- お役立ち記事
- Manufacturing Process of Acrylic Display Cases and Transparency Enhancement
Manufacturing Process of Acrylic Display Cases and Transparency Enhancement
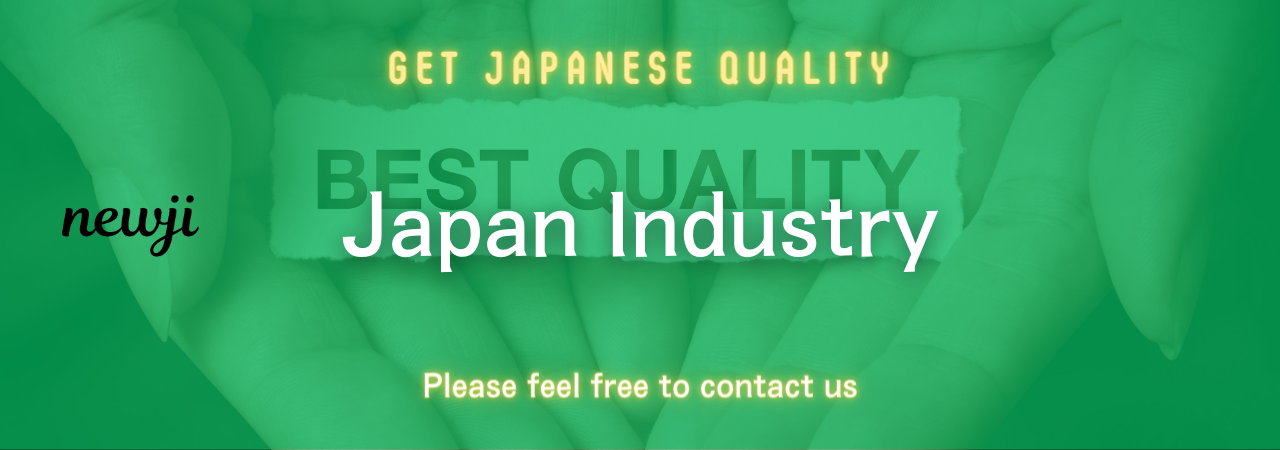
Acrylic display cases are omnipresent in various industries, from retail to museum exhibitions, due to their excellent clarity and durability.
This article will delve into the manufacturing process of acrylic display cases and explore ways to enhance their transparency.
目次
Understanding Acrylic: A Brief Overview
Acrylic, scientifically known as polymethyl methacrylate (PMMA), is a transparent thermoplastic often used as a lightweight and shatter-resistant alternative to glass.
This material has gained popularity for its exceptional clarity, impact resistance, and versatility.
Acrylic is available under various brand names, such as Plexiglas, Lucite, and Perspex.
The Manufacturing Process of Acrylic Display Cases
Step 1: Material Selection
The first step in manufacturing acrylic display cases is choosing the right type of acrylic sheet.
Manufacturers often opt for cast acrylic sheets due to their superior optical clarity and resistance to chemical reactions.
These sheets come in various thicknesses and are selected based on the specific requirements of the display case.
Step 2: Cutting the Acrylic
Once the suitable acrylic sheet is selected, it is precisely cut into the desired shapes and sizes.
This is typically done using laser cutting or CNC (Computer Numerical Control) machines.
Laser cutting offers high precision and leaves a polished edge, reducing the need for further finishing.
Step 3: Shaping and Forming
After cutting, the acrylic pieces are shaped and formed into the desired design.
This involves bending, molding, and thermoforming the acrylic sheets using specialized equipment.
Thermoforming, in particular, involves heating the acrylic sheet until it becomes pliable and then shaping it over a mold.
The sheet is then cooled and retains its new shape.
Step 4: Joining and Bonding
The individual acrylic pieces are then joined together using solvent welding or adhesive bonding.
Solvent welding involves using a solvent that partially dissolves the surfaces of the acrylic pieces, which then fuses them together as the solvent evaporates.
This method provides a strong, nearly invisible bond.
Alternatively, manufacturers may use specialized acrylic adhesives for a more straightforward bonding process.
Step 5: Polishing and Finishing
To achieve a high level of transparency and aesthetic appeal, the edges and surfaces of the acrylic display case are thoroughly polished.
This is done using a series of abrasives, followed by buffing with polishing compounds.
The goal is to remove any scratches, irregularities, or haziness, resulting in a crystal-clear finish.
Enhancing Transparency in Acrylic Display Cases
Choosing Quality Materials
The choice of material is paramount in ensuring optimal transparency.
High-quality cast acrylic sheets are preferred over extruded sheets as they offer better optical clarity and are less prone to yellowing over time.
Manufacturers should source acrylic sheets from reputable suppliers to guarantee consistency in quality.
Implementing Proper Cutting Techniques
Using advanced cutting methods, such as laser cutting, can significantly enhance the transparency of acrylic display cases.
Laser cutting not only provides precise cuts but also results in polished edges that require minimal post-processing.
Maintaining a Clean Working Environment
A clean working environment is essential to prevent contamination and debris from getting trapped in the acrylic sheets during the manufacturing process.
Dust and particles can cause surface imperfections that negatively impact transparency.
Regular cleaning and maintenance of the workspace and equipment are crucial.
Polishing and Buffing
Effective polishing and buffing techniques are vital for achieving a flawless finish.
Using progressively finer abrasives and specialized polishing compounds help remove any surface imperfections.
Mechanical polishing machines with precise control over speed and pressure can ensure consistent results across all surfaces of the display case.
UV Protection
Exposure to ultraviolet (UV) light can cause acrylic to yellow over time, reducing its transparency.
Incorporating UV-resistant additives during the production of acrylic sheets can help mitigate this issue.
Additionally, applying a UV-protective coating to the finished display case can further extend its clarity and longevity.
Quality Control and Inspection
Implementing rigorous quality control measures at various stages of the manufacturing process ensures that each acrylic display case meets the highest standards of transparency and durability.
Regular inspection for any defects, such as scratches, bubbles, or discoloration, can help identify and address issues early in the production cycle.
Conclusion
The manufacturing process of acrylic display cases involves several critical steps, including material selection, cutting, shaping, joining, and finishing.
To enhance transparency, it is essential to choose high-quality materials, employ precise cutting techniques, maintain a clean working environment, and perform meticulous polishing and buffing.
By incorporating UV protection and implementing rigorous quality control measures, manufacturers can produce acrylic display cases that offer exceptional clarity and durability.
資料ダウンロード
QCD調達購買管理クラウド「newji」は、調達購買部門で必要なQCD管理全てを備えた、現場特化型兼クラウド型の今世紀最高の購買管理システムとなります。
ユーザー登録
調達購買業務の効率化だけでなく、システムを導入することで、コスト削減や製品・資材のステータス可視化のほか、属人化していた購買情報の共有化による内部不正防止や統制にも役立ちます。
NEWJI DX
製造業に特化したデジタルトランスフォーメーション(DX)の実現を目指す請負開発型のコンサルティングサービスです。AI、iPaaS、および先端の技術を駆使して、製造プロセスの効率化、業務効率化、チームワーク強化、コスト削減、品質向上を実現します。このサービスは、製造業の課題を深く理解し、それに対する最適なデジタルソリューションを提供することで、企業が持続的な成長とイノベーションを達成できるようサポートします。
オンライン講座
製造業、主に購買・調達部門にお勤めの方々に向けた情報を配信しております。
新任の方やベテランの方、管理職を対象とした幅広いコンテンツをご用意しております。
お問い合わせ
コストダウンが利益に直結する術だと理解していても、なかなか前に進めることができない状況。そんな時は、newjiのコストダウン自動化機能で大きく利益貢献しよう!
(Β版非公開)