- お役立ち記事
- The difference between Predictive Maintenance and Diagnostic Maintenance
The difference between Predictive Maintenance and Diagnostic Maintenance
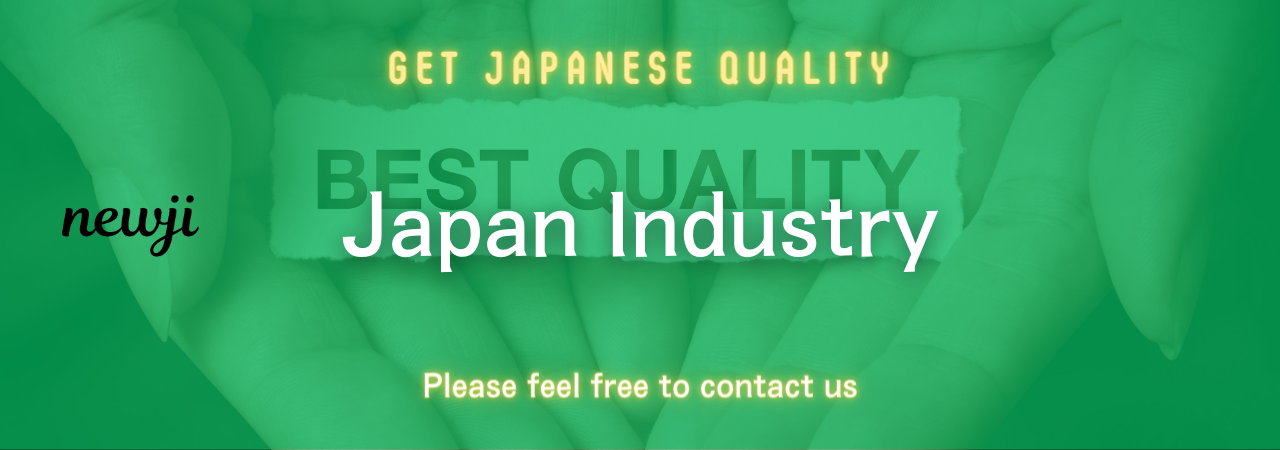
In today’s world of rapidly evolving technology, the maintenance of machinery and equipment has taken on new dimensions.
Industries now have the tools to better monitor, predict, and understand the health of their equipment.
Two popular methods that have emerged in recent years are predictive maintenance and diagnostic maintenance.
While they may sound similar, they serve different purposes and offer unique benefits.
This article will delve into the differences between these two approaches, helping you understand which might be better suited for your needs.
目次
What is Predictive Maintenance?
Predictive maintenance, often referred to as PdM, is a proactive approach to maintenance.
With this method, equipment and machinery are monitored using various sensors and data analytics tools.
The data collected provides insights into the condition and performance of the machines.
By analyzing this data, companies can predict when a machine is likely to fail and take action before it happens.
Key Features of Predictive Maintenance
One of the hallmarks of predictive maintenance is continuous monitoring.
Sensors are installed on machinery to constantly collect data.
This data can include temperature, vibration, noise levels, and other vital parameters.
Another critical feature is data analysis.
Advanced algorithms and machine learning models analyze the data collected from the sensors.
These analyses can identify patterns and trends that signal potential issues.
Finally, predictive maintenance emphasizes timely intervention.
By predicting when a machine will fail, maintenance can be scheduled at the most convenient time, reducing unexpected downtimes and optimizing maintenance costs.
Benefits of Predictive Maintenance
One of the primary benefits of predictive maintenance is reducing unplanned downtimes.
By predicting when failures might occur, companies can schedule maintenance during non-peak times, ensuring that production continues smoothly.
Another benefit is cost savings.
Since maintenance is performed only when necessary, companies can avoid spending money on unnecessary repairs and parts.
Additionally, timely interventions can prevent minor issues from becoming significant, costly problems.
Predictive maintenance also extends the lifespan of machinery and equipment.
By maintaining machines when they truly need it, companies can ensure that their equipment runs efficiently for longer periods.
What is Diagnostic Maintenance?
Diagnostic maintenance, on the other hand, is more reactive.
This approach involves diagnosing or identifying issues after they occur.
When a piece of equipment shows signs of trouble or breaks down, diagnostic maintenance steps in to find the root cause and fix the problem.
Key Features of Diagnostic Maintenance
Diagnostic maintenance often relies on skilled technicians.
These professionals use their expertise to examine and troubleshoot the problematic equipment.
Diagnostic tools are another essential aspect.
These can range from multimeters and oscilloscopes to specialized software that can read error codes and provide details about the malfunction.
An essential part of diagnostic maintenance is problem resolution.
Once the issue is identified, the necessary steps are taken to repair or replace the malfunctioning components.
Benefits of Diagnostic Maintenance
One of the main benefits of diagnostic maintenance is its focus on accurate problem identification.
By pinpointing the exact issue, companies can avoid unnecessary repairs and replace only the parts that are faulty.
This method also supports rapid response.
Once a problem is detected, technicians can quickly identify and address the issue, minimizing downtime.
Another advantage is the detailed insight it provides.
By understanding the root cause of failures, companies can take steps to prevent similar issues in the future, improving overall efficiency.
Comparing Predictive Maintenance and Diagnostic Maintenance
While both maintenance strategies aim to keep equipment running smoothly, their approaches are fundamentally different.
Predictive maintenance is proactive, focusing on preventing issues before they occur.
In contrast, diagnostic maintenance is reactive, dealing with problems after they arise.
Data Utilization
Predictive maintenance heavily relies on continuous data collection and advanced analytics.
It uses this data to forecast potential issues.
Diagnostic maintenance, on the other hand, uses data to understand what has already gone wrong.
Timing of Interventions
In predictive maintenance, interventions are planned and scheduled based on predictions.
This helps in minimizing unplanned downtimes.
Diagnostic maintenance, however, deals with problems as they occur, which can sometimes lead to longer downtimes.
Cost Implications
While predictive maintenance can involve higher upfront costs due to the need for sensors, data analytics tools, and sometimes even specialized staff, it often leads to lower overall maintenance costs.
This is because it reduces unexpected breakdowns and optimizes repair schedules.
Diagnostic maintenance might have lower initial costs but can result in higher expenses over time due to the potentially higher frequency of unexpected repairs and the associated downtime.
Choosing the Right Approach
The right maintenance strategy depends on various factors, including the criticality of the equipment, the industry, available budget, and specific operational goals.
For industries where downtime is extremely costly, such as in manufacturing or power generation, predictive maintenance might be the better choice.
It ensures continuous operation and optimal performance.
On the other hand, for smaller operations with a tighter budget, diagnostic maintenance can be a more feasible option.
Hybrid Approaches
Many companies find that a hybrid approach works best.
By combining elements of both predictive and diagnostic maintenance, they can enjoy the benefits of both.
For instance, they might use predictive maintenance for their most critical equipment while relying on diagnostic maintenance for less crucial machinery.
Conclusion
In summary, both predictive maintenance and diagnostic maintenance offer distinct advantages.
Predictive maintenance focuses on preventing issues before they occur through continuous data monitoring and analysis.
Diagnostic maintenance, however, identifies and resolves problems after they have occurred.
Understanding the differences between these two approaches can help you decide which is best suited for your needs.
Regardless of the approach chosen, both strategies ultimately aim to keep machinery running efficiently and minimize disruptions to operations.
資料ダウンロード
QCD調達購買管理クラウド「newji」は、調達購買部門で必要なQCD管理全てを備えた、現場特化型兼クラウド型の今世紀最高の購買管理システムとなります。
ユーザー登録
調達購買業務の効率化だけでなく、システムを導入することで、コスト削減や製品・資材のステータス可視化のほか、属人化していた購買情報の共有化による内部不正防止や統制にも役立ちます。
NEWJI DX
製造業に特化したデジタルトランスフォーメーション(DX)の実現を目指す請負開発型のコンサルティングサービスです。AI、iPaaS、および先端の技術を駆使して、製造プロセスの効率化、業務効率化、チームワーク強化、コスト削減、品質向上を実現します。このサービスは、製造業の課題を深く理解し、それに対する最適なデジタルソリューションを提供することで、企業が持続的な成長とイノベーションを達成できるようサポートします。
オンライン講座
製造業、主に購買・調達部門にお勤めの方々に向けた情報を配信しております。
新任の方やベテランの方、管理職を対象とした幅広いコンテンツをご用意しております。
お問い合わせ
コストダウンが利益に直結する術だと理解していても、なかなか前に進めることができない状況。そんな時は、newjiのコストダウン自動化機能で大きく利益貢献しよう!
(Β版非公開)