- お役立ち記事
- Best Practices to Improve Welding Quality for SMEs
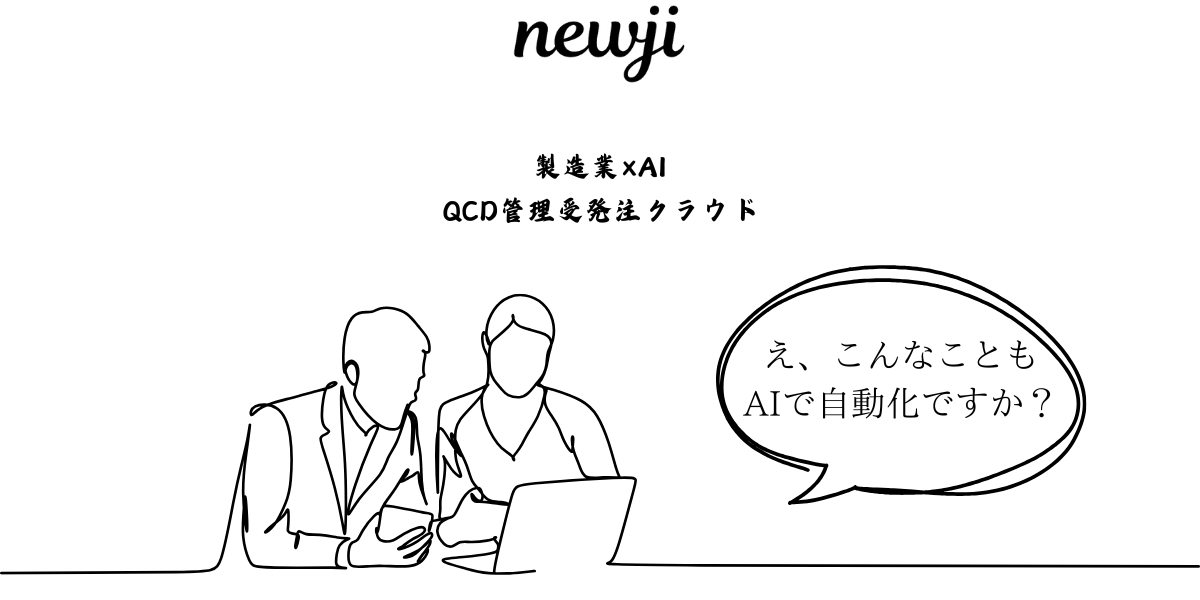
Best Practices to Improve Welding Quality for SMEs
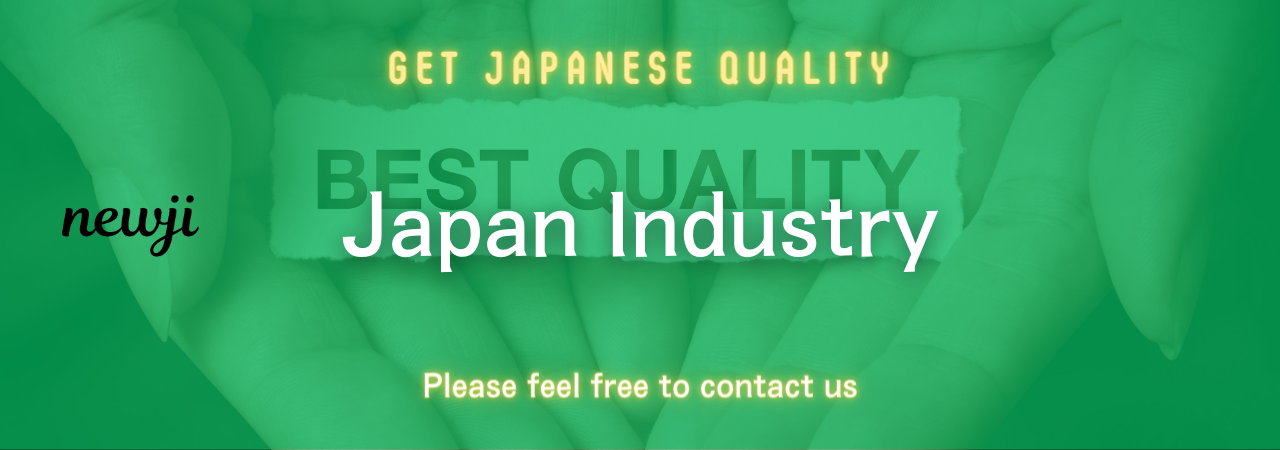
Welding quality is crucial for small and medium-sized enterprises (SMEs) involved in manufacturing, construction, and other industries.
Ensuring high-quality welds not only enhances product durability but also minimizes costs and rework.
In this article, we will explore some best practices to improve welding quality for SMEs.
目次
Understanding the Basics of Welding
Before diving into advanced practices, let’s revisit the basics.
Welding is a fabrication process that joins materials, usually metals, by causing coalescence.
This is typically done by melting the workpieces and adding a filler material.
The most common welding techniques include MIG (Metal Inert Gas), TIG (Tungsten Inert Gas), and ARC welding.
Training and Certification
Invest in Employee Training
Investing in employee training is one of the most effective ways to improve welding quality.
Properly trained welders are more likely to produce high-quality welds.
Regular training sessions on the latest welding techniques and safety measures can make a significant difference.
Importance of Certification
Encouraging welders to obtain certification from reputable organizations can also boost quality.
Certification programs ensure that welders possess the necessary skills and knowledge.
Certified welders often have a competitive edge and are more trusted by clients.
Choosing the Right Materials
Quality of Raw Materials
The quality of raw materials used in welding directly impacts the final product.
Using high-quality metals and filler materials can significantly improve weld durability and strength.
Ensure that your suppliers provide certified materials that meet industry standards.
Material Compatibility
Different materials have different properties and melting points.
Using incompatible metals can lead to weak welds.
Always ensure that the materials being welded are compatible to avoid issues later on.
Maintaining Equipment
Regular Maintenance
Welding equipment should be regularly inspected and maintained.
Faulty equipment can lead to poor weld quality and pose safety risks.
Implement a routine maintenance schedule to keep equipment in optimal condition.
Upgrading Equipment
Outdated equipment can hinder welding quality.
Modern welding machines come with advanced features that enhance precision and efficiency.
Consider upgrading old equipment to take advantage of these technologies.
Implementing Quality Control Measures
Pre-Welding Inspection
Conducting pre-welding inspections can help identify potential issues before they escalate.
Check for material defects, contamination, and proper alignment.
Pre-welding inspections can save time and resources by preventing costly rework.
Post-Welding Inspection
Post-welding inspections are equally important.
Use techniques like X-ray or ultrasonic testing to detect flaws that are not visible to the naked eye.
Addressing these flaws immediately can ensure the final product meets quality standards.
Optimizing Welding Parameters
Proper Heat Control
Controlling the amount of heat applied during welding is crucial.
Too much heat can weaken the material, while too little heat can result in weak welds.
Adjust welding parameters like current, voltage, and speed to achieve optimal heat control.
Shielding Gas Selection
The type of shielding gas used in MIG and TIG welding also affects weld quality.
Different gases offer varying levels of protection against oxidation and contamination.
Choose the right shielding gas based on the materials being welded to ensure high-quality welds.
Work Environment
Clean and Organized Workspace
A clean and organized workspace can significantly impact welding quality.
Contaminants like dust and grease can affect weld integrity.
Ensure that the welding area is free from these contaminants.
Proper Ventilation
Proper ventilation is essential for welding safety and quality.
Poor ventilation can lead to the accumulation of harmful fumes, affecting both the welder and the weld quality.
Install adequate ventilation systems to ensure a safer and more efficient work environment.
Documentation and Record-Keeping
Maintain Welding Records
Keeping detailed records of welding activities can help identify recurring issues and areas for improvement.
Document parameters like material type, welding technique, and inspection results.
This information can be invaluable for future reference and quality assurance.
Update Procedures Regularly
Welding procedures should be reviewed and updated regularly.
As new technologies and techniques emerge, updating your standard operating procedures can help maintain high welding quality.
Regularly review and update procedures to keep pace with industry advancements.
By following these best practices, SMEs can significantly improve welding quality.
Investing in training, choosing the right materials, maintaining equipment, and implementing quality control measures can make a substantial difference.
Moreover, optimizing welding parameters, ensuring a clean work environment, and maintaining proper documentation are essential steps toward achieving high-quality welds.
Adopting these best practices will not only enhance product quality but also boost customer satisfaction and business growth.
資料ダウンロード
QCD調達購買管理クラウド「newji」は、調達購買部門で必要なQCD管理全てを備えた、現場特化型兼クラウド型の今世紀最高の購買管理システムとなります。
ユーザー登録
調達購買業務の効率化だけでなく、システムを導入することで、コスト削減や製品・資材のステータス可視化のほか、属人化していた購買情報の共有化による内部不正防止や統制にも役立ちます。
NEWJI DX
製造業に特化したデジタルトランスフォーメーション(DX)の実現を目指す請負開発型のコンサルティングサービスです。AI、iPaaS、および先端の技術を駆使して、製造プロセスの効率化、業務効率化、チームワーク強化、コスト削減、品質向上を実現します。このサービスは、製造業の課題を深く理解し、それに対する最適なデジタルソリューションを提供することで、企業が持続的な成長とイノベーションを達成できるようサポートします。
オンライン講座
製造業、主に購買・調達部門にお勤めの方々に向けた情報を配信しております。
新任の方やベテランの方、管理職を対象とした幅広いコンテンツをご用意しております。
お問い合わせ
コストダウンが利益に直結する術だと理解していても、なかなか前に進めることができない状況。そんな時は、newjiのコストダウン自動化機能で大きく利益貢献しよう!
(Β版非公開)