- お役立ち記事
- Manufacturing Process of Electric Grinders and Improving Grinding Power
Manufacturing Process of Electric Grinders and Improving Grinding Power
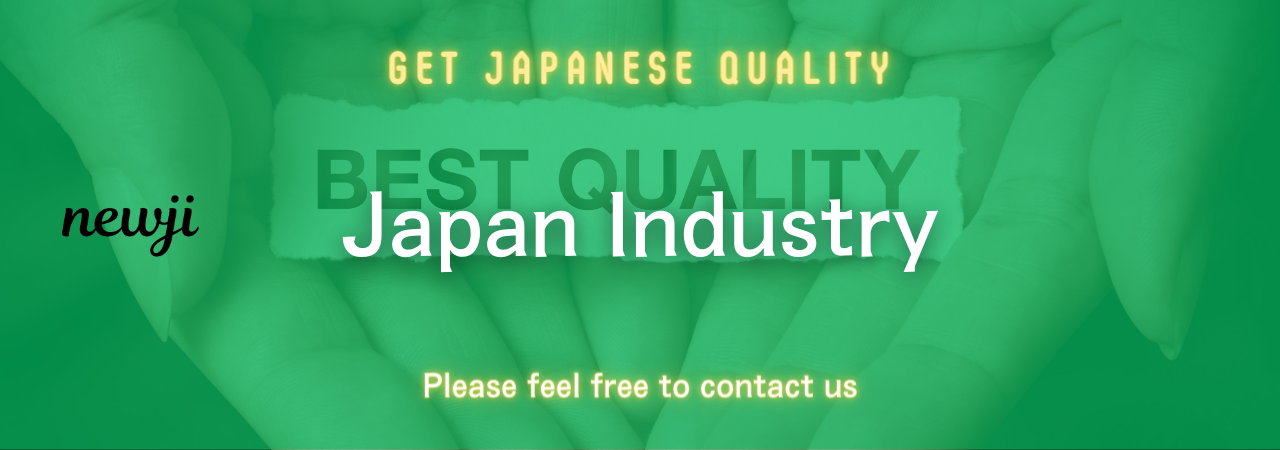
Electric grinders are essential tools in various industries and homes due to their versatility and efficiency.
Whether you’re a professional in a manufacturing setting or a DIY enthusiast, understanding the manufacturing process of electric grinders and knowing how to improve their grinding power can be invaluable.
In this detailed guide, we’ll explore the intricacies involved in crafting these powerful devices and provide insight on how to enhance their performance.
目次
Understanding the Basic Components of an Electric Grinder
Electric grinders consist of a few key components that work in tandem to deliver optimal performance.
Before we dive into the manufacturing process, let’s first identify and understand these fundamental parts:
1. Motor
The motor is the heart of the electric grinder.
It converts electrical energy into mechanical energy, driving the grinding wheel.
The power, efficiency, and durability of the motor significantly affect the grinder’s overall performance.
2. Grinding Wheel
The grinding wheel is the part that does the actual grinding.
It is typically made from abrasive materials like aluminum oxide or silicon carbide, which determine its effectiveness in cutting or grinding materials.
3. Housing
The housing encloses and protects the internal components of the grinder.
It is usually made from durable materials like metal or high-impact plastic.
4. Power Switch
The power switch is a safety mechanism that allows the user to control the operation of the grinder.
It ensures that the grinder can be easily turned on and off as needed.
The Manufacturing Process of Electric Grinders
Creating an electric grinder involves several crucial steps, each contributing to the tool’s overall quality and performance.
Below, we outline the process from start to finish.
Step 1: Design and Engineering
The first step in manufacturing an electric grinder is designing and engineering the product.
Engineers and designers work together to create detailed blueprints and specifications that outline the grinder’s dimensions, components, and features.
This stage may include computer-aided design (CAD) software to create 3D models and simulations.
Step 2: Material Selection
Once the design is finalized, the next step is to select the appropriate materials for each component.
High-quality metals and plastics are chosen to ensure durability and efficiency.
The grinding wheel material is particularly important, as it affects the grinder’s cutting and grinding performance.
Step 3: Component Manufacturing
With materials in hand, individual components are manufactured using various processes such as casting, machining, and injection molding.
Step 4: Motor Assembly
The motor is assembled using pre-manufactured parts like the rotor, stator, bearings, and winding.
The motor’s efficiency and power can be optimized by ensuring precise assembly and high-quality parts.
Step 5: Grinding Wheel Production
The grinding wheel is produced by mixing abrasive particles with a bonding agent, then shaping and hardening it through a process called vitrification.
This results in a robust and effective grinding wheel ready for use.
Step 6: Final Assembly
All components, including the motor, grinding wheel, housing, and power switch, are assembled into the final product.
This step requires careful attention to detail to ensure that all parts fit together perfectly and the grinder operates smoothly.
Step 7: Quality Control
Before an electric grinder can be shipped, it undergoes rigorous quality control tests.
These tests include performance checks, safety inspections, and durability assessments to guarantee that the product meets high standards.
Improving the Grinding Power of Electric Grinders
Maximizing the grinding power of your electric grinder can significantly enhance its performance and extend its lifespan.
Here are some practical tips on how to achieve this:
1. Use the Right Grinding Wheel
Choosing the right grinding wheel is critical for optimal performance.
Ensure the wheel matches the material you are working on and is suited for the specific task (e.g., cutting, grinding, or polishing).
2. Maintain the Motor
Regular maintenance of the motor can prevent overheating and ensure consistent power delivery.
Keep the motor clean and lubricate moving parts as needed.
3. Adjust Speed Settings
Most electric grinders come with adjustable speed settings.
Using the right speed for your specific task can improve efficiency and reduce wear on the grinding wheel and motor.
4. Keep the Grinder Clean
Dust and debris can accumulate inside the grinder, affecting its performance.
Regular cleaning helps maintain efficiency and prolongs the life of the tool.
5. Use Proper Techniques
Employing the right grinding techniques can make a significant difference.
Apply consistent pressure, angle the grinder correctly, and let the tool do the work instead of forcing it.
Safety Tips for Using Electric Grinders
Safety should always be a priority when using electric grinders.
Follow these essential tips to ensure a safe operating environment:
1. Wear Protective Gear
Always wear safety goggles, gloves, ear protection, and a dust mask to protect yourself from flying debris and noise.
2. Secure the Workpiece
Ensure the material you are grinding is securely clamped or held in place to prevent accidents.
3. Inspect the Grinder Before Use
Check the grinder for any signs of damage or wear before using it.
Make sure the grinding wheel is tightly secured and the power cord is in good condition.
4. Operate in a Safe Environment
Use the grinder in a well-lit, clean, and uncluttered area to avoid tripping hazards and ensure good visibility.
Understanding the manufacturing process of electric grinders and knowing how to improve their grinding power can greatly enhance your use of these versatile tools.
By paying attention to details and following best practices, you can ensure that your electric grinder remains powerful, efficient, and safe for all your grinding needs.
資料ダウンロード
QCD調達購買管理クラウド「newji」は、調達購買部門で必要なQCD管理全てを備えた、現場特化型兼クラウド型の今世紀最高の購買管理システムとなります。
ユーザー登録
調達購買業務の効率化だけでなく、システムを導入することで、コスト削減や製品・資材のステータス可視化のほか、属人化していた購買情報の共有化による内部不正防止や統制にも役立ちます。
NEWJI DX
製造業に特化したデジタルトランスフォーメーション(DX)の実現を目指す請負開発型のコンサルティングサービスです。AI、iPaaS、および先端の技術を駆使して、製造プロセスの効率化、業務効率化、チームワーク強化、コスト削減、品質向上を実現します。このサービスは、製造業の課題を深く理解し、それに対する最適なデジタルソリューションを提供することで、企業が持続的な成長とイノベーションを達成できるようサポートします。
オンライン講座
製造業、主に購買・調達部門にお勤めの方々に向けた情報を配信しております。
新任の方やベテランの方、管理職を対象とした幅広いコンテンツをご用意しております。
お問い合わせ
コストダウンが利益に直結する術だと理解していても、なかなか前に進めることができない状況。そんな時は、newjiのコストダウン自動化機能で大きく利益貢献しよう!
(Β版非公開)