- お役立ち記事
- The difference between Gas Cutting and Plasma Cutting
月間76,176名の
製造業ご担当者様が閲覧しています*
*2025年3月31日現在のGoogle Analyticsのデータより
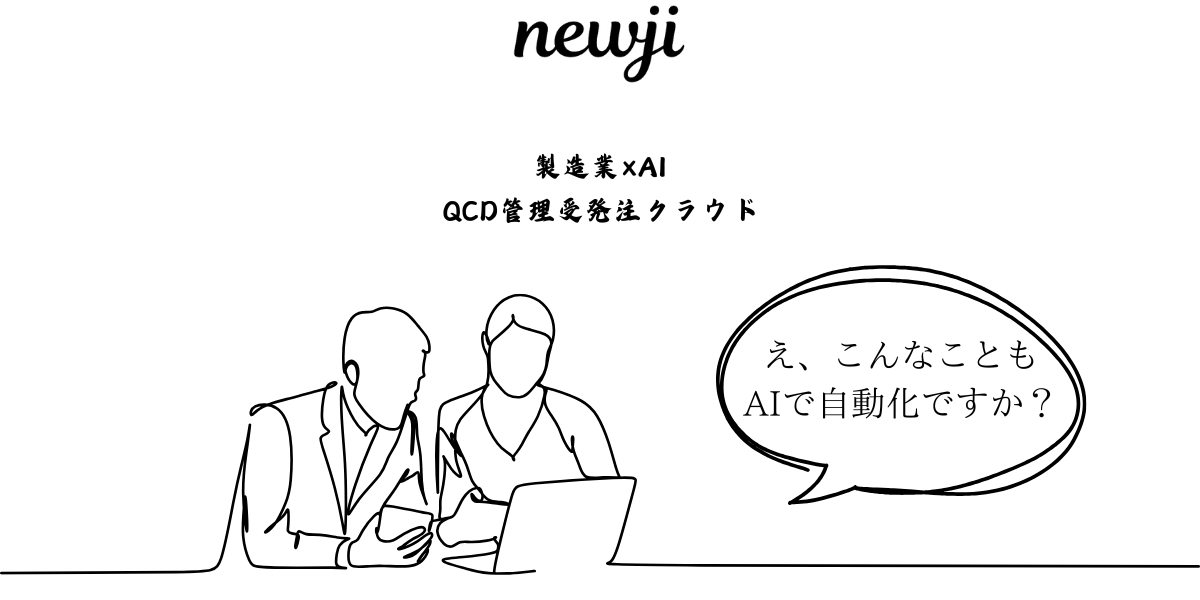
The difference between Gas Cutting and Plasma Cutting
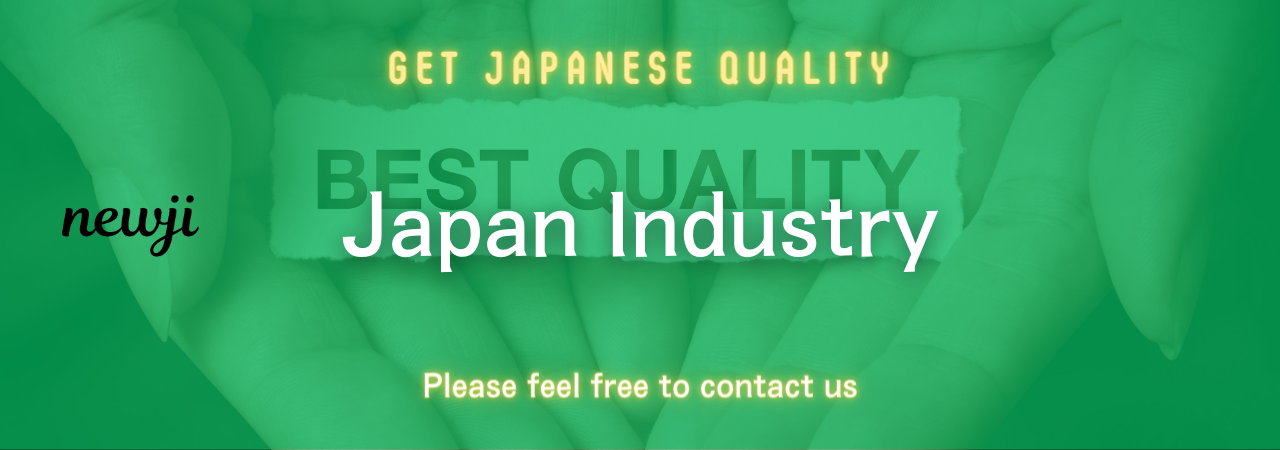
Metal cutting plays an essential role in many industrial applications, from automotive manufacturing to shipbuilding.
Two common methods used in metal cutting are gas cutting and plasma cutting.
While both techniques are effective, they have distinct differences that make them suitable for various applications.
In this article, we’ll explore the differences between gas cutting and plasma cutting, their advantages and disadvantages, and their typical uses.
目次
What is Gas Cutting?
Gas cutting, also known as oxy-fuel cutting, uses a combination of oxygen and fuel gases to cut through metal.
Commonly used fuel gases include acetylene, propane, and natural gas.
The process involves heating the metal to its ignition temperature and then introducing a high-pressure stream of oxygen to burn through the material.
How It Works
The gas cutting process begins by heating the metal surface with a flame composed of oxygen and fuel gas.
Once the metal reaches its ignition temperature, a jet of pure oxygen is directed at the heated area.
The oxygen reacts with the metal, forming iron oxides (commonly known as slag), which are then blown away by the force of the oxygen jet, creating a cut.
Advantages of Gas Cutting
– Cost-Effective: Gas cutting equipment is relatively inexpensive compared to other cutting technologies.
– Versatility: It can cut through a variety of metals, including mild steel, stainless steel, and cast iron.
– Portability: Gas cutting equipment is portable and can be used in various locations, making it ideal for fieldwork and repairs.
Disadvantages of Gas Cutting
– Limited Material Thickness: It is less effective for cutting thicker materials.
– Slower Cutting Speed: Gas cutting is generally slower than other cutting methods.
– Safety Concerns: The use of open flames and combustible gases poses safety risks, such as explosions and fire hazards.
What is Plasma Cutting?
Plasma cutting uses an electrically conductive gas to transfer energy from an electrical power source to a conductive material, effectively cutting through it.
The process is suitable for cutting various metals, including stainless steel, aluminum, and copper.
How It Works
The plasma cutting process starts with the creation of a plasma arc.
An electrical arc is generated between an electrode (usually made of tungsten) and the material being cut.
This arc ionizes the gas, creating a plasma jet.
The plasma jet reaches extremely high temperatures, which melts the material and blows it away, resulting in a clean cut.
Advantages of Plasma Cutting
– High Cutting Speed: Plasma cutting is significantly faster than gas cutting, especially for thinner materials.
– Precision: It offers high precision and a clean cut, reducing the need for additional finishing processes.
– Versatility: Plasma cutting can handle a wide range of conductive materials and thicknesses.
Disadvantages of Plasma Cutting
– Higher Initial Investment: Plasma cutting equipment is usually more expensive than gas cutting equipment.
– Limited Portability: Plasma cutters are generally less portable due to the need for an electrical power source and more complex machinery.
– Limited Effectiveness on Thick Materials: While plasma cutting is effective for various thicknesses, it struggles with very thick metals compared to gas cutting.
Typical Uses and Applications
Both gas cutting and plasma cutting have their specific applications based on their unique advantages and limitations.
Understanding these can help industries choose the appropriate method for their needs.
Gas Cutting Applications
– Construction Sites: Gas cutting is widely used in construction for cutting beams and other structural components.
– Metal Fabrication Shops: It’s useful for cutting shapes and profiles in metal fabrication.
– Repair and Maintenance: Due to its portability, gas cutting is ideal for on-site repairs and maintenance tasks.
Plasma Cutting Applications
– Automotive Industry: Plasma cutting is used for cutting and shaping various automotive parts.
– Metal Art and Signage: Its precision makes it suitable for intricate designs and detailed metalwork.
– Manufacturing: Plasma cutting is extensively used in manufacturing processes for producing parts and components efficiently.
Choosing the Right Cutting Method
Selecting the appropriate cutting method depends on various factors, including the type of material, thickness, cut quality requirements, and available budget.
Here are some considerations to help make the decision easier.
Material Type
If you’re working primarily with ferrous metals like steel or iron, gas cutting may be more suitable.
However, if you need to cut a variety of metals, including non-ferrous materials like aluminum and copper, plasma cutting is the better option.
Material Thickness
For thicker materials, gas cutting can be more effective.
On the other hand, plasma cutting excels at cutting thin to medium-thick materials quickly and accurately.
Budget
Gas cutting equipment is generally less expensive upfront, making it a cost-effective choice for small shops or fieldwork.
Plasma cutting requires a higher initial investment but offers long-term cost savings due to its speed and precision.
Portability
If you need to move your equipment frequently or perform on-site repairs, gas cutting is more portable and convenient.
Plasma cutting, while less portable, can be an excellent choice for stationary workshops with constant electrical access.
Conclusion
Both gas cutting and plasma cutting have their unique advantages and disadvantages, making them suitable for different applications.
Gas cutting is cost-effective, versatile, and portable, making it a practical choice for many fieldwork and repair scenarios.
Plasma cutting, with its high speed, precision, and versatility, is ideal for manufacturing, automotive, and detailed metalwork applications.
Understanding the differences between these two cutting methods can help you make informed decisions for your specific needs.
By considering factors such as material type, thickness, budget, and portability, you can choose the best cutting method for your projects.
資料ダウンロード
QCD管理受発注クラウド「newji」は、受発注部門で必要なQCD管理全てを備えた、現場特化型兼クラウド型の今世紀最高の受発注管理システムとなります。
ユーザー登録
受発注業務の効率化だけでなく、システムを導入することで、コスト削減や製品・資材のステータス可視化のほか、属人化していた受発注情報の共有化による内部不正防止や統制にも役立ちます。
NEWJI DX
製造業に特化したデジタルトランスフォーメーション(DX)の実現を目指す請負開発型のコンサルティングサービスです。AI、iPaaS、および先端の技術を駆使して、製造プロセスの効率化、業務効率化、チームワーク強化、コスト削減、品質向上を実現します。このサービスは、製造業の課題を深く理解し、それに対する最適なデジタルソリューションを提供することで、企業が持続的な成長とイノベーションを達成できるようサポートします。
製造業ニュース解説
製造業、主に購買・調達部門にお勤めの方々に向けた情報を配信しております。
新任の方やベテランの方、管理職を対象とした幅広いコンテンツをご用意しております。
お問い合わせ
コストダウンが利益に直結する術だと理解していても、なかなか前に進めることができない状況。そんな時は、newjiのコストダウン自動化機能で大きく利益貢献しよう!
(β版非公開)