- お役立ち記事
- Selecting the Right Machines and Tools for High-Speed Processing
Selecting the Right Machines and Tools for High-Speed Processing
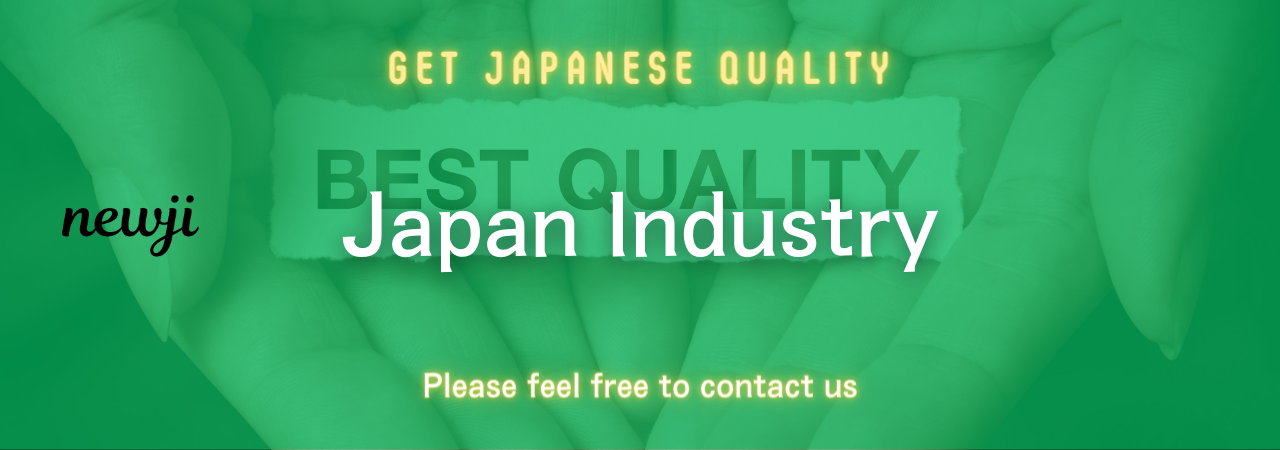
High-speed processing is a critical factor for many industries today. From automotive to aerospace, efficient and precise manufacturing is essential to meet production demands and maintain quality. Selecting the right machines and tools for high-speed processing can significantly impact the productivity, quality, and profitability of your operations.
目次
Understanding High-Speed Processing
High-speed processing involves operating machines at higher speeds to increase productivity without compromising on quality. This method is often used in industries where time efficiency and mass production are crucial.
To achieve high-speed processing, specific machines and tools must be designed to withstand the increased stress and heat generated during the process.
Importance of High-Speed Processing
High-speed processing offers several advantages, such as:
– **Increased Productivity:** By reducing cycle times, manufacturers can produce more parts in less time.
– **Enhanced Surface Finish:** High-speed processing often results in a superior surface finish, reducing the need for secondary operations.
– **Cost Efficiency:** Shorter production times and less tool wear translate to lower overall costs.
– **Flexibility:** High-speed machines often have sophisticated control systems that allow for quick adjustments and setups, accommodating a variety of tasks.
Choosing the Right Machines
Selecting the right machines is the first step toward efficient high-speed processing. Here are some factors to consider:
1. Machine Rigidity
For high-speed operations, machine rigidity is crucial. Machines with robust frameworks and high stiffness minimize vibrations and ensure precision. Look for machines with heavy-duty castings and well-designed structures.
2. Spindle Speed and Power
High-speed machining requires spindles capable of operating at high RPMs (Revolutions Per Minute). Evaluate the maximum spindle speed and the power rating of the machine. Machines with higher spindle speeds can reduce cycle times and improve cutting conditions.
3. Control Systems
Advanced CNC (Computer Numerical Control) systems are essential for high-speed processing. These systems should offer high processing speeds, accuracy, and easy programming. Modern control systems also provide real-time monitoring and diagnostics, enhancing machine performance.
4. Axis Acceleration
The ability of a machine to accelerate and decelerate swiftly is critical for high-speed processing. Machines with higher axis acceleration rates can achieve faster cycle times and provide better accuracy in complex geometries.
5. Cooling and Lubrication
High-speed processing generates a significant amount of heat. Efficient cooling and lubrication systems are necessary to maintain tool life and workpiece quality. Look for machines equipped with advanced cooling techniques such as through-tool cooling systems.
Selecting the Right Tools
High-speed processing demands specific tools designed to operate at high speeds while maintaining precision and durability. Consider the following when selecting tools:
1. Tool Material
Choose tools made from materials that can withstand the high temperatures and stresses associated with high-speed processing. Carbide, ceramic, and CBN (Cubic Boron Nitride) tools are common choices due to their hardness and heat resistance.
2. Tool Geometry
Tool geometry plays a vital role in high-speed machining. Optimized cutting angles and tool shapes can reduce cutting forces, minimize tool wear, and enhance surface finish. Tools with advanced coatings can further improve performance by reducing friction and extending tool life.
3. Tool Holding Systems
Accurate and secure tool holding is essential for high-speed processing. High-precision collets, shrink-fit holders, and hydraulic chucks provide better grip and minimize tool runout, ensuring precise machining.
4. Balanced Tools
Balanced tools and holders are necessary to prevent vibrations at high speeds. Unbalanced tools can lead to poor surface finishes and reduced tool life. Consider investing in dynamic balancing equipment to ensure optimal tool performance.
5. Tool Life Management
Implementing a tool life management system can help monitor tool wear and predict tool replacement needs. This proactive approach minimizes machine downtime and ensures consistent quality.
Integrating Machines and Tools: Best Practices
To achieve the best results in high-speed processing, it’s essential to seamlessly integrate machines and tools. Here are some best practices:
1. Collaborative Planning
Work closely with tool and machine manufacturers to design a system tailored for your specific needs. Collaborative planning ensures compatibility and optimizes performance.
2. Regular Maintenance
Perform regular maintenance on both machines and tools. Regular inspections, cleaning, and calibration help maintain peak performance and prevent unexpected breakdowns.
3. Training and Skill Development
Invest in training programs for your operators and engineers. Skilled personnel can maximize the potential of high-speed machines and tools, leading to better productivity and quality.
4. Monitoring and Feedback
Use monitoring systems to gather data on machine and tool performance. Analyze this data to identify improvements and troubleshoot issues promptly. Feedback from operators can also provide valuable insights.
Conclusion
Selecting the right machines and tools for high-speed processing is a multi-faceted decision that can significantly influence the efficiency of your operations.
By considering factors such as machine rigidity, spindle speed, control systems, and tool material, you can create an optimized environment for high-speed processing.
Implementing best practices in maintenance, training, and monitoring further ensures sustained productivity and quality.
With the right machines and tools, high-speed processing can drive your business towards greater success.
資料ダウンロード
QCD調達購買管理クラウド「newji」は、調達購買部門で必要なQCD管理全てを備えた、現場特化型兼クラウド型の今世紀最高の購買管理システムとなります。
ユーザー登録
調達購買業務の効率化だけでなく、システムを導入することで、コスト削減や製品・資材のステータス可視化のほか、属人化していた購買情報の共有化による内部不正防止や統制にも役立ちます。
NEWJI DX
製造業に特化したデジタルトランスフォーメーション(DX)の実現を目指す請負開発型のコンサルティングサービスです。AI、iPaaS、および先端の技術を駆使して、製造プロセスの効率化、業務効率化、チームワーク強化、コスト削減、品質向上を実現します。このサービスは、製造業の課題を深く理解し、それに対する最適なデジタルソリューションを提供することで、企業が持続的な成長とイノベーションを達成できるようサポートします。
オンライン講座
製造業、主に購買・調達部門にお勤めの方々に向けた情報を配信しております。
新任の方やベテランの方、管理職を対象とした幅広いコンテンツをご用意しております。
お問い合わせ
コストダウンが利益に直結する術だと理解していても、なかなか前に進めることができない状況。そんな時は、newjiのコストダウン自動化機能で大きく利益貢献しよう!
(Β版非公開)