- お役立ち記事
- Cleanroom Design in Semiconductor Manufacturing Processes
Cleanroom Design in Semiconductor Manufacturing Processes
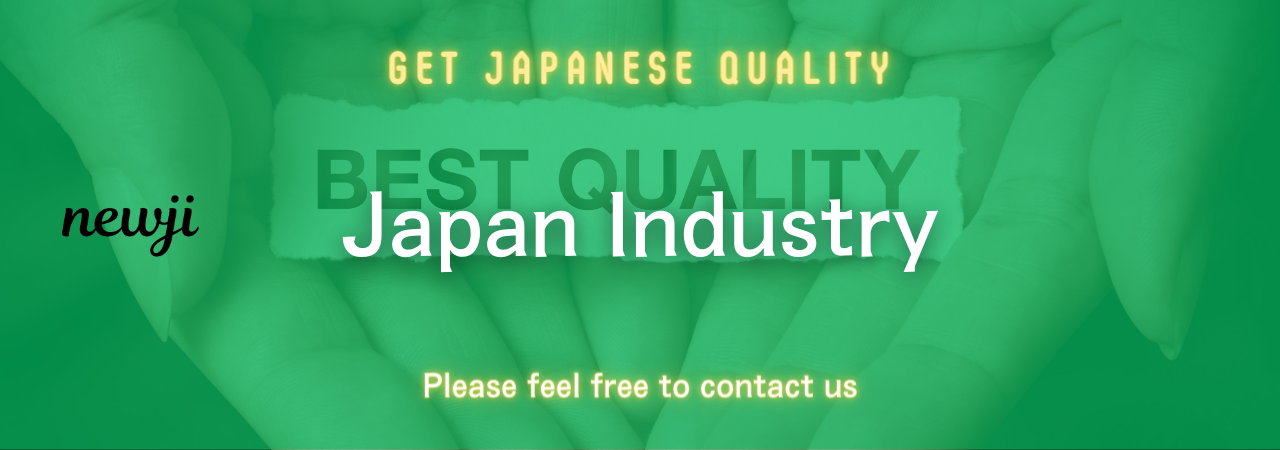
Cleanroom design plays a critical role in semiconductor manufacturing processes. These environments are essential to maintain the purity needed for creating advanced electronics. Contaminants such as dust, airborne microbes, and aerosol particles can wreak havoc on delicate semiconductor materials. By creating a meticulously controlled environment, we can ensure that high-quality semiconductor devices are produced efficiently.
目次
Understanding Cleanroom Classifications
Semiconductor manufacturing requires different levels of cleanliness depending on the specific processes involved. Cleanrooms are classified based on the number of particles permissible per cubic meter of air.
The most common classifications used are those defined by the International Organization for Standardization (ISO).
An ISO 1 cleanroom, for instance, allows no more than 10 particles per cubic meter, while an ISO 9 cleanroom allows up to 35,200,000 particles. Semiconductor production generally takes place in ISO 1 to ISO 5 cleanrooms.
Key Factors in Cleanroom Design
Several important factors should be considered when designing a cleanroom for semiconductor manufacturing. These include airflow, temperature, humidity, and construction materials.
Airflow Management
The cornerstone of cleanroom design is efficient airflow management. Airflow is carefully controlled to minimize contamination. Laminar flow systems are often used to ensure that air moves uniformly in one direction, usually downward. This helps to sweep away particles generated by manufacturing activities.
HEPA and ULPA filters are critical for maintaining air purity. HEPA filters eliminate 99.97% of particles larger than 0.3 micrometers, while ULPA filters can capture 99.999% of particles as small as 0.12 micrometers.
Temperature and Humidity Control
Temperature and humidity must be stringently controlled in semiconductor cleanrooms. Semiconductor devices are sensitive to environmental changes. Fluctuations in temperature can cause materials to expand or contract, impacting precision.
Typically, cleanrooms are maintained at temperatures between 20-22 degrees Celsius (68-72 degrees Fahrenheit) and relative humidity levels between 30-50%. Monitoring systems are often installed to continually track and adjust these parameters.
Construction Materials
Materials used in constructing cleanrooms must be non-shedding and easy to clean. Common materials include stainless steel, epoxy-coated surfaces, and specialized polymers.
These materials should also be resistant to corrosion and chemicals used during semiconductor manufacturing.
Importance of Contamination Control
Contamination control is imperative in semiconductor manufacturing. A single dust particle or microbe can cause defects, leading to significant financial losses. Therefore, contamination control strategies are integrated into every facet of cleanroom design and operation.
Use of Cleanroom Garments
Personnel working in cleanrooms must wear specialized garments to minimize the risk of contamination. These garments typically include coveralls, gloves, masks, and shoe covers. These items are designed to trap particles that might be shed by human skin or clothing.
Regular Cleaning and Maintenance
Cleanrooms require regular cleaning and maintenance to retain their high standards of cleanliness. Specialized cleaning protocols, such as using sterile wipes and cleaning agents, are employed. Additionally, equipment used in cleanrooms must also be regularly cleaned and serviced to prevent contamination.
Advancements in Cleanroom Technology
As semiconductor manufacturing evolves, so too does cleanroom technology. Advances in robotics, automation, and monitoring systems are enhancing the efficiency and effectiveness of cleanrooms.
Automated Systems
Automated robots are increasingly used in semiconductor cleanrooms. These robots handle delicate materials and perform repetitive tasks, reducing the possibility of contamination from human interaction. They can also work continuously without fatigue, enhancing productivity.
Real-Time Monitoring and Analytics
Modern cleanrooms are equipped with real-time monitoring systems. These systems can instantly detect any deviations in temperature, humidity, or particle count. Advanced analytics can predict potential contamination events, allowing for proactive measures to be taken.
Virtual Cleanroom Models
The use of virtual modeling and simulation tools is becoming more prevalent. These tools allow for the digital design and testing of cleanroom environments before construction begins.
This ensures that potential issues can be addressed in the design phase, saving time and resources.
Conclusion
The design of cleanrooms for semiconductor manufacturing is a complex but vital process. Ensuring the correct classification, implementing efficient airflow management, and choosing appropriate construction materials are critical to maintaining the purity required for semiconductor production.
As technology advances, new innovations continue to improve the effectiveness and efficiency of cleanroom environments. By staying abreast of these advancements and rigorously maintaining contamination control protocols, manufacturers can consistently produce high-quality semiconductor devices.
資料ダウンロード
QCD調達購買管理クラウド「newji」は、調達購買部門で必要なQCD管理全てを備えた、現場特化型兼クラウド型の今世紀最高の購買管理システムとなります。
ユーザー登録
調達購買業務の効率化だけでなく、システムを導入することで、コスト削減や製品・資材のステータス可視化のほか、属人化していた購買情報の共有化による内部不正防止や統制にも役立ちます。
NEWJI DX
製造業に特化したデジタルトランスフォーメーション(DX)の実現を目指す請負開発型のコンサルティングサービスです。AI、iPaaS、および先端の技術を駆使して、製造プロセスの効率化、業務効率化、チームワーク強化、コスト削減、品質向上を実現します。このサービスは、製造業の課題を深く理解し、それに対する最適なデジタルソリューションを提供することで、企業が持続的な成長とイノベーションを達成できるようサポートします。
オンライン講座
製造業、主に購買・調達部門にお勤めの方々に向けた情報を配信しております。
新任の方やベテランの方、管理職を対象とした幅広いコンテンツをご用意しております。
お問い合わせ
コストダウンが利益に直結する術だと理解していても、なかなか前に進めることができない状況。そんな時は、newjiのコストダウン自動化機能で大きく利益貢献しよう!
(Β版非公開)