- お役立ち記事
- Manufacturing Process of Suspension Arms and Rigidity Improvement
Manufacturing Process of Suspension Arms and Rigidity Improvement
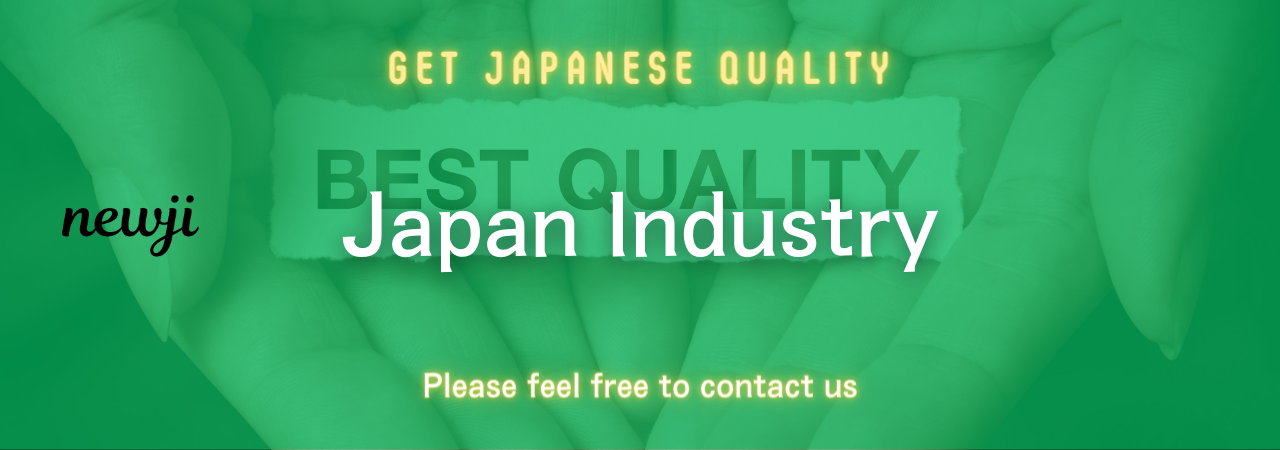
目次
Introduction to Suspension Arms
Suspension arms, also known as control arms, are crucial components in a vehicle’s suspension system.
They connect the wheel hub to the vehicle’s frame, keeping the wheels in contact with the road and allowing smooth driving.
Not only do suspension arms help absorb shocks, but they also play a vital role in vehicle stability and handling.
Understanding their manufacturing process and how to improve their rigidity can significantly enhance a vehicle’s performance and safety.
Materials Used in Suspension Arms
The first step in manufacturing suspension arms involves selecting the right materials.
Traditionally, these components are made of steel due to its strength and durability.
However, advancements in material science have introduced aluminum and composites as alternative materials.
Aluminum offers the advantage of being lighter than steel, which can improve fuel efficiency.
Composite materials, on the other hand, provide a unique combination of strength and lightness.
Steel Suspension Arms
Steel is widely used for its robustness and ability to withstand significant stress.
It is relatively inexpensive and easy to manufacture, making it a popular choice for many automotive companies.
However, steel is heavy, which can negatively impact a vehicle’s overall weight.
Aluminum Suspension Arms
Aluminum is lighter than steel and offers excellent resistance to corrosion.
This makes it an attractive option for automotive applications, particularly in high-end vehicles where weight reduction is crucial.
Despite its benefits, aluminum is more expensive and can be more challenging to work with.
Composite Suspension Arms
Composite materials, such as carbon fiber-reinforced plastics, are becoming increasingly popular in suspension arm manufacturing.
These materials offer high strength-to-weight ratios but come at a premium cost.
The complexity of manufacturing composite components also requires advanced techniques and machinery.
Manufacturing Process
The process of manufacturing suspension arms involves several stages, each critical to the final product’s quality and performance.
Design and Prototyping
The initial phase focuses on designing the suspension arms using computer-aided design (CAD) software.
Engineers create detailed models to simulate how the suspension arms will perform under various conditions.
Once the design is finalized, prototypes are manufactured and tested to validate their performance.
Material Preparation
After the design phase, the next step is material preparation.
For steel suspension arms, large sheets or rods of steel are cut into the required shapes using laser cutting or machining techniques.
For aluminum and composite materials, similar cutting processes are employed, but additional care is needed to avoid damage.
Forming and Shaping
Once the materials are prepared, they undergo forming and shaping processes.
Steel suspension arms are typically hot-forged, where the steel is heated and then hammered into shape.
Aluminum arms can be either hot-forged or cold-extruded, depending on the desired properties.
Composite materials are usually molded using specialized techniques, such as vacuum infusion or autoclaving.
Machining and Finishing
After forming, the suspension arms need further machining to achieve the final shape and dimensions.
Machining includes drilling holes, adding threads, and refining surfaces to meet exact specifications.
Finishing processes like heat treatment for steel or anodizing for aluminum enhance the arms’ durability and appearance.
Quality Control
The final stage in manufacturing is quality control.
Each suspension arm undergoes rigorous testing to ensure it meets safety and performance standards.
Techniques such as X-ray inspection, ultrasonic testing, and tensile testing are used to detect any defects.
Improving Rigidity in Suspension Arms
Rigidity is a critical factor in the performance of suspension arms.
Improved rigidity translates to better handling, stability, and overall vehicle safety.
Optimizing Design
One of the foremost methods to enhance rigidity is through optimized design.
Using advanced simulation tools, engineers can identify areas where material can be added or altered to increase strength without significantly increasing weight.
Topology optimization and finite element analysis (FEA) are commonly used techniques in this phase.
Material Selection
Choosing the right material is also paramount for improving rigidity.
High-strength steel alloys, advanced aluminum alloys, and optimized composite materials can all contribute to a more rigid suspension arm.
Research and development in material science continually bring forth new materials that offer better performance.
Heat Treatment
For metal suspension arms, heat treatment processes can enhance rigidity.
By altering the internal structure of the metal through processes such as quenching and tempering, manufacturers can significantly improve the material’s strength.
Adding Reinforcements
Another method to improve rigidity involves adding reinforcements to the suspension arms.
This may include integrating ribbing structures, using layered composite materials, or installing additional support brackets.
Reinforcements can help distribute loads more evenly and reduce stress concentration points.
Conclusion
Understanding the manufacturing process of suspension arms and the techniques to improve their rigidity is vital for anyone in the automotive industry.
From selecting appropriate materials to employing advanced design and manufacturing techniques, each step plays a critical role in ensuring the highest quality and performance.
As technology continues to advance, we can expect even more improvements in the design and manufacture of suspension arms, leading to safer and more efficient vehicles.
資料ダウンロード
QCD調達購買管理クラウド「newji」は、調達購買部門で必要なQCD管理全てを備えた、現場特化型兼クラウド型の今世紀最高の購買管理システムとなります。
ユーザー登録
調達購買業務の効率化だけでなく、システムを導入することで、コスト削減や製品・資材のステータス可視化のほか、属人化していた購買情報の共有化による内部不正防止や統制にも役立ちます。
NEWJI DX
製造業に特化したデジタルトランスフォーメーション(DX)の実現を目指す請負開発型のコンサルティングサービスです。AI、iPaaS、および先端の技術を駆使して、製造プロセスの効率化、業務効率化、チームワーク強化、コスト削減、品質向上を実現します。このサービスは、製造業の課題を深く理解し、それに対する最適なデジタルソリューションを提供することで、企業が持続的な成長とイノベーションを達成できるようサポートします。
オンライン講座
製造業、主に購買・調達部門にお勤めの方々に向けた情報を配信しております。
新任の方やベテランの方、管理職を対象とした幅広いコンテンツをご用意しております。
お問い合わせ
コストダウンが利益に直結する術だと理解していても、なかなか前に進めることができない状況。そんな時は、newjiのコストダウン自動化機能で大きく利益貢献しよう!
(Β版非公開)