- お役立ち記事
- The difference between Material Ordering and Parts Ordering
The difference between Material Ordering and Parts Ordering
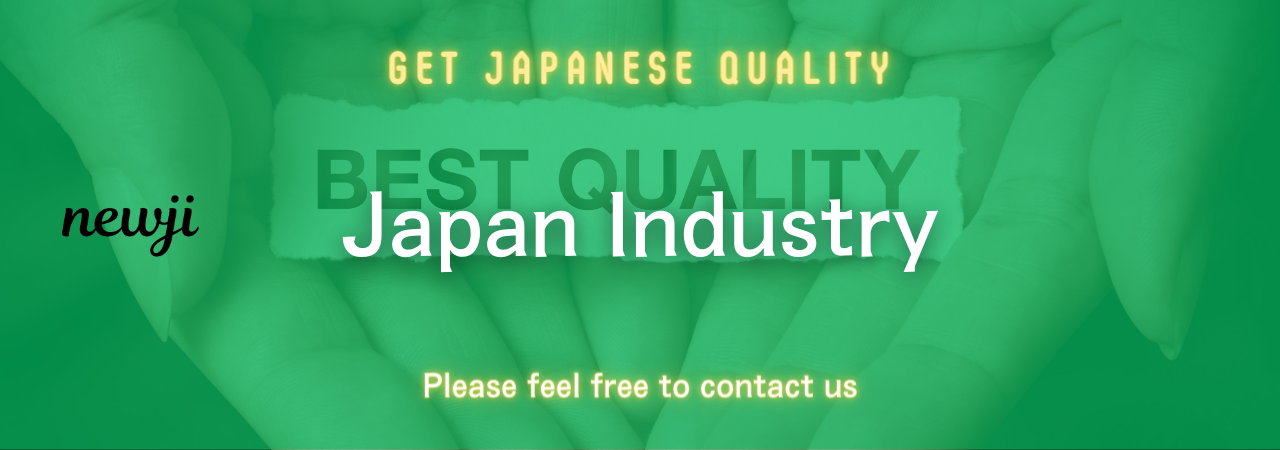
In the world of manufacturing, understanding the differences between material ordering and parts ordering is crucial.
These two processes, while seemingly similar, play distinct roles in the production and supply chain.
Knowing how each function can help you manage resources more effectively, improve efficiency, and ensure the timely completion of projects.
目次
What is Material Ordering?
Material ordering is the process of procuring raw materials required for manufacturing or production.
These materials are not yet processed or constructed into parts that will eventually form the final product.
Think of raw materials as the building blocks needed to create something new.
For instance, in the construction industry, materials might include cement, steel beams, and wood.
In the textile industry, materials could be different types of fabric, threads, and dyes.
Material ordering involves identifying suppliers, negotiating purchase agreements, and ensuring timely delivery of these raw materials to the manufacturing site.
This process can be complex, as it often requires careful planning and coordination with various departments within a company.
Failing to manage material ordering effectively can result in project delays and increased costs.
What is Parts Ordering?
Parts ordering, on the other hand, involves procuring components that have already been manufactured and are ready to be assembled into a final product.
These parts are typically standardized and designed to fit together in a particular way.
For example, in the automotive industry, parts ordering might include purchasing engines, transmissions, and brakes that are then assembled into a complete vehicle.
In electronics manufacturing, parts could include circuit boards, processors, and battery packs.
Like material ordering, parts ordering requires careful coordination and planning.
However, it often involves managing a different set of supplier relationships, and the logistics of handling parts can be more intricate given their specific design and compatibility requirements.
Key Differences Between Material Ordering and Parts Ordering
Understanding the key differences between material ordering and parts ordering can help streamline your operations.
Let’s delve deeper into these distinctions.
Nature of Items Ordered
The primary difference lies in the nature of the items ordered.
Material ordering involves acquiring substances in their raw form, around which the manufacturing process is built.
Parts ordering involves purchasing pre-manufactured components that are ready to be assembled.
Supplier Relationships
The types of suppliers you work with in each process tend to differ.
Raw material suppliers often specialize in bulk materials and may offer customization options to meet specific manufacturing needs.
Suppliers for parts ordering typically provide standardized components and parts designed to fit certain specifications.
Complexity of Management
Material ordering can involve more complex logistics and inventory management since raw materials often need to be stored, moved, and processed before they can be used.
Parts ordering, while also complex, often focuses on ensuring compatibility and assembling components correctly.
Lead Times
Lead times can vary significantly between these two processes.
Material ordering may require longer lead times due to the nature of raw materials procurement and initial processing requirements.
Parts ordering might have shorter lead times if the parts are standardized and readily available from suppliers.
Cost Considerations
The cost factors also differ.
Material ordering may involve bulk purchasing discounts but can also incur costs related to storage and handling.
Parts ordering may come with higher upfront costs per unit due to the added value and labor involved in manufacturing those components.
When to Use Material Ordering
Material ordering is ideal when you need specific materials to create a custom or unique product.
It’s especially useful in industries like construction, textiles, and certain types of manufacturing where raw materials form the core of production.
If your business model relies on transforming raw materials into a final product, you’ll need a robust material ordering process to keep your operations running smoothly.
When to Use Parts Ordering
Parts ordering is best suited for scenarios where you need to assemble pre-existing components into a finished product.
This approach is common in industries such as automotive manufacturing, electronics, and consumer goods.
If your production process revolves around assembling specific parts into a cohesive whole, efficient parts ordering is critical to your success.
Integrating Both Processes
In many businesses, both material ordering and parts ordering need to coexist harmoniously.
Effective integration of these processes can significantly enhance efficiency and productivity.
Inventory Management
Strong inventory management practices can help balance the needs of both material and parts ordering.
This includes monitoring stock levels, forecasting demand, and ensuring timely reordering.
Supplier Coordination
Working closely with suppliers to manage lead times, delivery schedules, and quality assurance is crucial.
Whether dealing with raw materials or parts, maintaining good supplier relationships can help prevent delays and disruptions.
Technology and Automation
Leveraging technology and automation can streamline both material and parts ordering processes.
Inventory management systems, automated ordering processes, and supply chain management software can help track orders, manage stock levels, and ensure timely deliveries.
Cross-Functional Collaboration
Ensuring good communication and collaboration between different departments, such as procurement, production, and logistics, is essential.
This can help align material and parts ordering processes with overall business goals and production schedules.
In conclusion, while material ordering and parts ordering serve different purposes within the manufacturing and production landscape, both are integral to successful operations.
By understanding the unique aspects of each process, you can better manage your supply chain, optimize resources, and meet your production goals more effectively.
資料ダウンロード
QCD調達購買管理クラウド「newji」は、調達購買部門で必要なQCD管理全てを備えた、現場特化型兼クラウド型の今世紀最高の購買管理システムとなります。
ユーザー登録
調達購買業務の効率化だけでなく、システムを導入することで、コスト削減や製品・資材のステータス可視化のほか、属人化していた購買情報の共有化による内部不正防止や統制にも役立ちます。
NEWJI DX
製造業に特化したデジタルトランスフォーメーション(DX)の実現を目指す請負開発型のコンサルティングサービスです。AI、iPaaS、および先端の技術を駆使して、製造プロセスの効率化、業務効率化、チームワーク強化、コスト削減、品質向上を実現します。このサービスは、製造業の課題を深く理解し、それに対する最適なデジタルソリューションを提供することで、企業が持続的な成長とイノベーションを達成できるようサポートします。
オンライン講座
製造業、主に購買・調達部門にお勤めの方々に向けた情報を配信しております。
新任の方やベテランの方、管理職を対象とした幅広いコンテンツをご用意しております。
お問い合わせ
コストダウンが利益に直結する術だと理解していても、なかなか前に進めることができない状況。そんな時は、newjiのコストダウン自動化機能で大きく利益貢献しよう!
(Β版非公開)