- お役立ち記事
- Revolutionizing Japanese Manufacturing: The Power of Physical Vapor Deposition Techniques
Revolutionizing Japanese Manufacturing: The Power of Physical Vapor Deposition Techniques
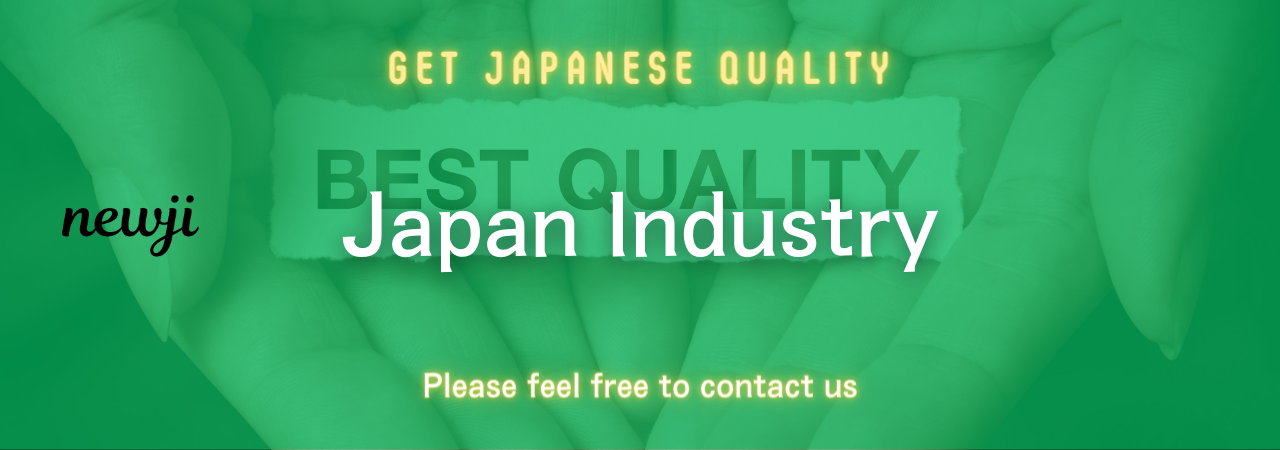
目次
Introduction to Physical Vapor Deposition (PVD)
Physical Vapor Deposition (PVD) is a prominent coating technique used in the manufacturing industry to produce thin films and coatings with high precision and exceptional quality.
This technology has gained significant traction due to its ability to enhance surface properties such as hardness, wear resistance, and corrosion resistance.
In the context of Japanese manufacturing, PVD techniques have revolutionized the production processes, offering an array of advantages that align perfectly with the core principles of efficiency, quality, and innovation.
The Dynamics of Japanese Manufacturing
Japan is renowned for its meticulous approach to manufacturing, emphasizing continuous improvement (kaizen), precision, and a deep commitment to quality.
The integration of PVD technology into Japanese manufacturing processes exemplifies these values, delivering unparalleled enhancements to the final products.
Japanese companies have embraced various PVD methods, including sputtering, evaporation, and arc deposition, to achieve superior product finishes.
Efficiency and Quality Control
One of the primary reasons for the extensive use of PVD in Japanese manufacturing is its efficiency.
PVD techniques allow for the precise control of coating thickness and uniformity, ensuring that every component meets stringent quality standards.
This level of control is crucial in industries such as electronics, automotive, and aerospace, where even the smallest deviation can lead to significant performance issues.
Furthermore, PVD processes are often conducted in vacuum environments, reducing the risk of contamination and ensuring the purity of the coatings.
This aligns perfectly with the Japanese emphasis on cleanliness and precision in manufacturing.
Material Versatility and Adaptability
Japanese manufacturing thrives on adaptability and the ability to work with a diverse range of materials.
PVD techniques are versatile and can be applied to various substrates, including metals, ceramics, and plastics.
This flexibility allows Japanese manufacturers to innovate and develop new products with enhanced properties, keeping them at the forefront of global competition.
Advantages of PVD Techniques
Enhanced Surface Properties
PVD coatings significantly enhance surface properties such as hardness, wear resistance, and corrosion resistance.
These improvements are vital in industries where components are subjected to extreme conditions, such as automotive and aerospace.
Japanese suppliers have mastered the art of achieving these enhancements, providing products that stand the test of time and perform exceptionally under stress.
Environmental Benefits
In addition to performance improvements, PVD techniques are environmentally friendly compared to traditional coating methods.
They do not produce hazardous by-products, and the processes are typically more energy-efficient.
Japanese manufacturers, known for their commitment to sustainability, have adopted PVD to reduce their environmental footprint and contribute to a greener future.
Cost-Effectiveness
While the initial investment in PVD equipment may be high, the long-term benefits in terms of product durability and reduced maintenance costs far outweigh the initial expenses.
Japanese companies have leveraged this cost-effectiveness to maintain competitive pricing while delivering superior quality products.
Challenges and Disadvantages
High Initial Investment
One of the primary disadvantages of PVD techniques is the high initial investment required for equipment and setup.
This can be a significant barrier for small and medium-sized enterprises (SMEs) looking to adopt the technology.
However, Japanese suppliers, supported by government initiatives and collaboration with larger corporations, have found ways to mitigate these costs and make PVD more accessible.
Complex Process Control
PVD processes require precise control and monitoring to achieve the desired coating properties.
This complexity can be a challenge, especially for companies with limited technical expertise.
However, Japanese companies have invested heavily in training and developing skilled technicians, ensuring that they can effectively manage and optimize PVD processes.
Supplier Negotiation Techniques
Understanding Supplier Capabilities
When dealing with Japanese suppliers, it is crucial to have a deep understanding of their capabilities, especially in PVD applications.
Conduct thorough research and engage in detailed discussions to gauge their expertise and previous projects.
Japanese suppliers value long-term relationships, so demonstrating a keen interest in their capabilities can foster trust and cooperation.
Value of Clear Communication
Clear and transparent communication is essential when negotiating with Japanese suppliers.
Ensure that all technical specifications, quality expectations, and delivery timelines are precisely conveyed.
Japanese suppliers appreciate detailed and comprehensive information, as it aligns with their meticulous approach to manufacturing.
Leveraging Long-Term Relationships
Building long-term relationships with Japanese suppliers is a cornerstone of successful negotiations.
Japanese business culture emphasizes trust and loyalty, and suppliers are more likely to offer favorable terms and prioritize your orders if they see a commitment to a long-term partnership.
Invest time in relationship-building activities, such as regular visits and collaborative projects.
Market Conditions and PVD Adoption
Global Demand for High-Performance Coatings
The global demand for high-performance coatings is on the rise, driven by advancements in industries such as electronics, automotive, and aerospace.
PVD technology plays a pivotal role in meeting this demand, and Japanese manufacturers are well-positioned to capitalize on this trend.
Their expertise in PVD techniques allows them to produce coatings that meet stringent international standards and cater to a global clientele.
Technological Advancements
Technological advancements in PVD equipment and processes have further boosted the adoption of this technique.
Japanese companies are at the forefront of these advancements, continually investing in research and development to push the boundaries of what PVD can achieve.
This commitment to innovation ensures that they remain competitive in the global market.
Best Practices for PVD Implementation
Investing in Advanced Equipment
One of the best practices for implementing PVD techniques is investing in state-of-the-art equipment.
Japanese manufacturers understand the importance of using advanced machinery to achieve the highest-quality coatings.
Partnering with suppliers who have access to top-tier PVD equipment can significantly enhance the performance of your products.
Skilled Workforce Development
Developing a skilled workforce is crucial for the successful implementation of PVD techniques.
Japanese companies prioritize training and development programs to ensure that their technicians and engineers are proficient in handling PVD processes.
By investing in workforce development, you can ensure consistent quality and optimize the benefits of PVD technology.
Continuous Quality Improvement
Japanese manufacturing is synonymous with continuous improvement, and this principle extends to PVD implementation.
Regularly monitor and evaluate the performance of PVD processes, and seek opportunities for improvement.
Engage in collaborative efforts with suppliers to identify areas where enhancements can be made, ensuring that your products consistently meet the highest standards.
The Future of PVD in Japanese Manufacturing
The future of PVD in Japanese manufacturing looks promising, with ongoing advancements and increasing adoption across various industries.
As global demand for high-performance, durable, and environmentally friendly coatings continues to grow, Japanese manufacturers are well-equipped to meet these needs through their expertise in PVD techniques.
By leveraging the advantages of PVD and adhering to best practices, companies can achieve remarkable product enhancements and maintain a competitive edge in the global market.
In conclusion, Physical Vapor Deposition techniques have revolutionized Japanese manufacturing by offering unparalleled efficiency, quality, and versatility.
Despite the challenges of high initial investments and complex processes, the long-term benefits make PVD a worthwhile endeavor.
By understanding supplier capabilities, fostering clear communication, and building long-term relationships, companies can effectively navigate the Japanese market and harness the full potential of PVD technology.
As market conditions and technological advancements continue to evolve, embracing best practices for PVD implementation will ensure that Japanese manufacturers remain at the forefront of innovation and excellence.
資料ダウンロード
QCD調達購買管理クラウド「newji」は、調達購買部門で必要なQCD管理全てを備えた、現場特化型兼クラウド型の今世紀最高の購買管理システムとなります。
ユーザー登録
調達購買業務の効率化だけでなく、システムを導入することで、コスト削減や製品・資材のステータス可視化のほか、属人化していた購買情報の共有化による内部不正防止や統制にも役立ちます。
NEWJI DX
製造業に特化したデジタルトランスフォーメーション(DX)の実現を目指す請負開発型のコンサルティングサービスです。AI、iPaaS、および先端の技術を駆使して、製造プロセスの効率化、業務効率化、チームワーク強化、コスト削減、品質向上を実現します。このサービスは、製造業の課題を深く理解し、それに対する最適なデジタルソリューションを提供することで、企業が持続的な成長とイノベーションを達成できるようサポートします。
オンライン講座
製造業、主に購買・調達部門にお勤めの方々に向けた情報を配信しております。
新任の方やベテランの方、管理職を対象とした幅広いコンテンツをご用意しております。
お問い合わせ
コストダウンが利益に直結する術だと理解していても、なかなか前に進めることができない状況。そんな時は、newjiのコストダウン自動化機能で大きく利益貢献しよう!
(Β版非公開)