- お役立ち記事
- Mastering the Art of Specimen Cutting: The Essentials of Japanese Manufacturing Techniques
Mastering the Art of Specimen Cutting: The Essentials of Japanese Manufacturing Techniques
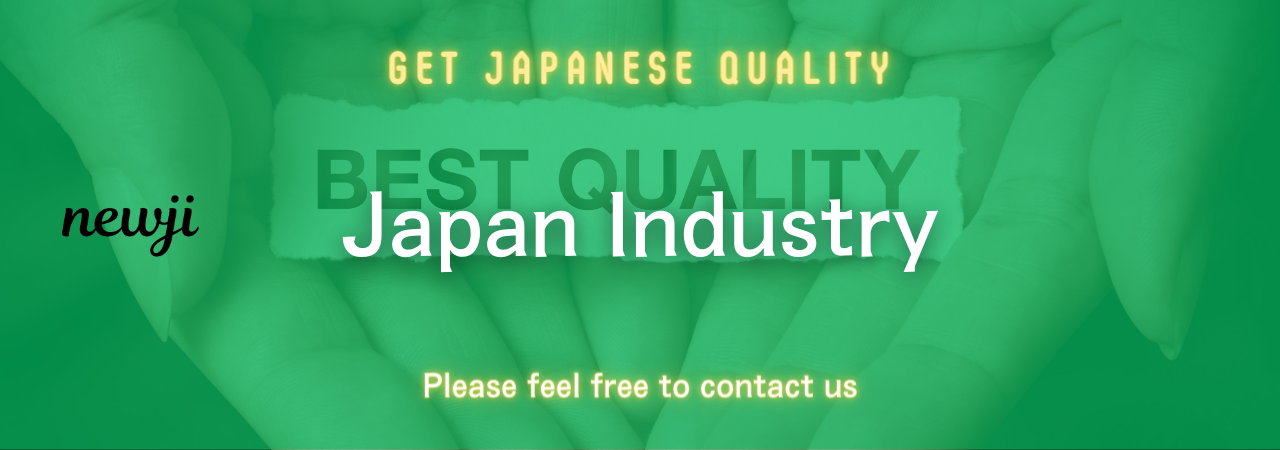
目次
Introduction to Specimen Cutting
In the realm of manufacturing, precision is key. One aspect that demands meticulous attention is specimen cutting, an essential process for testing and quality assurance. Specimen cutting involves taking samples from larger materials or products to evaluate their characteristics, properties, or defects. This technique is a cornerstone in industries such as automotive, aerospace, electronics, and more. In this context, Japanese manufacturing techniques have set a global benchmark.
This article delves into the intricacies of specimen cutting, highlighting the paramount Japanese methods that have become synonymous with quality and efficiency.
The Japanese Manufacturing Philosophy
Before diving into the technical aspects, it’s vital to understand the foundational philosophy of Japanese manufacturing. Japan’s manufacturing culture emphasizes perfection, continuous improvement (Kaizen), and a strong commitment to quality. This ethos permeates every facet of the production process, including specimen cutting.
Japanese manufacturers prioritize precision and accuracy, investing heavily in state-of-the-art technology and skilled labor. This commitment has enabled them to produce consistently high-quality specimens, ensuring reliable and valid test results.
Essential Techniques in Japanese Specimen Cutting
1. Precision Machining
One of the key techniques in Japanese specimen cutting is precision machining. Utilizing advanced machinery like CNC (Computer Numerical Control) machines, manufacturers achieve extremely tight tolerances and smooth finishes. These machines are programmed to cut specimens with unparalleled accuracy, minimizing human error and material wastage.
2. Laser Cutting
Laser cutting is another widely employed technique in Japan. This method involves using high-powered lasers to cut materials with exceptional precision. Laser cutting is particularly advantageous for delicate or intricate specimens, where traditional methods might fail to deliver the required accuracy. The use of lasers ensures clean cuts, reducing the need for further processing.
3. Waterjet Cutting
Waterjet cutting utilizes high-pressure streams of water, sometimes mixed with abrasive materials, to achieve precise cuts on a variety of materials. This technique is highly versatile and can cut through metals, ceramics, glass, and composites. The cold cutting process prevents heat-affected zones, preserving the material’s structural integrity.
4. Wire EDM (Electrical Discharge Machining)
Wire EDM is a technique where a thin wire conducts electrical discharges to cut through the material. It is ideal for cutting hard materials and complex shapes. This method offers high precision and smooth finishes, making it a preferred choice for critical specimen preparation.
Advantages of Japanese Specimen Cutting Techniques
1. Unparalleled Precision
Japanese techniques are revered for their remarkable precision. Advanced machinery and meticulous methodologies ensure that specimens are cut to exact specifications, which is crucial for reliable testing.
2. Enhanced Efficiency
Investing in high-tech machinery and skilled labor allows Japanese manufacturers to achieve faster turnaround times. This efficiency translates into cost savings and the ability to meet tight production schedules.
3. Superior Quality Control
Japanese manufacturing is synonymous with stringent quality control. Every step of the specimen cutting process is monitored to ensure adherence to the highest standards. This rigor guarantees that the specimens accurately represent the larger material or product.
4. Material Versatility
Whether dealing with metals, plastics, ceramics, or composites, Japanese techniques can handle a wide range of materials. This versatility is crucial for industries that work with diverse materials and require precise specimen preparation.
Challenges and Disadvantages
While Japanese specimen cutting techniques offer numerous advantages, they are not without challenges.
1. High Initial Investment
The advanced machinery and technology required for these techniques come with a significant initial investment. Small and mid-sized companies might find it challenging to afford such equipment.
2. Skilled Labor Requirement
Operating advanced machinery and ensuring precision cutting necessitates a highly skilled workforce. Training and retaining such skilled labor can be a challenge, especially in markets with labor shortages.
3. Maintenance Costs
High-tech machinery requires regular maintenance to function optimally. This upkeep can be costly and time-consuming, adding to the overall operational expenses.
Supplier Negotiation Techniques
When dealing with Japanese suppliers, it is crucial to adopt a strategic approach to negotiations. Understanding the Japanese business culture and negotiation tactics can significantly impact the outcome.
1. Building Relationships
In Japan, business relationships are built on trust and mutual respect. Investing time in building strong relationships with suppliers can lead to more favorable terms and long-term collaboration.
2. Emphasizing Quality
Japanese suppliers prioritize quality above all else. Highlighting your commitment to maintaining high standards can align your interests and foster cooperative negotiations.
3. Patience and Politeness
Patience is a virtue in Japanese business culture. Rushing negotiations or displaying impatience can be counterproductive. Politeness and respect are highly valued and can positively influence negotiations.
Market Conditions
The global market for specimen cutting is evolving, with technological advancements and increased demand for precision testing driving growth.
1. Technological Advancements
Continuous innovation in cutting technologies, such as AI-powered CNC machines and advanced laser systems, is enhancing precision and efficiency. Staying abreast of these advancements is crucial for maintaining competitiveness.
2. Growing Demand for Quality Testing
Industries worldwide are increasingly prioritizing quality assurance, leading to higher demand for precision specimen cutting. This trend presents opportunities for manufacturers to expand their capabilities and market reach.
Best Practices in Specimen Cutting
Adopting best practices can significantly enhance the efficiency and quality of specimen cutting processes.
1. Regular Calibration and Maintenance
Ensuring that all machinery is regularly calibrated and maintained is essential for consistent precision cutting. Scheduled maintenance can prevent breakdowns and extend the lifespan of equipment.
2. Skilled Workforce Training
Investing in continuous training for the workforce ensures that operators stay updated with the latest techniques and technologies. Skilled operators are essential for achieving the high precision demanded in specimen cutting.
3. Implementing Quality Control Protocols
Establishing stringent quality control protocols at every stage of the specimen cutting process is crucial. Regular inspections and testing can prevent defects and ensure that specimens meet the required standards.
4. Adopting Sustainable Practices
Sustainability is becoming increasingly important in manufacturing. Implementing eco-friendly practices, such as minimizing material wastage and using energy-efficient machinery, can enhance the sustainability of specimen cutting processes.
Conclusion
Mastering the art of specimen cutting involves understanding and implementing the essential techniques and best practices that define Japanese manufacturing. Embracing precision machining, laser cutting, waterjet cutting, and wire EDM can elevate the quality and efficiency of specimen preparation. While challenges such as high initial investment and the need for skilled labor exist, the benefits far outweigh these hurdles.
By building strong relationships with Japanese suppliers, understanding market conditions, and adopting best practices, manufacturers can achieve unparalleled precision and quality in specimen cutting. This commitment to excellence not only enhances product reliability but also solidifies a reputation for quality in the competitive global market.
資料ダウンロード
QCD調達購買管理クラウド「newji」は、調達購買部門で必要なQCD管理全てを備えた、現場特化型兼クラウド型の今世紀最高の購買管理システムとなります。
ユーザー登録
調達購買業務の効率化だけでなく、システムを導入することで、コスト削減や製品・資材のステータス可視化のほか、属人化していた購買情報の共有化による内部不正防止や統制にも役立ちます。
NEWJI DX
製造業に特化したデジタルトランスフォーメーション(DX)の実現を目指す請負開発型のコンサルティングサービスです。AI、iPaaS、および先端の技術を駆使して、製造プロセスの効率化、業務効率化、チームワーク強化、コスト削減、品質向上を実現します。このサービスは、製造業の課題を深く理解し、それに対する最適なデジタルソリューションを提供することで、企業が持続的な成長とイノベーションを達成できるようサポートします。
オンライン講座
製造業、主に購買・調達部門にお勤めの方々に向けた情報を配信しております。
新任の方やベテランの方、管理職を対象とした幅広いコンテンツをご用意しております。
お問い合わせ
コストダウンが利益に直結する術だと理解していても、なかなか前に進めることができない状況。そんな時は、newjiのコストダウン自動化機能で大きく利益貢献しよう!
(Β版非公開)