- お役立ち記事
- The Manufacturing Process for Wooden Clocks and Precision Component Machining
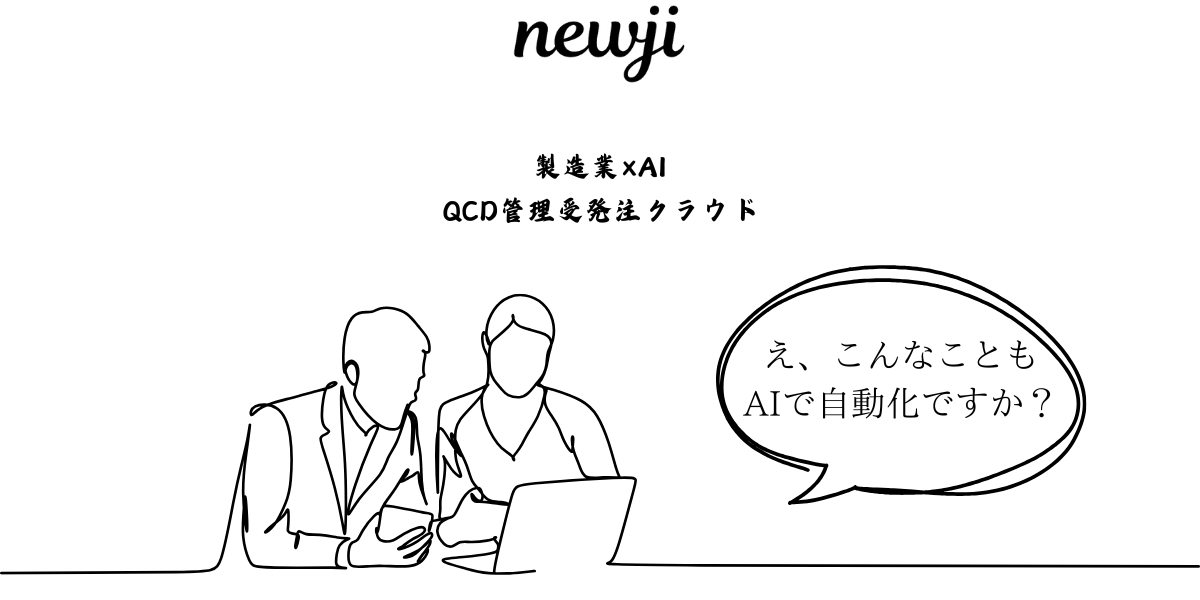
The Manufacturing Process for Wooden Clocks and Precision Component Machining
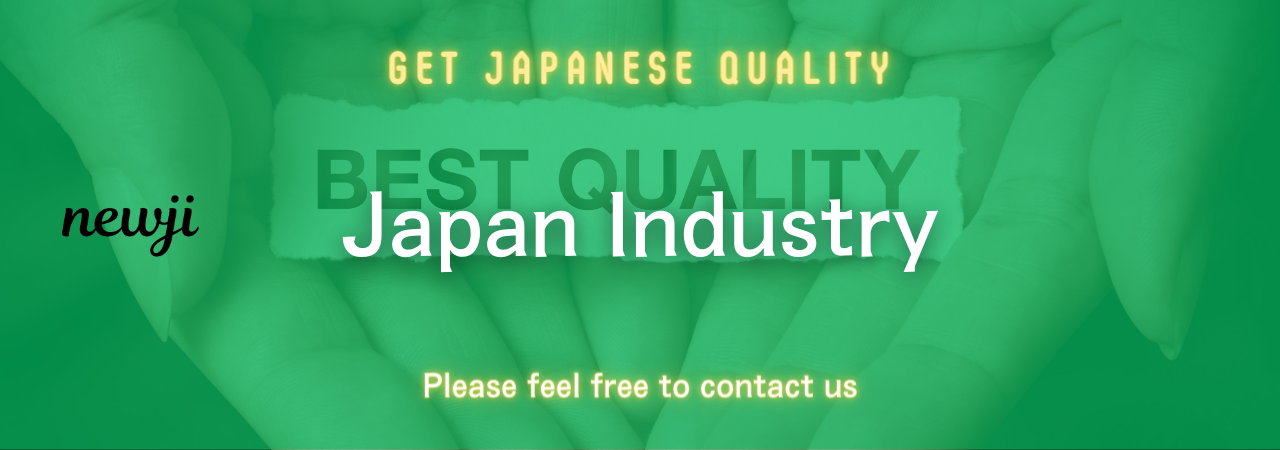
The art of creating wooden clocks blends traditional craftsmanship with modern precision machining techniques.
Understanding how these clocks are made involves diving into a step-by-step process that ensures both beauty and functionality.
In this article, we’ll explore the detailed processes involved in manufacturing wooden clocks and discuss the precision required in producing their components.
目次
Selecting the Right Wood
The first step in making a wooden clock is choosing the right type of wood.
The choice of wood plays a crucial role in the clock’s aesthetic and durability.
Commonly used woods include mahogany, oak, maple, and cherry.
These woods are known for their strength, stability, and beautiful grain patterns.
Wood is inspected for any defects, such as knots or cracks, that might affect the clock’s structural integrity.
After selection, the wood is cut into rough shapes using a bandsaw or a jigsaw, creating the basic pieces that will form the clock body and face.
Sanding and Shaping
Once the wood has been cut to size, the pieces are carefully sanded to achieve smooth and even surfaces.
This step is essential to ensure that the pieces fit together perfectly and that the final product has a professional finish.
Sanding can be done using various grits of sandpaper, starting with a coarse grit and gradually moving to finer grits.
Shaping involves carving and routing the wood pieces to achieve the desired contours and details.
This may include creating grooves for clock hands, intricate designs on the clock face, or beveling the edges for a refined look.
Router tools and chisels are often used for these tasks, requiring a steady hand and precision.
Assembling the Clock Body
After the individual wooden pieces are sanded and shaped, they are assembled to form the clock body.
This process involves gluing the pieces together and securing them with clamps until the glue dries.
Precision is key to ensure that all parts align perfectly, and that the clock looks symmetrical and balanced.
Joinery techniques, like dovetails or mortise and tenon, might be used to increase the clock’s strength and durability.
These techniques involve interlocking pieces of wood, creating strong joints without the need for nails or screws.
Precision Component Machining
The accuracy of a wooden clock depends heavily on the precision of its internal components.
While the exterior of the clock is crafted from wood, the internal mechanisms—gears, escapements, and hands—are often made from metals or synthetic materials.
These components are manufactured using precision machining techniques to ensure accurate timekeeping.
Creating Gears
Gears are crucial for the proper functioning of a clock.
They translate the energy from the clock’s power source into the controlled movement of the hands.
Creating gears requires high precision machining to achieve the correct tooth profile and spacing.
Computer Numerical Control (CNC) machines are used to manufacture gears with extreme accuracy.
These machines are programmed with digital designs that guide the cutting tools to shape the gears precisely.
This ensures that the gears mesh correctly and operate smoothly without too much friction.
Making the Escapement
The escapement mechanism regulates the release of energy from the clock’s power source (such as a spring or weight) to the gear train.
It is essential for maintaining consistent time intervals.
The escapement consists of several parts, including the escape wheel and the anchor.
Each piece must be machined with exact specifications.
Errors in the machining process can result in inaccurate timekeeping.
Crafting the Hands
The minute, hour, and second hands of a clock must be lightweight and balanced.
They are typically made from metals like aluminum, brass, or stainless steel.
These materials can be machined into precise shapes and polished for a smooth finish.
During machining, each hand is cut to the correct length and width, then shaped and balanced to ensure it moves accurately on the clock face without wobbling.
Final Assembly and Testing
With all components ready, the final assembly of the clock begins.
The internal mechanism, including gears, escapements, and hands, is installed within the wooden clock body.
Every part must be placed accurately to ensure proper functionality.
Once assembled, the clock undergoes rigorous testing.
This involves calibrating the timekeeping mechanism, checking the alignment of the gears, and ensuring that the hands move smoothly and accurately.
Any necessary adjustments are made to fine-tune the clock’s performance.
Finishing Touches
The final step in manufacturing a wooden clock is applying the finishing touches.
This includes staining or painting the wood to enhance its natural beauty and protect it from moisture and wear.
A clear varnish or lacquer is usually applied to provide a glossy finish and further protection.
Additional decorative elements, such as engravings, inlays, or decorative moldings, may be added to give the clock a unique appearance.
These embellishments are often done by hand, requiring artistic skill and attention to detail.
Ensuring Quality and Craftsmanship
The entire process of creating a wooden clock, from selecting the wood to applying the final finish, requires a high level of craftsmanship and precision.
Every step is crucial to ensuring that the clock is not only aesthetically pleasing but also highly functional.
Manufacturers must adhere to strict quality control standards, inspecting every component and assembly step to ensure the final product meets the desired specifications.
Attention to detail and a commitment to excellence are essential in producing a wooden clock that stands the test of time.
In conclusion, the manufacturing process for wooden clocks and their precision components is a fascinating blend of traditional woodworking techniques and modern machining technology.
This intricate process ensures that each clock is a beautiful and accurate timepiece, reflecting the skill and dedication of its makers.
資料ダウンロード
QCD調達購買管理クラウド「newji」は、調達購買部門で必要なQCD管理全てを備えた、現場特化型兼クラウド型の今世紀最高の購買管理システムとなります。
ユーザー登録
調達購買業務の効率化だけでなく、システムを導入することで、コスト削減や製品・資材のステータス可視化のほか、属人化していた購買情報の共有化による内部不正防止や統制にも役立ちます。
NEWJI DX
製造業に特化したデジタルトランスフォーメーション(DX)の実現を目指す請負開発型のコンサルティングサービスです。AI、iPaaS、および先端の技術を駆使して、製造プロセスの効率化、業務効率化、チームワーク強化、コスト削減、品質向上を実現します。このサービスは、製造業の課題を深く理解し、それに対する最適なデジタルソリューションを提供することで、企業が持続的な成長とイノベーションを達成できるようサポートします。
オンライン講座
製造業、主に購買・調達部門にお勤めの方々に向けた情報を配信しております。
新任の方やベテランの方、管理職を対象とした幅広いコンテンツをご用意しております。
お問い合わせ
コストダウンが利益に直結する術だと理解していても、なかなか前に進めることができない状況。そんな時は、newjiのコストダウン自動化機能で大きく利益貢献しよう!
(Β版非公開)