- お役立ち記事
- Manufacturing Process of Automatic Tissue Dispensers and Strengthening Sensor Control Functions
Manufacturing Process of Automatic Tissue Dispensers and Strengthening Sensor Control Functions
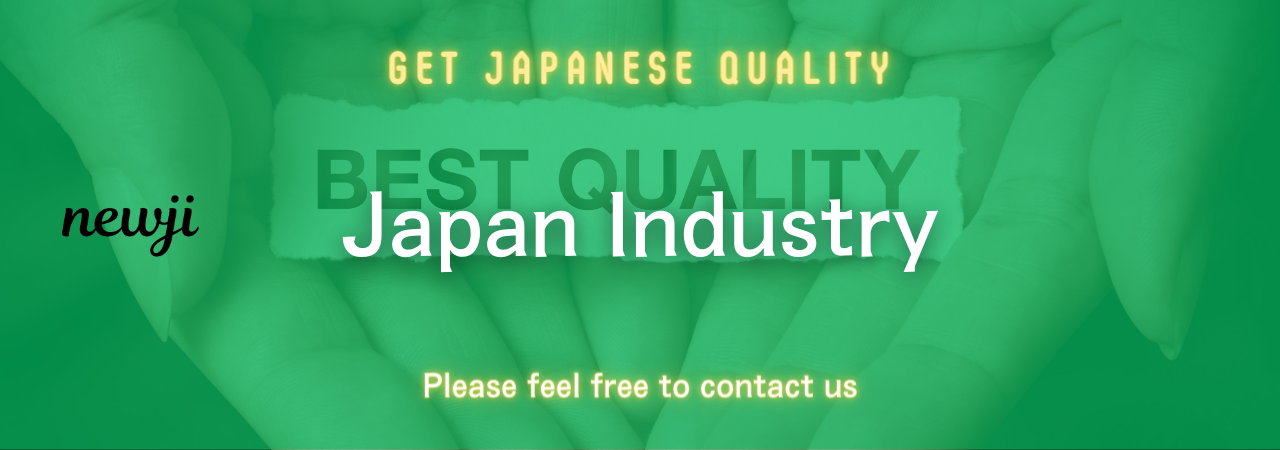
目次
Introduction to Automatic Tissue Dispensers
Automatic tissue dispensers have become a crucial part of maintaining hygiene in various public spaces.
From malls and offices to hospitals and schools, these devices ensure that tissues are dispensed efficiently without the need for physical contact.
Apart from their hygienic benefits, automatic tissue dispensers also offer convenience and reduce waste, as they dispense a single tissue at a time.
Understanding the manufacturing process and the sensor control functions that make these devices so efficient is essential for businesses and consumers alike.
Raw Materials and Initial Preparations
The manufacturing process of automatic tissue dispensers begins with sourcing high-quality raw materials.
Most dispensers are made from durable plastics, such as ABS (Acrylonitrile Butadiene Styrene) and polypropylene, which offer resistance to impact and wear.
Metal components, including springs and brackets, are typically made from stainless steel to prevent rusting, ensuring the longevity of the dispenser.
Once the materials are sourced, they undergo rigorous quality checks to ensure they meet industry standards.
Only materials that pass these checks proceed to the next stage of production.
Molds for plastic components are designed using computer-aided design (CAD) software to ensure precision.
The materials are then molded into the required shapes using injection molding machines.
Assembling the Mechanical Framework
After the individual components are created, the next stage involves assembling the mechanical framework of the dispenser.
This process typically starts with the base of the dispenser, where internal mechanisms are housed.
Springs, gears, and other moving parts are fixed into place carefully to ensure smooth operation.
Technicians use precision tools to secure these components, adjusting them as needed to ensure they are aligned correctly.
The dispensers often feature a storage compartment designed to hold a stack of tissues, arranged so that one tissue is dispensed with each use.
As part of the assembly process, these storage compartments are installed and tested to ensure they function seamlessly.
Integrating Sensor Control Functions
One of the most critical aspects of an automatic tissue dispenser is its sensor control function.
These sensors detect when a hand is placed in front of the dispenser, triggering the mechanism to release a tissue.
Typically, infrared (IR) sensors are used due to their reliability and accuracy.
Integrating the sensor control functions starts with installing the IR sensors into pre-designated slots in the dispenser.
Wires from the sensors are connected to a central control circuit.
This circuit is responsible for interpreting signals from the sensors and activating the dispensing mechanism.
Programming and Calibrating Sensors
Once the sensors are installed, they need to be programmed and calibrated for optimal performance.
Technicians use specialized software to configure the sensors, ensuring they can accurately detect hand movements at the intended distance.
Calibration involves adjusting the sensitivity of the sensors.
The aim is to make sure they respond correctly to hand movements while avoiding false triggers from other movements or environmental factors.
Testing Sensor Accuracy
After programming and calibration, extensive testing is conducted to check the accuracy of the sensors.
Various tests simulate different scenarios, ensuring the sensors consistently detect hand movements and trigger the dispensing mechanism effectively.
Any issues found during this testing phase are addressed by fine-tuning the sensor settings or making necessary adjustments to the internal components.
Final Assembly and Quality Control
With the mechanical framework and sensor functions in place, the next stage is the final assembly of the dispenser.
This involves attaching the outer casing, which protects the internal components and gives the dispenser its finished look.
The outer casing is typically made from the same durable plastic as the internal parts and is designed to be both functional and aesthetically pleasing.
Quality control is a crucial part of the final assembly process.
Each dispenser undergoes a series of tests to verify that all components work together seamlessly.
Technicians check for any defects, ensuring that the dispensers meet industry standards before they are packaged and shipped.
Performing Operational Tests
Operational tests are performed to ensure the dispenser works as intended.
This includes checking the dispensing rate, sensor responsiveness, and overall durability of the device.
Tissue stacks are loaded into the dispenser, and multiple usage cycles are simulated to test its reliability.
Addressing Potential Issues
If any issues are identified during the operational tests, they are addressed before the dispensers are approved for shipment.
This may involve making minor adjustments or replacing faulty components.
The goal is to ensure that every unit leaving the manufacturing facility is of the highest quality.
Packaging and Distribution
Once the dispensers pass quality control checks, they move to the packaging stage.
Each unit is carefully packaged to prevent damage during transportation.
Instructions for installation and usage are included in the packaging to help end-users set up their dispensers correctly.
The packaged dispensers are then distributed to various retailers, businesses, and other clients.
Ensuring Safe Delivery
Measures are taken to ensure the dispensers are delivered safely and in perfect working condition.
This involves coordinating with reliable logistics companies and tracking shipments until they reach their destination.
Customer Support and Feedback
After the dispensers are distributed, manufacturers often provide customer support to address any questions or issues from buyers.
Feedback from customers is valuable, as it helps manufacturers make improvements in future models.
Conclusion
The manufacturing process of automatic tissue dispensers is intricate, involving multiple stages from material sourcing to final assembly and testing.
Integrating and calibrating sensor control functions is a key element that ensures these devices are both efficient and reliable.
Continuous innovation and quality control are essential in producing dispensers that meet the hygiene and convenience needs of today’s public spaces.
Understanding this process not only highlights the importance of each phase but also showcases the technology and precision that go into creating these essential devices.
資料ダウンロード
QCD調達購買管理クラウド「newji」は、調達購買部門で必要なQCD管理全てを備えた、現場特化型兼クラウド型の今世紀最高の購買管理システムとなります。
ユーザー登録
調達購買業務の効率化だけでなく、システムを導入することで、コスト削減や製品・資材のステータス可視化のほか、属人化していた購買情報の共有化による内部不正防止や統制にも役立ちます。
NEWJI DX
製造業に特化したデジタルトランスフォーメーション(DX)の実現を目指す請負開発型のコンサルティングサービスです。AI、iPaaS、および先端の技術を駆使して、製造プロセスの効率化、業務効率化、チームワーク強化、コスト削減、品質向上を実現します。このサービスは、製造業の課題を深く理解し、それに対する最適なデジタルソリューションを提供することで、企業が持続的な成長とイノベーションを達成できるようサポートします。
オンライン講座
製造業、主に購買・調達部門にお勤めの方々に向けた情報を配信しております。
新任の方やベテランの方、管理職を対象とした幅広いコンテンツをご用意しております。
お問い合わせ
コストダウンが利益に直結する術だと理解していても、なかなか前に進めることができない状況。そんな時は、newjiのコストダウン自動化機能で大きく利益貢献しよう!
(Β版非公開)