- お役立ち記事
- Manufacturing Process of Indoor Filters and Strengthening Air Purification Functionality
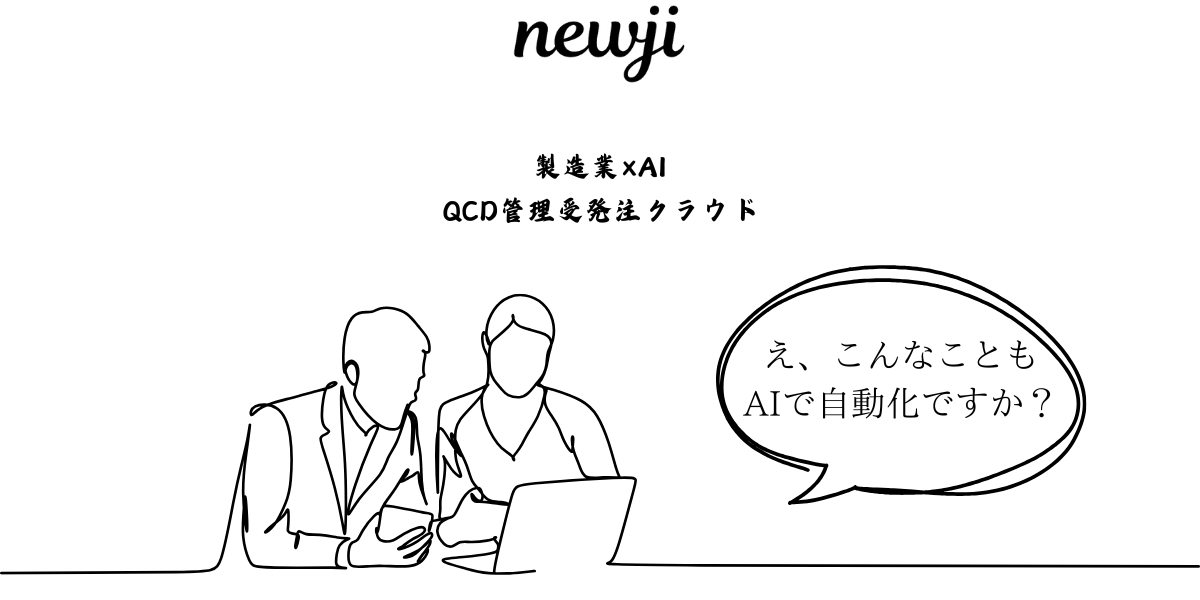
Manufacturing Process of Indoor Filters and Strengthening Air Purification Functionality
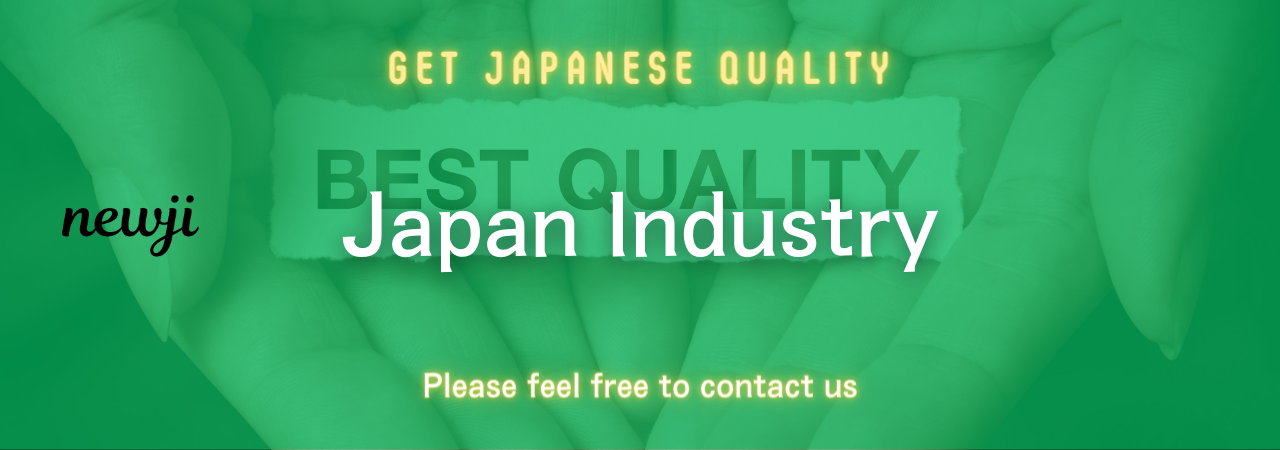
目次
Introduction to Indoor Filters and Their Importance
Indoor filters play a crucial role in maintaining air quality inside homes and workplaces.
They help filter out dust, pollen, pet dander, and other airborne particles, making the environment healthier and more comfortable.
In a world where air pollution is a growing concern, understanding how indoor filters are made and how they function can provide significant benefits to everyone.
Materials Used in Manufacturing Indoor Filters
Main Components
Indoor filters are primarily made from fibrous materials that can catch and hold small particles.
The most common materials include fiberglass, polyester, and paper.
Fiberglass is often used because of its durability and ability to trap large amounts of dust particles.
Polyester and other synthetic fibers are chosen for their fine filtration capabilities and resistance to moisture.
Additional Elements
Certain filters include added layers like carbon or activated charcoal.
These materials specialize in removing odors and chemical pollutants.
Additionally, an electrostatically charged layer may be added to attract and capture finer particles, enhancing the overall filtration efficiency.
The Manufacturing Process of Indoor Filters
Step 1: Selecting the Raw Materials
The first step in making an indoor filter involves selecting high-quality raw materials.
Manufacturers source fiberglass, polyester, and other required materials from reliable suppliers.
The chemical and physical properties of these materials are carefully tested before they are approved for production.
Step 2: Forming the Filter Media
Once the raw materials are ready, they are processed to form the filter media.
For fiberglass filters, molten glass is extruded into thin fibers.
These fibers are then woven or layered to form a mat-like structure.
For polyester filters, synthetic fibers undergo a similar process.
After forming the mat, the material is bathed in a binder solution to improve its structural integrity.
Step 3: Adding Specialized Layers
In this stage, additional layers like activated carbon are added for enhanced filtration.
These layers are uniformly applied to ensure balanced coverage.
The additional materials are pressed and bonded to the primary filter media, creating a composite structure.
Step 4: Cutting and Shaping
The combined filter media is then cut into the required shapes and sizes.
Industrial cutting machines ensure precision to fit various HVAC systems perfectly.
This step is crucial as deviations can affect the filter’s performance and fitting.
Step 5: Assembling the Frame
Once the filter media is cut, it’s time to assemble the filter frame.
Most frames are made from cardboard or metal.
These materials are chosen for their strength and lightweight properties.
The frame is designed to hold the filter media firmly while allowing easy installation and replacement.
Step 6: Quality Control Checks
Before a filter is packaged for sale, it undergoes rigorous quality control tests.
These inspections ensure that the filter meets industry standards for particle retention, airflow, and durability.
Specialized machines test the filter’s ability to capture various particle sizes and maintain optimal airflow.
Strengthening Air Purification Functionality
Upgrading Filter Efficiency
To improve the air purification functionality, manufacturers focus on enhancing filter efficiency.
This can be achieved by increasing the density of the filter media or incorporating advanced technologies like High-Efficiency Particulate Air (HEPA) filters.
HEPA filters are known for their high particle retention rates, capturing up to 99.97% of particles down to 0.3 microns.
Incorporation of Electrostatic Filters
Electrostatic filters leverage an electrically charged filter media to attract and capture airborne particles.
These filters can significantly improve the air purification capability, making them popular in residential and commercial settings.
Active Carbon Layers
The addition of active carbon layers can remove gaseous pollutants and odors, offering superior air purification.
These filters can trap volatile organic compounds (VOCs) and other harmful chemicals, making the indoor air cleaner and safer.
Regular Maintenance and Replacement
Even the best filters need regular maintenance to perform efficiently.
It’s essential to follow the manufacturer’s guidelines for replacement intervals.
Typically, filters should be checked every three months and replaced if they appear dirty or clogged.
Conclusion
Indoor filters play a vital role in ensuring the quality of the air we breathe.
Understanding the manufacturing process helps in appreciating the intricate steps taken to produce effective filters.
By upgrading materials and incorporating advanced filtration technologies, manufacturers continue to improve air purification functionality.
With regular maintenance and timely replacement, indoor filters can significantly enhance the health and comfort of indoor environments.
資料ダウンロード
QCD調達購買管理クラウド「newji」は、調達購買部門で必要なQCD管理全てを備えた、現場特化型兼クラウド型の今世紀最高の購買管理システムとなります。
ユーザー登録
調達購買業務の効率化だけでなく、システムを導入することで、コスト削減や製品・資材のステータス可視化のほか、属人化していた購買情報の共有化による内部不正防止や統制にも役立ちます。
NEWJI DX
製造業に特化したデジタルトランスフォーメーション(DX)の実現を目指す請負開発型のコンサルティングサービスです。AI、iPaaS、および先端の技術を駆使して、製造プロセスの効率化、業務効率化、チームワーク強化、コスト削減、品質向上を実現します。このサービスは、製造業の課題を深く理解し、それに対する最適なデジタルソリューションを提供することで、企業が持続的な成長とイノベーションを達成できるようサポートします。
オンライン講座
製造業、主に購買・調達部門にお勤めの方々に向けた情報を配信しております。
新任の方やベテランの方、管理職を対象とした幅広いコンテンツをご用意しております。
お問い合わせ
コストダウンが利益に直結する術だと理解していても、なかなか前に進めることができない状況。そんな時は、newjiのコストダウン自動化機能で大きく利益貢献しよう!
(Β版非公開)