- お役立ち記事
- The difference between BOM (Bill of Materials) and BOP (Bill of Process)
The difference between BOM (Bill of Materials) and BOP (Bill of Process)
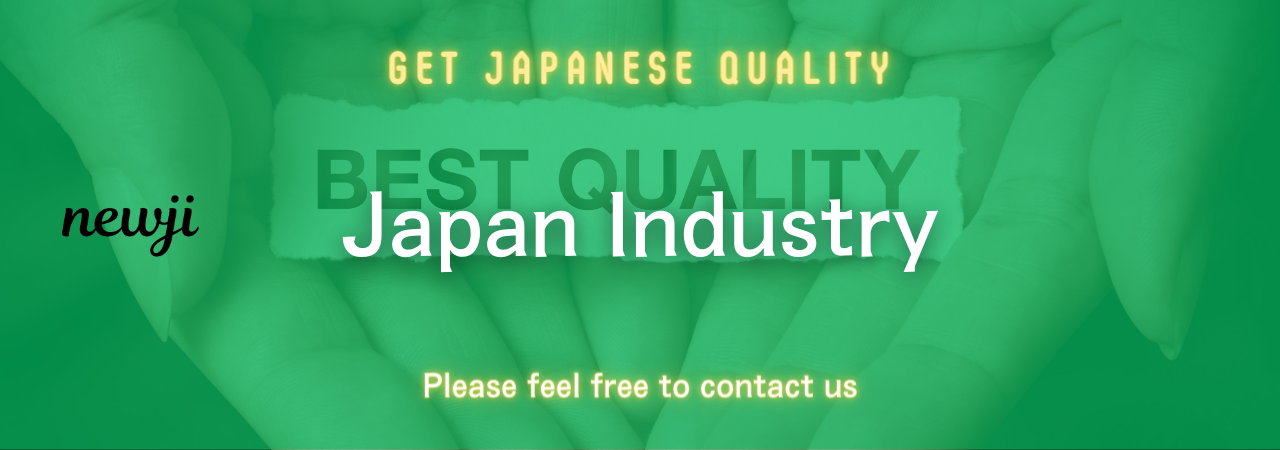
Understanding the world of manufacturing terms can be challenging, especially when some of them sound quite similar.
Yet, two such terms—BOM (Bill of Materials) and BOP (Bill of Process)—are fundamental concepts that play crucial roles in the manufacturing process.
Let’s delve into these concepts and understand their differences.
目次
What is a Bill of Materials (BOM)?
A BOM, or Bill of Materials, is a comprehensive list of raw materials, components, and assemblies required to create a product.
Think of it as the recipe required to produce a final product, encompassing everything from individual nuts and bolts to complex sub-assemblies.
The BOM serves several purposes in a manufacturing environment, acting as a key document in production planning, inventory management, and costing.
Components of a BOM
A well-formed BOM typically contains the following elements:
– **Part Number:** A unique identifier for each item.
– **Description:** A brief but informative description of each item.
– **Quantity:** The number of units required to make one final product.
– **Unit of Measure:** The unit in which the item is measured, such as piece, kilogram, meter, etc.
– **Manufacturer Information:** Sometimes, details about where to source each material are included.
Types of BOMs
There are different types of BOMs based on the specifics of production and the industry.
Here are a couple of commonly used types:
– **Engineering BOM (EBOM):** Used primarily by product design engineers to document product design.
– **Manufacturing BOM (MBOM):** Focuses on listing materials and components required for manufacturing.
What is a Bill of Process (BOP)?
On the other hand, a BOP, or Bill of Process, outlines the steps, policies, and stages required to manufacture a product.
It is a detailed guide describing how to turn the raw materials listed in a BOM into a finished product.
If a BOM is the “what,” then the BOP is the “how.”
Components of a BOP
A BOP often includes several crucial elements such as:
– **Process Steps:** Detailed steps or operations needed to manufacture the product.
– **Sequence:** The order in which these steps should be carried out.
– **Resources Required:** Tools, machines, and other facilities needed to perform each step.
– **Quality Checks:** Policies and checks to ensure each step meets quality standards.
– **Time Estimates:** Estimated time to complete each step or the entire production process.
The Role of BOP in Production
The BOP serves as the roadmap for the production team, guiding them through every step of the manufacturing process.
This document ensures consistency, efficiency, and quality across production runs.
It is essential for training new employees, continuous process improvement, and troubleshooting production issues.
Key Differences Between BOM and BOP
While both BOM and BOP are critical to manufacturing, they serve different purposes and are composed of distinct elements.
Core Focus
The BOM is focused on the “what” aspect:
– What materials are needed?
– What components are required?
The BOP concentrates on the “how”:
– How should the materials be assembled?
– How should the components be processed?
Usage
The BOM is extensively used by various departments, including procurement, inventory management, engineering, and production planning.
The BOP is predominantly used by the production team, quality control, and sometimes by the engineering department when developing new processes.
Format and Detail
The BOM is typically a list, sometimes in a hierarchical structure that shows the relationships between parts and sub-assemblies.
The BOP, however, reads more like a step-by-step instruction manual, outlining the sequence of operations.
Importance of Synchronization
For a manufacturing process to run efficiently, the BOM and BOP must be in perfect synchronization.
A mismatch can result in production delays, quality issues, and increased costs.
Why Synchronization Matters
Imagine having a complete BOM ready but lacking a detailed BOP.
Your team will have all the materials but no clear method on how to assemble them.
Similarly, a detailed BOP without a corresponding BOM means your team knows the process but lacks the necessary materials.
Ways to Achieve Synchronization
– **Regular Updates:** Both BOM and BOP should be periodically reviewed and updated to reflect any changes in the design or process.
– **Cross-Department Collaboration:** Open communication channels between departments that handle BOM and BOP can eliminate misunderstandings and ensure both documents are aligned.
– **Integrated Software Systems:** Using ERP (Enterprise Resource Planning) systems that can handle both BOM and BOP comprehensively can ensure real-time updates and synchronization.
Conclusion
Understanding the differences between BOM (Bill of Materials) and BOP (Bill of Process) is essential for anyone involved in manufacturing.
The BOM outlines what is needed to produce a product, while the BOP describes how to produce it.
Both documents must work in harmony to achieve efficient, quality, and cost-effective manufacturing.
By keeping both your BOM and BOP updated and synchronized, you ensure a smooth production process, reducing the likelihood of errors and increasing overall efficiency.
Whether you are an engineer, production manager, or a supply chain professional, grasping these concepts can drastically improve your manufacturing workflow.
資料ダウンロード
QCD調達購買管理クラウド「newji」は、調達購買部門で必要なQCD管理全てを備えた、現場特化型兼クラウド型の今世紀最高の購買管理システムとなります。
ユーザー登録
調達購買業務の効率化だけでなく、システムを導入することで、コスト削減や製品・資材のステータス可視化のほか、属人化していた購買情報の共有化による内部不正防止や統制にも役立ちます。
NEWJI DX
製造業に特化したデジタルトランスフォーメーション(DX)の実現を目指す請負開発型のコンサルティングサービスです。AI、iPaaS、および先端の技術を駆使して、製造プロセスの効率化、業務効率化、チームワーク強化、コスト削減、品質向上を実現します。このサービスは、製造業の課題を深く理解し、それに対する最適なデジタルソリューションを提供することで、企業が持続的な成長とイノベーションを達成できるようサポートします。
オンライン講座
製造業、主に購買・調達部門にお勤めの方々に向けた情報を配信しております。
新任の方やベテランの方、管理職を対象とした幅広いコンテンツをご用意しております。
お問い合わせ
コストダウンが利益に直結する術だと理解していても、なかなか前に進めることができない状況。そんな時は、newjiのコストダウン自動化機能で大きく利益貢献しよう!
(Β版非公開)