- お役立ち記事
- Manufacturing Process of Electric Air Pumps and Improving Pressure Control Technology
Manufacturing Process of Electric Air Pumps and Improving Pressure Control Technology
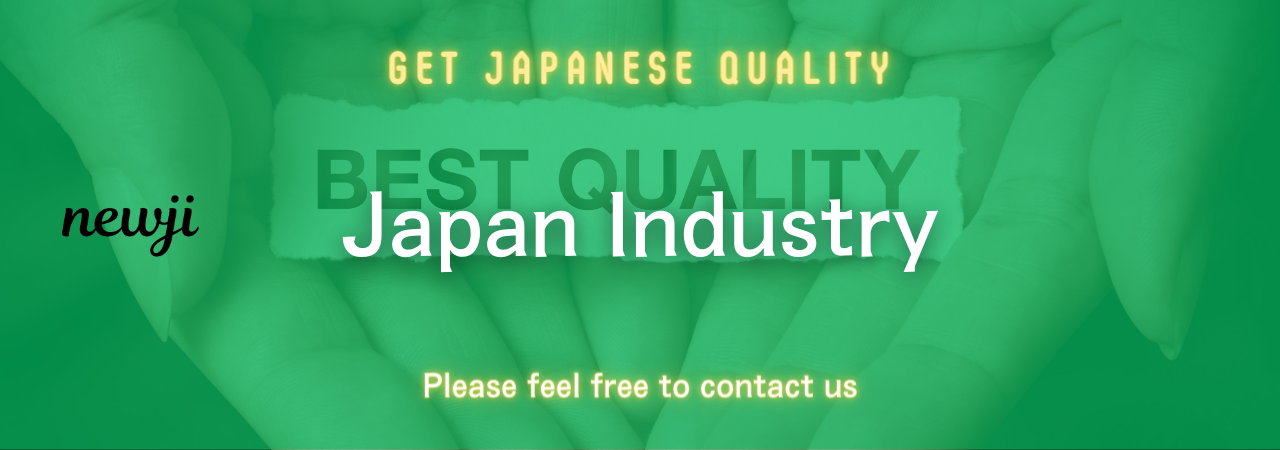
Electric air pumps have become an essential tool in various applications, from inflating tires and sports equipment to supporting medical devices and industrial machinery.
The manufacturing process of electric air pumps involves multiple stages, each requiring precision and quality control to ensure optimal performance.
目次
Understanding the Basics of Electric Air Pumps
Electric air pumps operate by converting electrical energy into mechanical energy, which in turn moves air from one place to another.
They consist of several key components, including a motor, air compartment, and various valves and sensors.
These components must work together seamlessly for the pump to be effective and efficient.
Initial Design and Prototyping
The first step in the manufacturing process is initial design and prototyping.
Engineers use computer-aided design (CAD) software to create detailed digital models of the air pump.
These models allow for precise calculations and simulations, helping engineers identify potential issues before physical prototypes are built.
Once the design is finalized, a prototype is created.
This prototype undergoes extensive testing to ensure it meets all performance specifications.
Any necessary adjustments are made to the design at this stage to refine the product further.
Material Selection and Sourcing
Selecting the right materials is crucial for manufacturing reliable electric air pumps.
Materials must be durable, lightweight, and resistant to wear and tear.
Commonly used materials include high-grade plastics, aluminum, and stainless steel.
Manufacturers source these materials from trusted suppliers to ensure consistency and quality.
Each batch of materials is inspected for defects before moving on to the next stage of production.
Component Manufacturing
The manufacturing of individual components begins once the materials have been sourced.
This process involves using various techniques, such as injection molding for plastic parts, and precision machining for metal components.
Quality control is key during this stage.
Each component is measured and inspected to ensure it meets the strict tolerances specified in the design.
Any faulty parts are discarded and replaced.
Assembly of the Electric Air Pump
With the components manufactured, the assembly process can begin.
This stage involves putting together the motor, air compartment, valves, and sensors into a single unit.
Automated assembly lines are often used to ensure consistency and efficiency.
Technicians perform regular checks to ensure each assembly is correctly put together.
Once assembled, the pumps undergo initial testing to ensure they operate as intended.
Pressure Control Technology
Modern electric air pumps are equipped with advanced pressure control technology.
This technology allows the pump to maintain accurate and consistent air pressure, which is crucial for many applications.
Pressure Sensors
Pressure sensors are integral to pressure control technology.
These sensors measure the air pressure within the pump and send real-time data to the control unit.
High-quality sensors are essential for accurate readings.
Feedback Systems
Feedback systems work in tandem with pressure sensors to adjust the pump’s operation.
When the sensors detect a pressure change, the feedback system sends signals to the motor to either increase or decrease its speed.
This helps maintain the desired pressure level.
Electronic Control Units (ECUs)
Electronic Control Units (ECUs) act as the brain of the pressure control system.
They process data from the sensors and determine the necessary actions to maintain pressure.
Advanced ECUs can handle multiple inputs and provide precise control over the pump’s operation.
Final Testing and Quality Assurance
After assembly, the electric air pumps undergo rigorous testing.
These tests include performance assessments, durability tests, and safety checks.
Each pump is tested under various conditions to ensure it can withstand real-world applications.
Pumps that pass these tests are approved for packaging and distribution.
Packaging and Distribution
The final step is packaging and distribution.
Pumps are carefully packed to prevent damage during transit.
Manufacturers often use eco-friendly materials for packaging to reduce environmental impact.
Once packaged, the pumps are distributed to retailers, wholesalers, or directly to customers.
Efficient logistics ensure the products reach their destination promptly.
Continuous Improvement in Manufacturing
The manufacturing process of electric air pumps is continually evolving.
Manufacturers invest in research and development to improve pump efficiency, durability, and pressure control technology.
Feedback from users and advancements in technology drive these improvements.
By staying at the forefront of innovation, manufacturers can produce high-quality electric air pumps that meet the ever-changing needs of various industries.
Electric air pumps are essential in many applications, and their manufacturing process is a testament to precision and technological advancement.
By understanding this process, we can appreciate the complexity and innovation behind these indispensable devices.
資料ダウンロード
QCD調達購買管理クラウド「newji」は、調達購買部門で必要なQCD管理全てを備えた、現場特化型兼クラウド型の今世紀最高の購買管理システムとなります。
ユーザー登録
調達購買業務の効率化だけでなく、システムを導入することで、コスト削減や製品・資材のステータス可視化のほか、属人化していた購買情報の共有化による内部不正防止や統制にも役立ちます。
NEWJI DX
製造業に特化したデジタルトランスフォーメーション(DX)の実現を目指す請負開発型のコンサルティングサービスです。AI、iPaaS、および先端の技術を駆使して、製造プロセスの効率化、業務効率化、チームワーク強化、コスト削減、品質向上を実現します。このサービスは、製造業の課題を深く理解し、それに対する最適なデジタルソリューションを提供することで、企業が持続的な成長とイノベーションを達成できるようサポートします。
オンライン講座
製造業、主に購買・調達部門にお勤めの方々に向けた情報を配信しております。
新任の方やベテランの方、管理職を対象とした幅広いコンテンツをご用意しております。
お問い合わせ
コストダウンが利益に直結する術だと理解していても、なかなか前に進めることができない状況。そんな時は、newjiのコストダウン自動化機能で大きく利益貢献しよう!
(Β版非公開)