- お役立ち記事
- The difference between Work Standards and Quality Standards
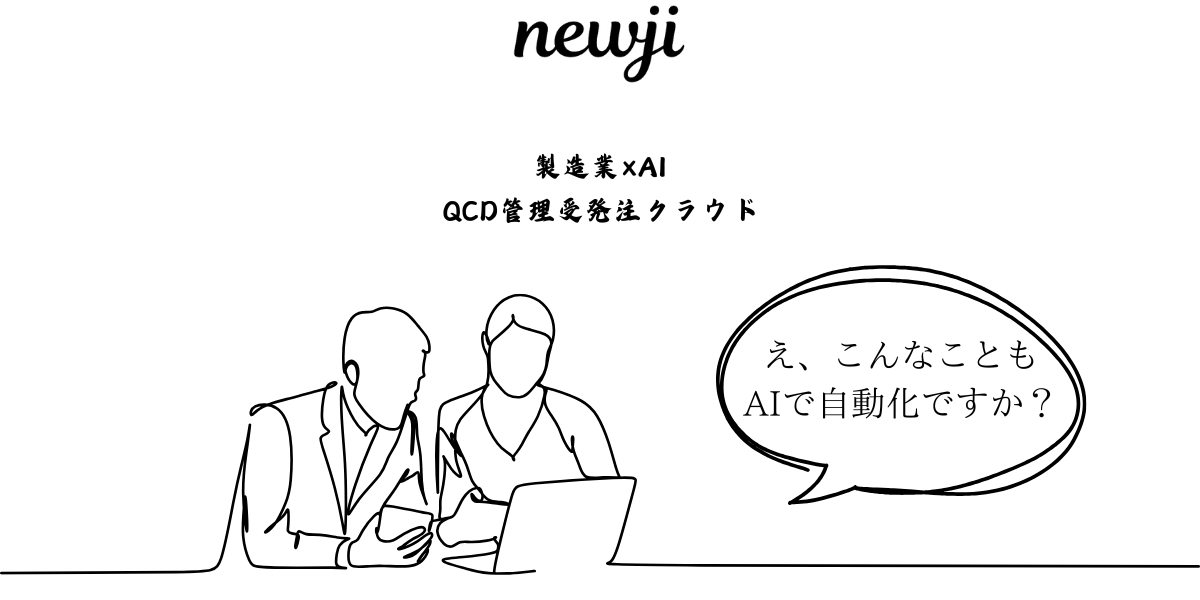
The difference between Work Standards and Quality Standards
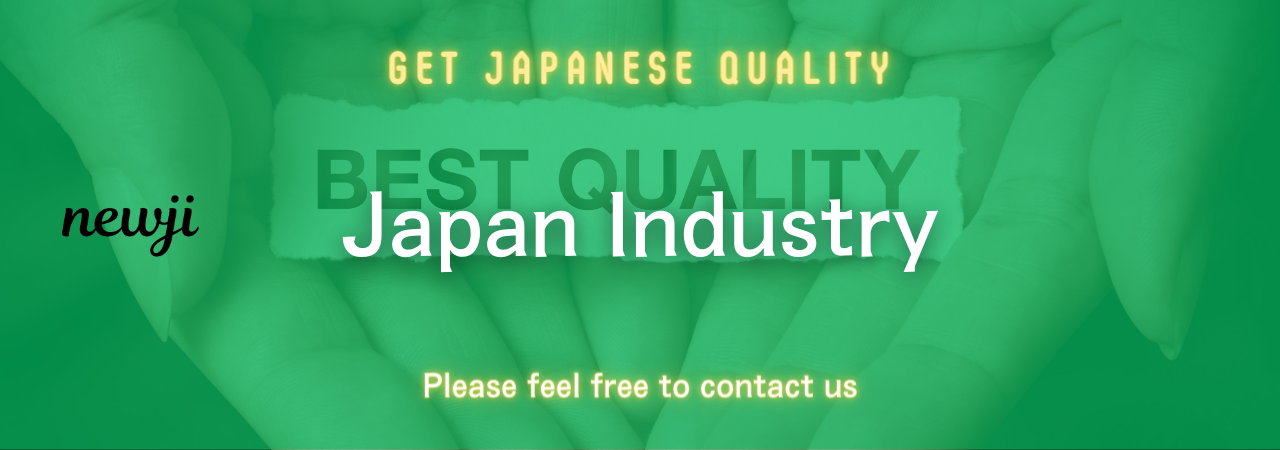
When it comes to maintaining high levels of productivity and ensuring the quality of products and services, organizations rely on certain benchmarks and guidelines.
Two fundamental concepts that often come into play are work standards and quality standards.
Understanding the differences between these two is crucial for both employees and management to achieve excellence in performance and product delivery.
目次
What are Work Standards?
Work standards are the documented expectations and guidelines for how tasks and processes should be completed within an organization.
These standards provide a clear and consistent framework that employees can follow to perform their duties efficiently.
Work standards are typically developed by subject-matter experts and are based on industry best practices, regulatory requirements, and internal organizational goals.
Importance of Work Standards
1. **Consistency:** Work standards ensure that tasks are performed in a consistent manner, regardless of who is performing them.
This eliminates variability and ensures that outcomes are predictable.
2. **Efficiency:** By providing a clear roadmap for completing tasks, work standards help employees work more efficiently.
Time is not wasted figuring out what needs to be done or how to do it.
3. **Training:** New employees can quickly get up to speed by following established work standards.
This reduces the learning curve and helps them become productive members of the team more quickly.
Components of Work Standards
Work standards generally include several key components:
– **Procedures:** Step-by-step instructions for how tasks should be completed.
– **Responsibilities:** Clear delineation of roles and responsibilities.
– **Timelines:** Expected time frames for completing tasks.
– **Tools and Equipment:** Specifications for the tools and equipment that should be used.
What are Quality Standards?
Quality standards are the criteria and specifications that products or services must meet to ensure they satisfy customer requirements and regulatory guidelines.
These standards are often developed by industry bodies, regulatory agencies, or organizations themselves.
Quality standards are used to measure and control the quality of products and services, ensuring they meet predefined benchmarks.
Importance of Quality Standards
1. **Customer Satisfaction:** Quality standards ensure that products and services meet customer expectations, which is crucial for retaining and attracting clients.
2. **Regulatory Compliance:** Adhering to quality standards helps organizations meet regulatory requirements, avoiding legal issues and potential fines.
3. **Market Competitiveness:** High-quality products and services differentiate an organization from its competitors, offering a competitive edge in the market.
Components of Quality Standards
Quality standards usually include:
– **Specifications:** Detailed descriptions of the characteristics of the product or service, such as dimensions, weight, materials, and functionalities.
– **Testing Methods:** Procedures for evaluating whether the product or service meets the specified criteria.
– **Acceptance Criteria:** The benchmarks that a product or service must meet to be considered acceptable.
Difference Between Work Standards and Quality Standards
While both work standards and quality standards aim to improve performance and outcomes, they serve different purposes and focus on different aspects of the organizational workflow.
Objective
– **Work Standards:** The main objective is to ensure tasks are performed efficiently and consistently.
They focus on how work is done.
– **Quality Standards:** The main objective is to ensure that the final product or service meets customer expectations and regulatory requirements.
They focus on the outcome.
Scope
– **Work Standards:** Typically apply to internal processes and employee performance.
– **Quality Standards:** Apply to the final product or service delivered to the customer.
Focus
– **Work Standards:** Focus on process efficiency and consistency.
– **Quality Standards:** Focus on the quality and reliability of the final output.
Integration of Work and Quality Standards
For an organization to achieve excellence, it is important to integrate both work standards and quality standards effectively.
One cannot exist without the other if the goal is to provide high-quality products and services efficiently.
Steps for Integration
1. **Align Objectives:** Ensure that the objectives of work standards and quality standards are aligned with the overall goals of the organization.
2. **Employee Training:** Train employees to understand and implement both work standards and quality standards in their daily tasks.
3. **Continuous Improvement:** Regularly review and update both types of standards to keep up with industry trends and customer expectations.
4. **Performance Metrics:** Use performance metrics to measure both process efficiency and product quality.
This helps in identifying areas that need improvement.
Conclusion
Understanding the difference between work standards and quality standards is crucial for any organization aiming to excel in its operations and deliver high-quality products and services.
Work standards focus on how tasks should be completed efficiently and consistently, while quality standards ensure that the final output meets customer expectations and regulatory requirements.
By integrating both types of standards, organizations can achieve a balanced approach to performance and quality, leading to increased customer satisfaction and a competitive edge in the market.
Therefore, recognizing and implementing the appropriate standards for your specific needs will help in achieving long-term success.
資料ダウンロード
QCD調達購買管理クラウド「newji」は、調達購買部門で必要なQCD管理全てを備えた、現場特化型兼クラウド型の今世紀最高の購買管理システムとなります。
ユーザー登録
調達購買業務の効率化だけでなく、システムを導入することで、コスト削減や製品・資材のステータス可視化のほか、属人化していた購買情報の共有化による内部不正防止や統制にも役立ちます。
NEWJI DX
製造業に特化したデジタルトランスフォーメーション(DX)の実現を目指す請負開発型のコンサルティングサービスです。AI、iPaaS、および先端の技術を駆使して、製造プロセスの効率化、業務効率化、チームワーク強化、コスト削減、品質向上を実現します。このサービスは、製造業の課題を深く理解し、それに対する最適なデジタルソリューションを提供することで、企業が持続的な成長とイノベーションを達成できるようサポートします。
オンライン講座
製造業、主に購買・調達部門にお勤めの方々に向けた情報を配信しております。
新任の方やベテランの方、管理職を対象とした幅広いコンテンツをご用意しております。
お問い合わせ
コストダウンが利益に直結する術だと理解していても、なかなか前に進めることができない状況。そんな時は、newjiのコストダウン自動化機能で大きく利益貢献しよう!
(Β版非公開)