- お役立ち記事
- Manufacturing Process of Tachometers and Accuracy Enhancement
Manufacturing Process of Tachometers and Accuracy Enhancement
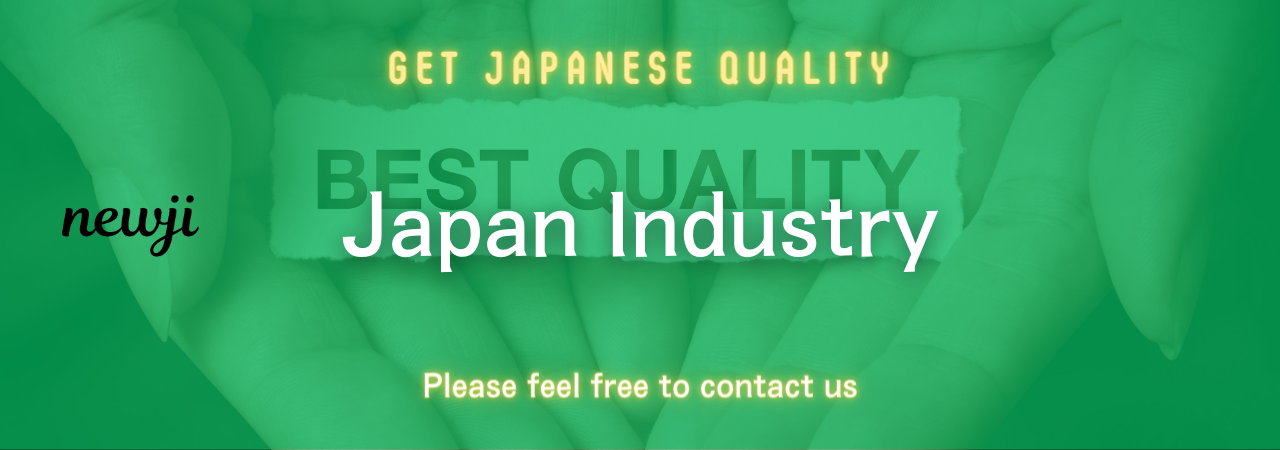
The tachometer is a critical instrument found in various machines, particularly within the automotive and aerospace industries.
Understanding its manufacturing process and the methods used to ensure its accuracy can provide valuable insights for businesses and enthusiasts alike.
目次
Understanding Tachometers
A tachometer measures the rotation speed of a shaft or a disk, typically in revolutions per minute (RPM).
This device is crucial for monitoring the performance of engines and machinery, ensuring they operate within their optimal speed range.
Modern tachometers come in both analog and digital forms, each with its unique manufacturing process.
Basic Components of Tachometers
Regardless of whether a tachometer is analog or digital, certain core components are essential for its function.
These include the sensor, processing unit, and display unit.
The Sensor
The sensor detects the rotational speed of the shaft.
Common types of sensors include magnetic pickup sensors, optical sensors, and hall-effect sensors.
Each sensor type has its method of detecting rotation, but they all serve the same fundamental purpose.
The Processing Unit
The processing unit converts the raw data from the sensor into a readable format.
In analog tachometers, this involves a series of mechanical and electrical processes.
In digital tachometers, microprocessors or microcontrollers handle this task.
The Display Unit
The display unit presents the rotation speed to the user.
Analog tachometers use a needle and dial, while digital tachometers use LCD or LED screens to show precise numerical values.
Manufacturing Process of Analog Tachometers
The manufacturing of analog tachometers involves several precise steps:
Step 1: Designing the Components
The first step is designing the tachometer’s components.
Engineers create detailed drawings and specifications for the sensor, processing unit, and display unit.
These designs must meet rigorous industry standards to ensure reliable performance.
Step 2: Fabricating the Sensor
Manufacturing the sensor involves creating a coil of conducting material or integrating magnet-sensitive materials for magnetic pickup sensors.
Optical sensors require precise placement of light-emitting diodes (LEDs) and photodetectors.
Each type of sensor must be carefully calibrated to ensure accurate readings.
Step 3: Assembling the Processing Unit
The processing unit includes intricate electrical circuits and mechanical linkages.
Components like resistors, capacitors, and transistors are placed on a printed circuit board (PCB) based on the tachometer’s design specifications.
In some cases, fine-tuning is necessary to ensure the unit processes the sensor’s data correctly.
Step 4: Creating the Display Unit
For analog tachometers, the display unit typically involves manufacturing a dial and needle.
The dial is often printed with high-precision instruments to ensure the RPM numbers are clear and accurate.
The needle is then attached to a central pivot connected to the processing unit.
Step 5: Final Assembly and Calibration
Once all components are ready, they are assembled into a single unit.
Each tachometer undergoes rigorous testing and calibration to ensure accuracy.
Testing often involves running the tachometer under different rotational speeds to verify that it displays the correct RPM.
Manufacturing Process of Digital Tachometers
The process of manufacturing digital tachometers shares some similarities with analog tachometers, but there are also notable differences:
Step 1: Designing the Digital Circuitry
Engineers design the digital circuitry, including the microcontroller or microprocessor that will process the sensor data.
This step involves creating schematics and laying out the PCB.
Step 2: Fabricating the Sensor
Similar to the process for analog tachometers, the sensor must be fabricated and calibrated.
For digital tachometers, sensors are often more advanced, such as high-resolution optical sensors.
Step 3: Assembling the Processing Unit
The processing unit in digital tachometers involves placing microchips and electronic components onto the PCB.
Surface-mount technology (SMT) is commonly used to mount the components precisely.
Programming the microcontroller with the necessary software or firmware is also part of this step.
Step 4: Creating the Digital Display
The display unit for digital tachometers involves manufacturing or sourcing LCD or LED screens.
These screens must be capable of displaying RPM values clearly and precisely.
Step 5: Final Assembly and Testing
All components are assembled into the tachometer casing.
Rigorous testing and calibration are critical to ensure the digital tachometer functions accurately across various speeds.
Software algorithms often play a significant role in this calibration process.
Enhancing Tachometer Accuracy
Accurate tachometer readings are essential for maintaining the optimal performance of engines and machinery.
Several methods are employed to enhance the accuracy of tachometers:
High-Precision Sensors
Using high-precision sensors with advanced materials and technologies can improve accuracy.
Optical sensors with higher resolutions and magnetoresistive sensors are examples of more precise options.
Calibration Techniques
Regular calibration is vital for accurate readings.
Calibration involves comparing the tachometer’s readings with a known reference and making adjustments as necessary.
Temperature Compensation
Temperature fluctuations can impact sensor performance.
Employing temperature compensation techniques ensures accurate readings despite environmental changes.
Advanced Signal Processing
Implementing advanced signal processing algorithms can filter out noise and provide more accurate RPM readings.
Digital tachometers benefit significantly from these techniques, as microcontrollers can handle complex calculations.
Quality Control
Strict quality control procedures during manufacturing ensure that each tachometer meets high standards.
This includes testing for accuracy, durability, and reliability under various conditions.
Conclusion
The manufacturing process of tachometers, whether analog or digital, involves precise design, fabrication, assembly, and calibration steps.
Ensuring accurate readings requires high-quality sensors, regular calibration, temperature compensation, advanced signal processing, and robust quality control measures.
Understanding these aspects can help in choosing the right tachometer for specific applications and maintaining its performance over time.
By investing in accurate tachometers, industries can ensure the longevity and efficiency of their machines.
資料ダウンロード
QCD調達購買管理クラウド「newji」は、調達購買部門で必要なQCD管理全てを備えた、現場特化型兼クラウド型の今世紀最高の購買管理システムとなります。
ユーザー登録
調達購買業務の効率化だけでなく、システムを導入することで、コスト削減や製品・資材のステータス可視化のほか、属人化していた購買情報の共有化による内部不正防止や統制にも役立ちます。
NEWJI DX
製造業に特化したデジタルトランスフォーメーション(DX)の実現を目指す請負開発型のコンサルティングサービスです。AI、iPaaS、および先端の技術を駆使して、製造プロセスの効率化、業務効率化、チームワーク強化、コスト削減、品質向上を実現します。このサービスは、製造業の課題を深く理解し、それに対する最適なデジタルソリューションを提供することで、企業が持続的な成長とイノベーションを達成できるようサポートします。
オンライン講座
製造業、主に購買・調達部門にお勤めの方々に向けた情報を配信しております。
新任の方やベテランの方、管理職を対象とした幅広いコンテンツをご用意しております。
お問い合わせ
コストダウンが利益に直結する術だと理解していても、なかなか前に進めることができない状況。そんな時は、newjiのコストダウン自動化機能で大きく利益貢献しよう!
(Β版非公開)