- お役立ち記事
- Digital Tools to Strengthen QCD Management
Digital Tools to Strengthen QCD Management
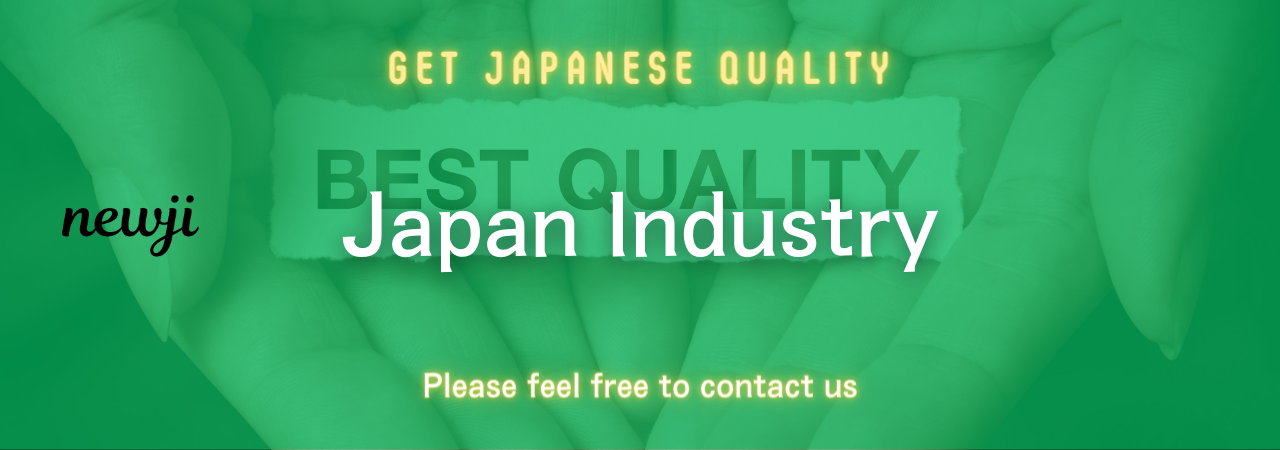
In today’s fast-paced business environment, maintaining high standards in Quality, Cost, and Delivery (QCD) is essential for any organization aiming to stay competitive.
Each component of QCD significantly influences the overall performance, and striking the right balance between them can be challenging.
Fortunately, digital tools are available to simplify QCD management, making it more efficient and effective.
In this article, we will explore how digital tools can strengthen QCD management in your organization.
目次
Understanding QCD Management
QCD management is a methodology used to evaluate and improve the three key performance indicators: Quality, Cost, and Delivery.
Quality ensures that the product or service meets the required standards and expectations of customers.
Cost refers to the expenditure involved in producing the product or service, while Delivery focuses on the timeliness and efficiency with which the product reaches the customer.
Balancing these three elements is crucial.
Improving quality can often lead to increased costs, while reducing costs might impact quality.
Similarly, to meet delivery deadlines, there might be a compromise on either quality or cost.
Therefore, a well-rounded strategy that optimally balances these elements is essential.
Digital Tools for Quality Management
1. Quality Management Systems (QMS)
A Quality Management System is a digital tool that helps ensure products or services meet the desired quality levels.
Overseeing everything from production processes to compliance with regulatory standards, QMS streamlines operations and reduces errors.
It offers functionalities including document control, quality audits, and corrective action tracking.
Implementing a robust QMS will lead to improved product quality and better customer satisfaction.
2. Statistical Process Control (SPC)
Statistical Process Control is a method used to monitor and control a process through statistical methods.
It helps to identify any variations in the production process that could lead to defects.
By using SPC software, organizations can collect and analyze data in real-time, enabling them to react swiftly to any anomalies.
This ensures that the products remain consistent in quality, reducing waste and rework.
Digital Tools for Cost Management
1. Integrated Enterprise Resource Planning (ERP) Systems
An ERP system integrates various business processes like finance, HR, procurement, and production into a single platform.
By making information available across all departments, ERP systems improve decision-making and resource allocation.
They enable better cost management through modules for budgeting, forecasting, and expense tracking.
With real-time data, organizations can proactively identify areas where costs can be reduced without compromising on quality or delivery times.
2. Activity-Based Costing (ABC)
Activity-Based Costing is an accounting method that identifies and assigns costs to overhead activities and then assigns those costs to products.
This method provides a more accurate reflection of the actual costs associated with production.
ABC software tools help organizations allocate resources more effectively and identify areas where cost savings can be achieved.
This leads to enhanced budget control and superior financial performance.
Digital Tools for Delivery Management
1. Supply Chain Management (SCM) Software
Supply Chain Management Software helps in planning, executing, and monitoring the flow of goods and materials.
It manages everything from procurement to delivery to inventory management.
By providing real-time visibility into the supply chain, these tools help organizations optimize processes, reduce lead times, and increase responsiveness to demand changes.
Efficiency in supply chain operations directly impacts the delivery performance, ensuring products reach customers on time.
2. Transportation Management Systems (TMS)
A Transportation Management System is a digital solution that optimizes the planning and execution of transportation processes.
TMS software helps in route planning, carrier selection, and freight allocation.
It tracks shipments in real-time, providing detailed insights into the delivery process.
By using TMS, organizations can reduce transportation costs, improve delivery times, and enhance overall customer satisfaction.
The Role of Data Analytics in QCD Management
Data is incredibly powerful in the realm of QCD management.
By leveraging data analytics, organizations can gain valuable insights into their processes, helping to make informed decisions.
Data analytics tools can analyze historical data to predict future trends, identify inefficiencies, and uncover areas for improvement.
For example, predictive analytics can forecast demand, enabling better inventory management and ensuring timely delivery without overstocking.
Additionally, advanced analytics can pinpoint root causes of quality issues, allowing for quicker resolution and continuous improvement.
Implementing Digital Tools: Best Practices
Adopting digital tools for QCD management requires strategic planning and execution.
Here are some best practices to ensure a smooth implementation:
1. Assess Your Needs
Before selecting any digital tools, it is essential to assess your organization’s specific needs.
Identify the areas where improvements are necessary and then evaluate which tools can best address these requirements.
2. Involve All Stakeholders
Engage all the relevant stakeholders from different departments to gain a comprehensive understanding of their needs and challenges.
Their input will be crucial in selecting and implementing the most suitable tools.
3. Train Your Workforce
Ensure that your employees are adequately trained to use the new digital tools.
This may involve conducting training sessions and workshops to build their proficiency and comfort with the technology.
4. Monitor and Evaluate
Once the tools are implemented, continuously monitor their performance and evaluate their effectiveness.
Collect feedback from employees and make necessary adjustments to optimize their utility.
Conclusion
Digital tools offer a significant advantage in managing Quality, Cost, and Delivery efficiently.
By leveraging technologies such as Quality Management Systems, ERP, SCM, and data analytics, organizations can gain a competitive edge.
These tools not only help in maintaining high standards but also drive continuous improvement, ultimately leading to better customer satisfaction and business success.
It’s time to embrace digital solutions and elevate your QCD management to the next level.
資料ダウンロード
QCD調達購買管理クラウド「newji」は、調達購買部門で必要なQCD管理全てを備えた、現場特化型兼クラウド型の今世紀最高の購買管理システムとなります。
ユーザー登録
調達購買業務の効率化だけでなく、システムを導入することで、コスト削減や製品・資材のステータス可視化のほか、属人化していた購買情報の共有化による内部不正防止や統制にも役立ちます。
NEWJI DX
製造業に特化したデジタルトランスフォーメーション(DX)の実現を目指す請負開発型のコンサルティングサービスです。AI、iPaaS、および先端の技術を駆使して、製造プロセスの効率化、業務効率化、チームワーク強化、コスト削減、品質向上を実現します。このサービスは、製造業の課題を深く理解し、それに対する最適なデジタルソリューションを提供することで、企業が持続的な成長とイノベーションを達成できるようサポートします。
オンライン講座
製造業、主に購買・調達部門にお勤めの方々に向けた情報を配信しております。
新任の方やベテランの方、管理職を対象とした幅広いコンテンツをご用意しております。
お問い合わせ
コストダウンが利益に直結する術だと理解していても、なかなか前に進めることができない状況。そんな時は、newjiのコストダウン自動化機能で大きく利益貢献しよう!
(Β版非公開)