- お役立ち記事
- Manufacturing Process of Vacuum Dustboxes and Integration of Filter Technology
Manufacturing Process of Vacuum Dustboxes and Integration of Filter Technology
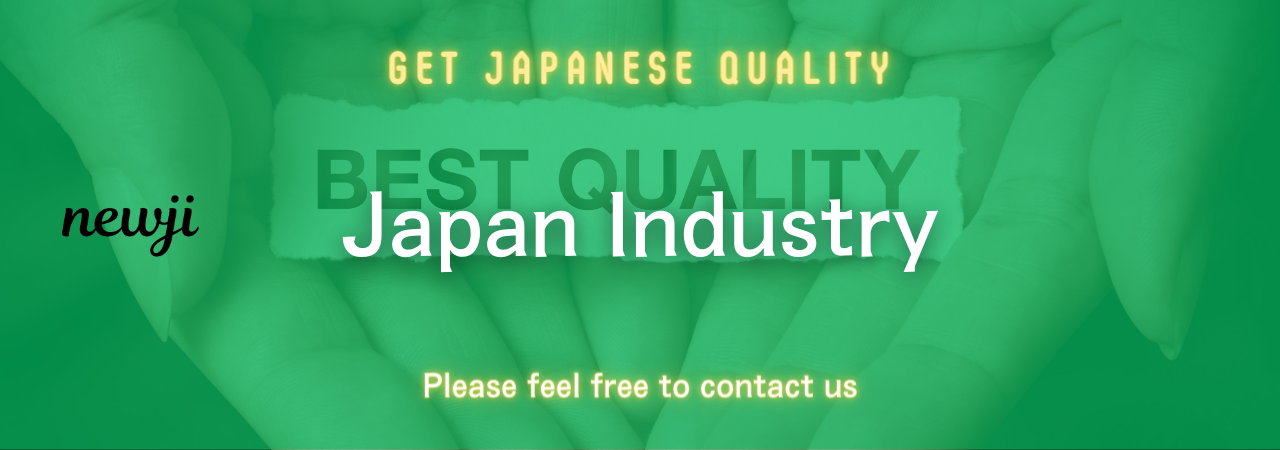
Vacuum dustboxes are an essential component in many modern cleaning devices.
These dustboxes not only store the collected dust and debris but also work in tandem with advanced filter technology.
Understanding the manufacturing process and the integration of filter technology can help us appreciate the efficiency and sophistication of these components.
目次
Manufacturing the Vacuum Dustbox
Designing the Dustbox
The first step in manufacturing a vacuum dustbox is the design.
Engineers and designers collaborate to create a dustbox that is both efficient and user-friendly.
The design process typically begins with computer-aided design (CAD) software, which allows the team to visualize the dustbox and make necessary adjustments.
The design must ensure that the dustbox fits within the body of the vacuum cleaner and maximizes the space available for dust collection.
Additionally, the design should consider ease of removal and installation by the user.
Prototyping and Testing
Once the design is finalized, the next step is creating a prototype.
This prototype is typically 3D-printed and then subjected to rigorous testing.
The testing phase ensures that the dustbox can withstand regular use and easily retain dust without leaks.
Any flaws or design issues identified during testing are rectified before proceeding to mass production.
Material Selection
The choice of material for the dustbox is crucial, as it must be durable, lightweight, and capable of containing dust without cracking or breaking.
Common materials used include high-impact plastic and sometimes metal for high-end models.
Polypropylene and acrylonitrile-butadiene-styrene (ABS) are popular choices due to their strength and resistance to impacts.
Molding and Shaping
After selecting the appropriate material, the manufacturing process begins with injection molding.
In this process, melted plastic is injected into a mold shaped like the dustbox.
Once cooled, the plastic hardens, and the mold opens to reveal the newly formed dustbox.
This method ensures a consistent and precise shape for every dustbox produced.
Any excess material or burrs from the molding process are trimmed to ensure smooth edges.
Integration of Filter Technology
Understanding Filter Requirements
Filters are critical in preventing dust and allergens from being released back into the air during vacuuming.
There are different types of filters, such as HEPA (High-Efficiency Particulate Air) filters, foam filters, and cloth filters.
The choice of filter depends on the vacuum cleaner’s intended use and the level of filtration required.
Designing the Filter Mechanism
The filter mechanism must be designed to fit seamlessly within the dustbox.
Engineers ensure that the filter is positioned for optimal airflow while maximizing dust retention.
This often involves creating a specific compartment or housing within the dustbox to hold the filter securely.
Easy access to the filter for cleaning or replacement is also a key consideration in the design.
Filter Material and Fabrication
The materials used for filters vary based on their purpose.
HEPA filters, for instance, are made from very fine glass fibers, while foam filters use porous foam material.
The fabrication process involves layering or shaping these materials into the desired filter form.
HEPA filters are often pleated to increase the surface area, resulting in better filtration efficiency.
Once fabricated, the filters are tested for efficiency and durability.
Assembling the Filter and Dustbox
The final step involves integrating the filter into the dustbox.
The filter is placed into its designated compartment, ensuring that it fits snugly and securely.
Some designs feature a locking mechanism or snaps to hold the filter in place and prevent shifting during use.
After assembly, the dustbox undergoes a final quality check to ensure it meets all design specifications and performance standards.
Quality Assurance and Final Testing
Before vacuum dustboxes are released to the market, they undergo rigorous quality assurance and testing procedures.
These checks ensure that each dustbox performs as expected and meets safety standards.
Testing includes checking the durability of the dustbox, the fit and security of the filter, and overall performance in a vacuum cleaner.
Any units that fail to meet standards are either reworked or scrapped to maintain high quality.
Sustainability in Manufacturing
Manufacturers are increasingly focusing on sustainability in their production processes.
This includes using recyclable materials for both the dustbox and the filters.
Efforts are made to minimize waste during manufacturing, and any excess material is often recycled.
Furthermore, some companies are researching biodegradable filter materials to reduce environmental impact.
By understanding the manufacturing process and the integration of filter technology, we can appreciate the precision and engineering involved in creating vacuum dustboxes.
These components, though often overlooked, play a crucial role in the efficiency and performance of modern vacuum cleaners.
Continuing advancements in materials and design promise even more effective and environmentally friendly solutions in the future.
資料ダウンロード
QCD調達購買管理クラウド「newji」は、調達購買部門で必要なQCD管理全てを備えた、現場特化型兼クラウド型の今世紀最高の購買管理システムとなります。
ユーザー登録
調達購買業務の効率化だけでなく、システムを導入することで、コスト削減や製品・資材のステータス可視化のほか、属人化していた購買情報の共有化による内部不正防止や統制にも役立ちます。
NEWJI DX
製造業に特化したデジタルトランスフォーメーション(DX)の実現を目指す請負開発型のコンサルティングサービスです。AI、iPaaS、および先端の技術を駆使して、製造プロセスの効率化、業務効率化、チームワーク強化、コスト削減、品質向上を実現します。このサービスは、製造業の課題を深く理解し、それに対する最適なデジタルソリューションを提供することで、企業が持続的な成長とイノベーションを達成できるようサポートします。
オンライン講座
製造業、主に購買・調達部門にお勤めの方々に向けた情報を配信しております。
新任の方やベテランの方、管理職を対象とした幅広いコンテンツをご用意しております。
お問い合わせ
コストダウンが利益に直結する術だと理解していても、なかなか前に進めることができない状況。そんな時は、newjiのコストダウン自動化機能で大きく利益貢献しよう!
(Β版非公開)