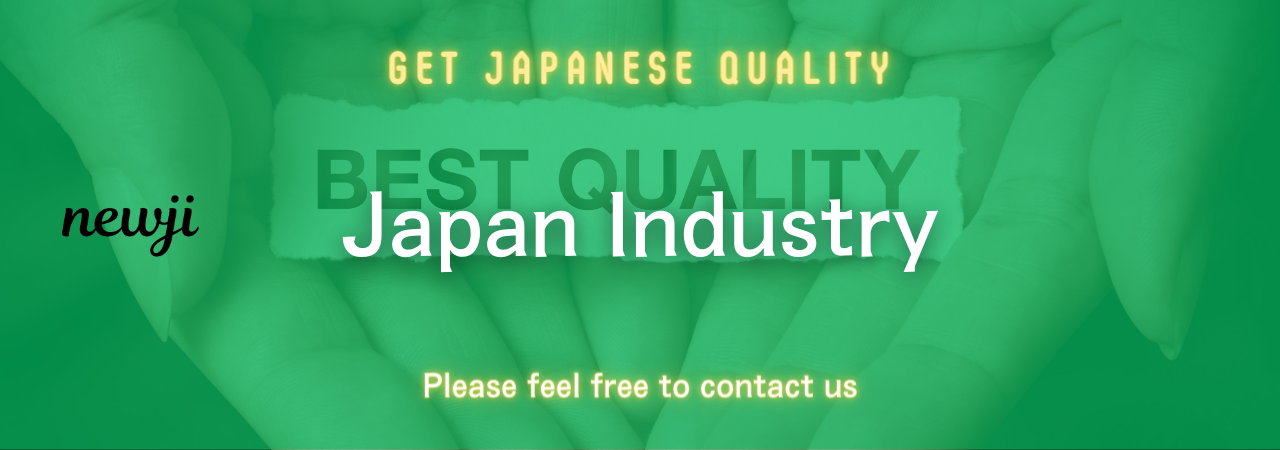
Die forging and open forging are two fundamental techniques used in the metalworking industry to shape metals into desired forms.
While both methods aim to transform raw metal into useful products, they do so in different ways and often serve distinct purposes.
Understanding the differences between die forging and open forging can help in selecting the appropriate process for a specific application.
目次
What is Die Forging?
Die forging, also known as closed die forging, involves using high pressure to shape a piece of metal inside a closed mold or die.
This process results in precise shapes and consistent dimensions.
A pair of dies is typically used, with one fixed and the other movable.
When the metal is placed between the dies and pressure is applied, the metal takes the shape of the cavity formed by the dies.
Advantages of Die Forging
One of the primary benefits of die forging is the ability to produce complex shapes with a high degree of accuracy.
The finished products often require little to no additional machining, which can save both time and cost.
Another advantage is the uniformity of the parts produced.
Because the same die can be used repeatedly, each piece tends to be identical in terms of dimensions and physical properties.
Disadvantages of Die Forging
While die forging offers high precision and consistency, it also comes with some drawbacks.
The cost of manufacturing the dies can be substantial, making this process more suitable for high-volume production runs.
Additionally, die forging is generally limited to smaller parts because creating large dies can be impractical and expensive.
Applications of Die Forging
Die forging is commonly used in industries where precision and strength are crucial.
Automotive components, aerospace parts, and industrial machinery often rely on die-forged parts for their superior mechanical properties.
Common examples include gears, shafts, and connecting rods.
What is Open Forging?
Open forging, also known as smith forging or hand forging, involves shaping metal using hammering and pressing techniques without confining the work piece within a die.
This method is often used for larger parts and allows for greater flexibility in shaping the material.
The metal is heated until it becomes pliable and is then manipulated by a blacksmith or machine.
Advantages of Open Forging
One of the main advantages of open forging is the ability to produce large and uniquely shaped parts that would be difficult or impossible to create using die forging.
Because the process doesn’t rely on expensive dies, it can also be more cost-effective for smaller production runs or one-off custom pieces.
Open forging also allows for greater control over the grain structure of the metal, leading to improved mechanical properties.
Disadvantages of Open Forging
While open forging is versatile, it also has some limitations.
The process is less precise than die forging, so additional machining is often required to achieve the desired dimensions and surface finish.
Open forging can also be more labor-intensive, requiring skilled operators to perform the process accurately.
Applications of Open Forging
Open forging is widely used in industries that require large, strong components.
Shipbuilding, construction, and heavy machinery often utilize open-forged parts.
Examples include large shafts, beams, and custom-engineered components that must withstand substantial stress and load conditions.
Comparing Die Forging and Open Forging
While both die forging and open forging serve the purpose of shaping metal, they are suited to different applications and offer distinct advantages and disadvantages.
Precision and Complexity
Die forging excels in producing precise, complex shapes with high repeatability.
Open forging, on the other hand, is more versatile and can create larger, more uniquely shaped parts.
Cost and Production Volume
Die forging generally requires a higher initial investment due to the cost of manufacturing dies.
It becomes cost-effective for large production runs.
Open forging is more cost-effective for smaller production runs or unique, customized pieces, as it doesn’t require expensive dies.
Material Properties
Both methods can produce parts with excellent mechanical properties, but open forging allows for more control over grain structure.
This can be especially beneficial for components that need to withstand high stress and impact.
Conclusion
Choosing between die forging and open forging depends on various factors, including the size and complexity of the part, the required precision, and the production volume.
Die forging offers high precision and consistency, making it ideal for smaller, high-volume parts.
Open forging, with its flexibility and ability to produce large parts, is better suited for custom and low-volume applications.
Understanding these differences can help you make informed decisions when selecting the most suitable forging process for your specific needs.
Whether you prioritize precision, cost, or material properties, both die forging and open forging have their unique strengths and applications.
資料ダウンロード
QCD調達購買管理クラウド「newji」は、調達購買部門で必要なQCD管理全てを備えた、現場特化型兼クラウド型の今世紀最高の購買管理システムとなります。
ユーザー登録
調達購買業務の効率化だけでなく、システムを導入することで、コスト削減や製品・資材のステータス可視化のほか、属人化していた購買情報の共有化による内部不正防止や統制にも役立ちます。
NEWJI DX
製造業に特化したデジタルトランスフォーメーション(DX)の実現を目指す請負開発型のコンサルティングサービスです。AI、iPaaS、および先端の技術を駆使して、製造プロセスの効率化、業務効率化、チームワーク強化、コスト削減、品質向上を実現します。このサービスは、製造業の課題を深く理解し、それに対する最適なデジタルソリューションを提供することで、企業が持続的な成長とイノベーションを達成できるようサポートします。
オンライン講座
製造業、主に購買・調達部門にお勤めの方々に向けた情報を配信しております。
新任の方やベテランの方、管理職を対象とした幅広いコンテンツをご用意しております。
お問い合わせ
コストダウンが利益に直結する術だと理解していても、なかなか前に進めることができない状況。そんな時は、newjiのコストダウン自動化機能で大きく利益貢献しよう!
(Β版非公開)