- お役立ち記事
- The difference between Belt Grinding and Disc Grinding
The difference between Belt Grinding and Disc Grinding
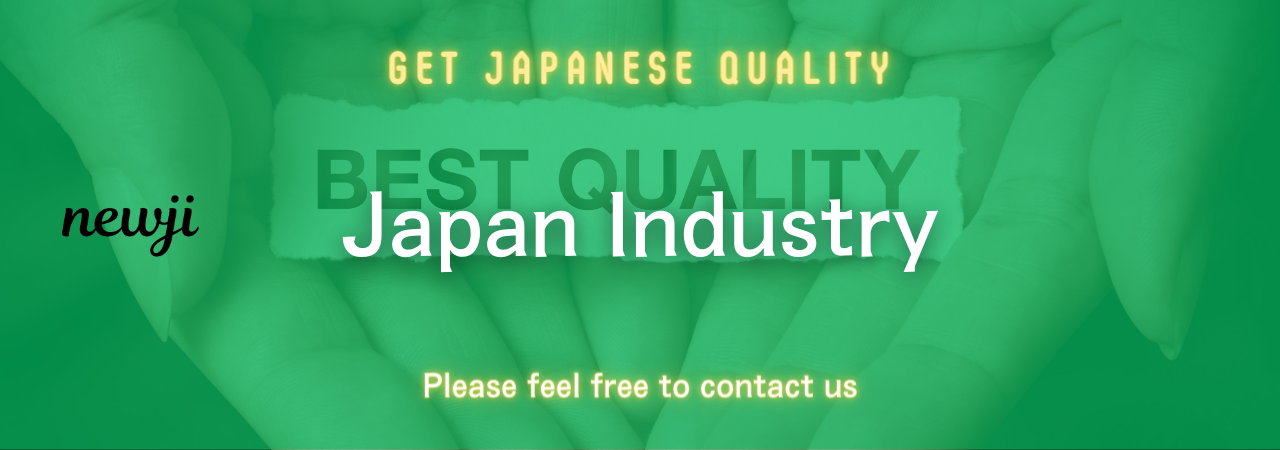
When it comes to precision grinding and efficient material removal, knowing the difference between belt grinding and disc grinding is crucial. Although these two grinding methods serve similar purposes, they each have unique features, applications, and benefits.
Understanding the nuances of these grinding techniques can help you choose the best method for your project.
Let’s delve into the details.
目次
What is Belt Grinding?
Belt grinding involves the use of abrasive belts to remove material from a workpiece’s surface.
The abrasive belt, which consists of a continuous loop of material, is spanned over two or more pulleys.
A motor powers these pulleys to rotate the belt at high speeds.
Belt grinding machines, also known as belt sanders, come in various configurations.
Some are bench-mounted, while others are handheld, portable devices.
The flexibility of the abrasive belt allows it to conform to complex shapes and contours, making belt grinding suitable for a wide range of applications.
Advantages of Belt Grinding
**Versatility**: Belt grinders can be used for various applications, including deburring, stock removal, and surface finishing.
They can grind, sand, and polish all kinds of materials such as metal, wood, and plastics.
**Speed and Efficiency**: The continuous movement of the abrasive belt allows for rapid material removal, making it ideal for tasks requiring substantial stock removal.
**Less Heat Generation**: Belt grinding tends to produce less heat compared to other grinding methods, reducing the risk of damaging the workpiece.
Common Applications of Belt Grinding
**Metalworking**: Belt grinders are extensively used in metal fabrication shops for deburring, grinding weld seams, and surface preparation.
They are also common in knife-making for shaping and sharpening blades.
**Woodworking**: Woodworkers use belt sanders for smoothing rough wooden surfaces and achieving a fine finish.
**Automotive and Aerospace Industries**: These sectors utilize belt grinding for precision surface finishing, ensuring components meet stringent quality standards.
What is Disc Grinding?
Disc grinding uses an abrasive disc to remove material from the surface of a workpiece.
The disc, which can vary in diameter, is mounted on the grinder’s spindle and rotates at high speeds.
Disc grinding equipment can be classified into two main types: horizontal and vertical spindle grinders.
Horizontal spindle grinders have the disc mounted parallel to the workpiece, while vertical spindle grinders have the disc mounted perpendicular to the workpiece.
Advantages of Disc Grinding
**High Precision**: Disc grinders offer exceptional precision and flatness, making them ideal for achieving tight tolerances and excellent surface finishes.
**Consistent Performance**: The rigid, fixed nature of the abrasive disc ensures consistent material removal and surface quality over time.
**Large Surface Area**: Disc grinders cover a larger surface area compared to other grinding methods, allowing for efficient grinding of large workpieces.
Common Applications of Disc Grinding
**Precision Manufacturing**: Disc grinding is widely used in industries where precision and surface finish are critical, such as aerospace, automotive, and electronics.
**Tool Sharpening**: Disc grinders are employed to sharpen cutting tools, ensuring they maintain their cutting performance over time.
**Surface Preparation**: Disc grinding is often used for surface preparation tasks, such as removing old coatings, rust, and contaminants from workpieces.
Key Differences Between Belt Grinding and Disc Grinding
While belt grinding and disc grinding share some similarities, there are key differences that set them apart.
Abrasive Surface
In belt grinding, the abrasive surface is a continuous looped belt, whereas in disc grinding, the abrasive surface is a flat disc.
This fundamental difference influences the grinding processes and the types of surfaces they can effectively work on.
Material Removal Rates
Belt grinding typically offers a faster material removal rate due to the continuous movement of the abrasive belt.
Disc grinding, on the other hand, provides more controlled material removal, making it suitable for applications requiring high precision.
Surface Finish
Disc grinding generally provides a smoother and more uniform surface finish compared to belt grinding.
The rigid nature of the abrasive disc results in consistent grinding, which is crucial for achieving fine finishes.
Application Flexibility
Belt grinding is more versatile, with applications ranging from shaping and deburring to finishing and polishing.
Disc grinding is more focused on achieving high precision and exceptional surface quality, making it ideal for specialized tasks.
Choosing the Right Grinding Method
Selecting the appropriate grinding method depends on the specific requirements of your project. If versatility and rapid material removal are your primary concerns, belt grinding might be the best choice.
Belt grinders can handle a wide range of tasks, from rough grinding to fine finishing.
On the other hand, if your project demands high precision and consistent surface finishes, disc grinding is the way to go.
Disc grinders excel in achieving tight tolerances and smooth surfaces, making them indispensable in precision manufacturing.
Consider the Material
The material you are working on also plays a crucial role in determining the suitable grinding method. Belt grinding works well with metals, wood, and plastics, while disc grinding is particularly effective for hard materials and precision components.
Safety Considerations
Both belt grinding and disc grinding can pose safety hazards if not used correctly. Always adhere to safety guidelines, such as wearing appropriate personal protective equipment (PPE), ensuring proper ventilation, and maintaining a clean workspace.
Regularly inspect and maintain your grinding equipment to prevent accidents and ensure optimal performance.
By understanding the key differences and applications of belt grinding and disc grinding, you can make informed decisions that enhance the efficiency and quality of your work. Whether you need to remove material quickly or achieve precise, smooth finishes, choosing the right grinding method will help you achieve your project goals with confidence.
資料ダウンロード
QCD調達購買管理クラウド「newji」は、調達購買部門で必要なQCD管理全てを備えた、現場特化型兼クラウド型の今世紀最高の購買管理システムとなります。
ユーザー登録
調達購買業務の効率化だけでなく、システムを導入することで、コスト削減や製品・資材のステータス可視化のほか、属人化していた購買情報の共有化による内部不正防止や統制にも役立ちます。
NEWJI DX
製造業に特化したデジタルトランスフォーメーション(DX)の実現を目指す請負開発型のコンサルティングサービスです。AI、iPaaS、および先端の技術を駆使して、製造プロセスの効率化、業務効率化、チームワーク強化、コスト削減、品質向上を実現します。このサービスは、製造業の課題を深く理解し、それに対する最適なデジタルソリューションを提供することで、企業が持続的な成長とイノベーションを達成できるようサポートします。
オンライン講座
製造業、主に購買・調達部門にお勤めの方々に向けた情報を配信しております。
新任の方やベテランの方、管理職を対象とした幅広いコンテンツをご用意しております。
お問い合わせ
コストダウンが利益に直結する術だと理解していても、なかなか前に進めることができない状況。そんな時は、newjiのコストダウン自動化機能で大きく利益貢献しよう!
(Β版非公開)