- お役立ち記事
- Manufacturing Process of Electric Ice Shavers and Precision Blade Adjustment
Manufacturing Process of Electric Ice Shavers and Precision Blade Adjustment
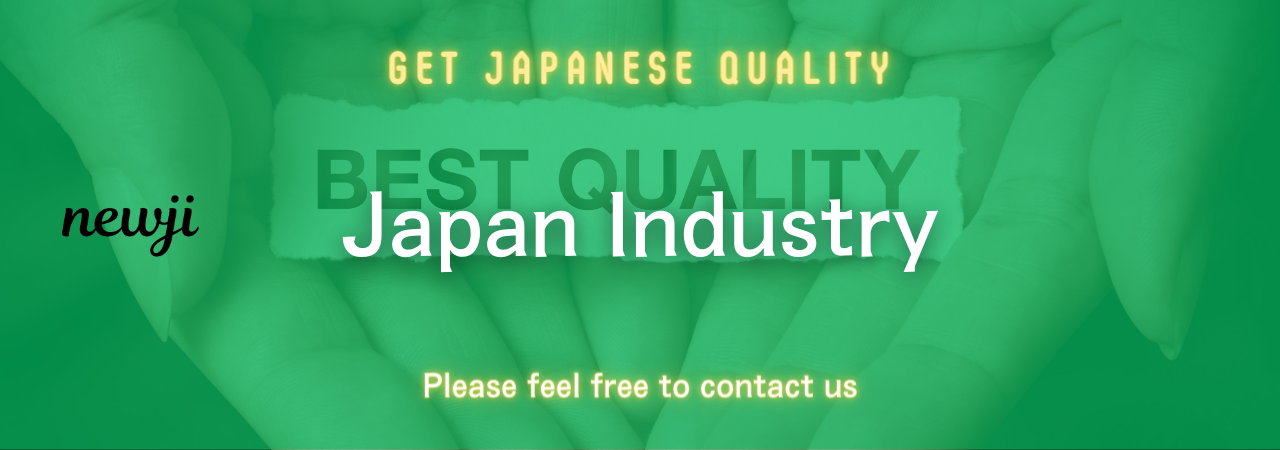
Electric ice shavers have become essential tools for making refreshing frozen treats.
Whether you’re running a snow cone stand or enjoying icy snacks at home, understanding the manufacturing process of these machines can be fascinating and beneficial.
The precision blade adjustment is one of the most critical aspects of ensuring a high-quality shave.
In this article, we’ll explore the manufacturing process of electric ice shavers and dive into the details of how precision blade adjustment plays a significant role.
目次
Raw Materials and Initial Preparation
The manufacturing process of electric ice shavers begins with the selection of raw materials.
High-quality stainless steel is commonly used for the blades due to its durability and resistance to rust.
The body of the ice shaver can be made from a combination of materials such as plastic, aluminum, or stainless steel.
Once the raw materials are selected, they undergo a series of initial preparations.
Steel sheets are cut and molded into the desired shape to form the blades.
The plastic or aluminum components are molded through an injection molding process to create the body parts of the ice shaver.
Assembling the Machine
After the individual components are prepared, the assembly process begins.
First, the motor, which is the heart of the electric ice shaver, is mounted onto a base.
This motor drives the blades and ensures efficient ice shaving.
Next, the blades are attached to the motor shaft with precision.
This step involves careful alignment to ensure that the blades rotate perfectly and efficiently shave the ice.
The body parts are then assembled around the motor and blades.
These parts are fastened together using screws and bolts.
The design must be ergonomic to ensure ease of use, safety, and efficient operation.
Precision Blade Adjustment
One of the most crucial aspects of manufacturing electric ice shavers is the precision adjustment of the blades.
This ensures that the ice is shaved to the correct consistency and texture, making the final product perfect for use.
Blade Angle and Sharpness
The angle of the blade is adjusted to achieve the ideal contact with the ice.
If the angle is too steep, the blade may crush the ice instead of shaving it.
If it’s too shallow, the blade might not cut efficiently.
High-precision tools are used to calibrate the blade angle accurately.
Sharpness is another vital factor.
Blades are sharpened to the finest edge to ensure they can cut through ice smoothly.
The sharpness is tested through various methods, including cutting through test ice blocks and measuring the uniformity of the shaved ice.
Testing and Quality Assurance
Once the precision blade adjustment is complete, the entire unit undergoes a series of tests.
Quality assurance teams test the ice shavers under different conditions to ensure durability and performance.
They check for any mechanical issues, blade efficiency, and motor functionality.
Ice shavers are also tested for safety features, such as overload protection and automatic shut-off mechanisms.
These tests are essential for ensuring the product’s safety during use and maintaining customer satisfaction.
Final Assembly and Finishing
After successful testing, the electric ice shavers are ready for final assembly.
The components are cleaned and polished to remove any manufacturing residues.
The final assembly involves attaching any remaining parts, such as the ice hopper, holding container, and safety guards.
The exterior of the ice shaver may be painted or coated for added durability and aesthetics.
Logos and product information are then printed or stamped on the body.
This provides users with crucial information such as model numbers and operating instructions.
Packing and Distribution
Once the ice shavers are fully assembled and finished, they are packed for distribution.
Packaging involves careful consideration to prevent any damage during transit.
Protective packaging materials such as foam inserts and bubble wrap are used to safeguard the product.
The packed ice shavers are then labeled and categorized for distribution.
They are shipped to wholesalers, retailers, or directly to customers depending on the distribution channels.
Conclusion
Understanding the manufacturing process of electric ice shavers and the importance of precision blade adjustments can provide a deeper appreciation for these handy devices.
Each step in the process, from raw material selection to the final assembly, plays a crucial role in producing a high-quality electric ice shaver.
Next time you enjoy a snow cone or a refreshing shaved ice treat, you’ll know the intricate details and craftsmanship that went into making that possible.
資料ダウンロード
QCD調達購買管理クラウド「newji」は、調達購買部門で必要なQCD管理全てを備えた、現場特化型兼クラウド型の今世紀最高の購買管理システムとなります。
ユーザー登録
調達購買業務の効率化だけでなく、システムを導入することで、コスト削減や製品・資材のステータス可視化のほか、属人化していた購買情報の共有化による内部不正防止や統制にも役立ちます。
NEWJI DX
製造業に特化したデジタルトランスフォーメーション(DX)の実現を目指す請負開発型のコンサルティングサービスです。AI、iPaaS、および先端の技術を駆使して、製造プロセスの効率化、業務効率化、チームワーク強化、コスト削減、品質向上を実現します。このサービスは、製造業の課題を深く理解し、それに対する最適なデジタルソリューションを提供することで、企業が持続的な成長とイノベーションを達成できるようサポートします。
オンライン講座
製造業、主に購買・調達部門にお勤めの方々に向けた情報を配信しております。
新任の方やベテランの方、管理職を対象とした幅広いコンテンツをご用意しております。
お問い合わせ
コストダウンが利益に直結する術だと理解していても、なかなか前に進めることができない状況。そんな時は、newjiのコストダウン自動化機能で大きく利益貢献しよう!
(Β版非公開)