- お役立ち記事
- Color Management in Japanese Manufacturing: Precision and Perfection Redefined
Color Management in Japanese Manufacturing: Precision and Perfection Redefined
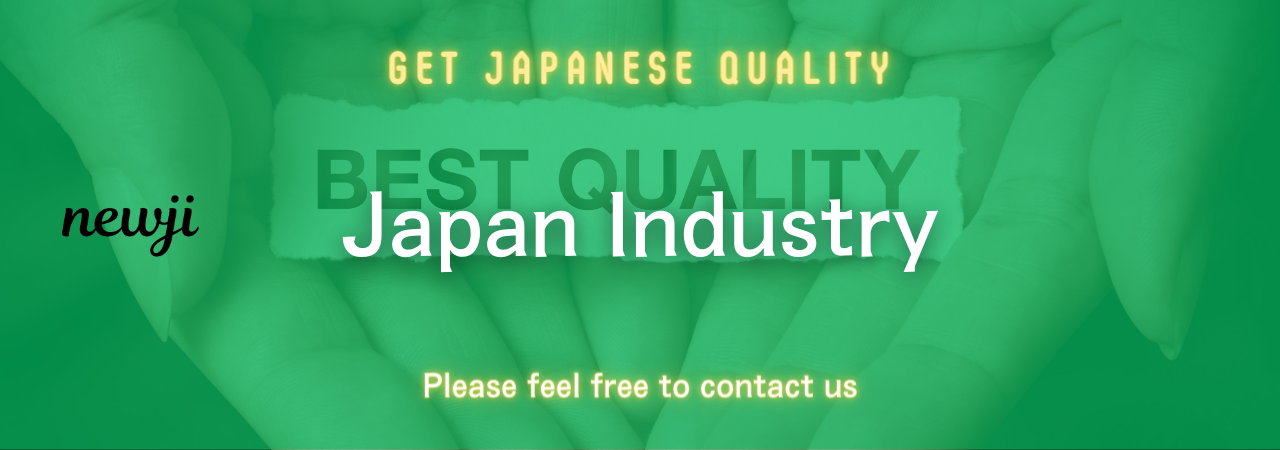
目次
Introduction
Color management in Japanese manufacturing symbolizes the nation’s relentless pursuit of precision and perfection.
The meticulous attention to detail and the intricate processes involved in ensuring consistent color delivery are the cornerstones of maintaining Japan’s reputation for high quality.
In this article, we will delve into the significance of color management within Japanese manufacturing, exploring its advantages, disadvantages, supplier negotiation techniques, market conditions, and best practices.
The Importance of Color Management in Manufacturing
Impact on Product Quality
Color plays a crucial role in the overall perception of product quality.
Inconsistent color can lead to a perception of poor quality and can negatively affect brand reputation.
In Japan, color management is not just about aesthetics; it is integrated deeply into quality control processes to ensure that each product meets stringent standards.
Consistency Across Production Batches
Maintaining color consistency across different production batches is vital.
In sectors like automotive, electronics, and textiles, color fidelity impacts not only the visual appeal but also the functional performance of products.
Japanese manufacturers utilize advanced color matching systems and spectrophotometers to achieve this consistency.
Brand Integrity
Consistent color management helps in preserving brand integrity.
Japanese manufacturers understand that a brand’s identity is closely tied to its visual presentation.
色uaranteeing precise colors across all products ensures that brand colors remain faithful from one product to another.
Advantages of Japanese Color Management Techniques
Advanced Technology and Equipment
Japanese manufacturing is known for its investment in advanced technology and equipment.
State-of-the-art color matching systems, high-precision spectrophotometers, and automated color correction systems enhance their color management capabilities.
Skilled Workforce
The expertise of the Japanese workforce forms the backbone of their color management strategy.
Extensive training programs ensure that workers understand the importance of color consistency and possess the skills necessary to achieve it.
Supplier Collaboration
Japanese manufacturers often work closely with their suppliers to ensure color quality.
Collaboration on material selection, colorants, and dyes ensures that the entire supply chain maintains a high standard of color fidelity.
Disadvantages and Challenges
High Costs
Implementing advanced color management systems can be costly.
The initial investment in sophisticated equipment and ongoing maintenance expenses can be significant.
However, Japanese manufacturers often view these costs as necessary investments in quality.
Complexity and Time Consumption
Color management processes can be complex and time-consuming.
Achieving the perfect color match often requires multiple iterations and adjustments, which can slow down production timelines.
Environmental Concerns
The use of certain dyes and colorants may pose environmental challenges.
The Japanese manufacturing sector is constantly exploring sustainable and environmentally-friendly alternatives to minimize their ecological footprint.
Supplier Negotiation Techniques
Establishing Clear Specifications
One of the first steps in effective supplier negotiation is establishing clear and precise color specifications.
Utilizing color standards such as Pantone or RAL ensures that both parties have a common understanding of the desired color.
Regular Communication
Frequent and transparent communication with suppliers helps in quickly addressing any color discrepancies.
Japanese manufacturers often conduct regular meetings and audits to ensure alignment on color requirements.
Performance Metrics
Setting performance metrics for suppliers related to color consistency helps in maintaining high standards.
Key Performance Indicators (KPIs) such as color deviation tolerances and defect rates are commonly used in Japanese manufacturing.
Market Conditions
Demand for Customization
There is a growing demand for customized products in markets worldwide.
This trend necessitates precise and flexible color management systems to cater to varying customer requirements.
Technological Advancements
Continual advancements in color science and technology are driving the market forward.
With innovations in digital color management systems, Japanese manufacturers are staying ahead of the curve to meet market expectations.
Global Integration
As Japanese manufacturers integrate more globally, maintaining color consistency across different geographical locations becomes paramount.
Adopting global color standards and leveraging digital communication tools helps in overcoming these challenges.
Best Practices in Japanese Color Management
Utilizing Color Management Software
Utilizing advanced color management software is a best practice in Japanese manufacturing.
Software solutions aid in color matching, formulation, and quality control, ensuring that color consistency is maintained throughout the production process.
Implementing Standard Operating Procedures (SOPs)
Standard Operating Procedures for color management outline the steps and protocols to be followed, ensuring consistency and reducing the likelihood of errors.
SOPs are integral to maintaining high standards in Japanese manufacturing.
Employee Training and Development
Investing in continuous training and development programs for employees ensures that they remain adept at handling the latest color management technologies and techniques.
Skilled employees are better equipped to maintain color quality and address any issues promptly.
Conclusion
Color management in Japanese manufacturing is a testament to the nation’s commitment to precision and perfection.
By leveraging advanced technology, skilled workforce, and robust supplier collaboration, Japanese manufacturers are able to maintain high standards of color consistency and quality.
Despite challenges, their dedication to excellence ensures that products meet both aesthetic and functional requirements.
Adopting best practices such as utilizing color management software, implementing SOPs, and investing in employee training further solidifies their position as leaders in color management. As market demands evolve, Japanese manufacturers continue to innovate, setting benchmarks for the industry in maintaining color fidelity and brand integrity.
資料ダウンロード
QCD調達購買管理クラウド「newji」は、調達購買部門で必要なQCD管理全てを備えた、現場特化型兼クラウド型の今世紀最高の購買管理システムとなります。
ユーザー登録
調達購買業務の効率化だけでなく、システムを導入することで、コスト削減や製品・資材のステータス可視化のほか、属人化していた購買情報の共有化による内部不正防止や統制にも役立ちます。
NEWJI DX
製造業に特化したデジタルトランスフォーメーション(DX)の実現を目指す請負開発型のコンサルティングサービスです。AI、iPaaS、および先端の技術を駆使して、製造プロセスの効率化、業務効率化、チームワーク強化、コスト削減、品質向上を実現します。このサービスは、製造業の課題を深く理解し、それに対する最適なデジタルソリューションを提供することで、企業が持続的な成長とイノベーションを達成できるようサポートします。
オンライン講座
製造業、主に購買・調達部門にお勤めの方々に向けた情報を配信しております。
新任の方やベテランの方、管理職を対象とした幅広いコンテンツをご用意しております。
お問い合わせ
コストダウンが利益に直結する術だと理解していても、なかなか前に進めることができない状況。そんな時は、newjiのコストダウン自動化機能で大きく利益貢献しよう!
(Β版非公開)