- お役立ち記事
- The difference between Electroforming and Casting
The difference between Electroforming and Casting
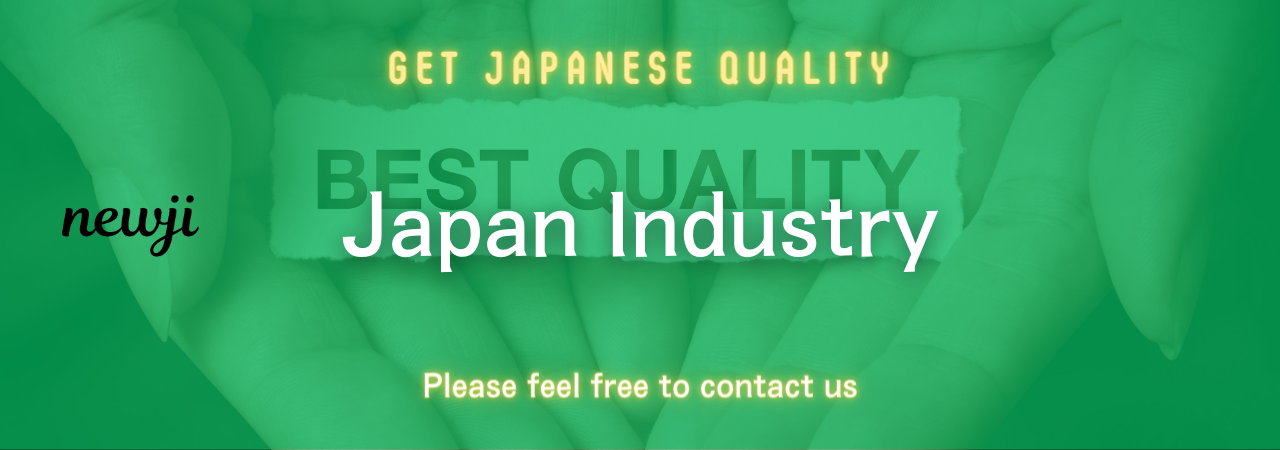
Electroforming and casting are two distinct yet fascinating techniques used in crafting objects.
While both methods have their roots in engineering and manufacturing, they differ significantly in their processes and applications.
Understanding these differences can help in selecting the appropriate method for your specific needs.
目次
What is Electroforming?
Electroforming is an advanced manufacturing technique that involves metal deposition.
It starts with a mold, known as a mandrel, upon which a layer of metal is deposited through an electrolytic bath.
The metal ions in the bath are electrically charged, causing them to adhere to the mold.
Once the desired thickness is achieved, the mandrel is removed, leaving a hollow metal object.
Advantages of Electroforming
One of the primary benefits of electroforming is the precision it offers.
The process allows for intricate details and fine features that are difficult to replicate using other methods.
This makes it ideal for applications such as microelectronics and fine jewelry.
Another advantage is material efficiency.
Since electroforming involves depositing metal only where it’s needed, it reduces waste and can be cost-effective in producing prototypes and complex designs.
Applications of Electroforming
Electroforming is widely used in various industries.
In the electronics sector, it’s employed to create high-precision components like printed circuit boards.
In the jewelry industry, it allows for the crafting of delicate and intricate designs that are both lightweight and robust.
The aerospace industry also uses electroforming for manufacturing lightweight yet sturdy components.
What is Casting?
Casting, on the other hand, is a more traditional technique that has been in use for centuries.
It involves pouring a liquid material, usually metal, into a mold.
The material then cools and solidifies, taking the shape of the mold.
Once hardened, the mold is removed, revealing the final object.
Advantages of Casting
Casting is known for its versatility.
It can be used to create objects of various sizes, from small intricate pieces to large industrial components.
This method is also highly efficient for mass production, making it a popular choice for manufacturing large quantities of identical objects.
Another advantage of casting is its ability to work with different types of materials, including metals, plastics, and ceramics.
This flexibility allows for a wide range of applications, from automotive parts to household items.
Applications of Casting
Casting is prevalent in industries such as automotive, where it is used to produce engine blocks and other vital components.
In the construction industry, casting is utilized to manufacture structural elements like beams and columns.
The art and sculpture world also relies on casting to create everything from statues to intricate ornaments.
Key Differences Between Electroforming and Casting
Despite their similarities, electroforming and casting have several key differences.
Process
The primary difference lies in their processes.
Electroforming involves the deposition of metal through an electrolytic bath, while casting requires pouring liquid material into a mold.
This fundamental distinction leads to variations in the types of objects each method can produce.
Precision and Detail
Electroforming excels in precision.
It can achieve fine details and intricate designs with high accuracy.
Casting, although versatile, may not reach the same level of detail, especially in smaller objects.
Material Efficiency
Electroforming is more material-efficient as it deposits metal only where needed.
Casting involves pouring excess material, which may lead to waste.
However, casting can be more suitable for mass production due to its ability to create multiple identical objects quickly.
Energy Consumption
Electroforming generally consumes more energy due to the electrolytic process.
Casting, especially when utilizing gravity, can be more energy-efficient.
Choosing the Right Technique
The choice between electroforming and casting depends on several factors.
Consider the level of detail required, the type of material, and the production volume.
If precision and intricate details are crucial, electroforming might be the better choice.
For large-scale production and versatility in material, casting may be more suitable.
Industry-specific Considerations
In industries like electronics and aerospace, where precision and lightweight components are essential, electroforming is often the preferred method.
For automotive and construction, casting’s ability to produce large and robust parts makes it more applicable.
Cost Factors
Cost is another critical consideration.
Electroforming can be more expensive due to its specialized process and equipment requirements.
Casting, especially when needed in bulk, can offer cost savings through economies of scale.
Conclusion
Understanding the differences between electroforming and casting is essential for making informed decisions.
Both methods have their unique advantages and are suited to specific applications.
By considering factors such as precision, material efficiency, and cost, you can determine the most appropriate technique for your project.
Whether you choose electroforming or casting, each method offers distinct benefits that can enhance the quality and functionality of your final product.
資料ダウンロード
QCD調達購買管理クラウド「newji」は、調達購買部門で必要なQCD管理全てを備えた、現場特化型兼クラウド型の今世紀最高の購買管理システムとなります。
ユーザー登録
調達購買業務の効率化だけでなく、システムを導入することで、コスト削減や製品・資材のステータス可視化のほか、属人化していた購買情報の共有化による内部不正防止や統制にも役立ちます。
NEWJI DX
製造業に特化したデジタルトランスフォーメーション(DX)の実現を目指す請負開発型のコンサルティングサービスです。AI、iPaaS、および先端の技術を駆使して、製造プロセスの効率化、業務効率化、チームワーク強化、コスト削減、品質向上を実現します。このサービスは、製造業の課題を深く理解し、それに対する最適なデジタルソリューションを提供することで、企業が持続的な成長とイノベーションを達成できるようサポートします。
オンライン講座
製造業、主に購買・調達部門にお勤めの方々に向けた情報を配信しております。
新任の方やベテランの方、管理職を対象とした幅広いコンテンツをご用意しております。
お問い合わせ
コストダウンが利益に直結する術だと理解していても、なかなか前に進めることができない状況。そんな時は、newjiのコストダウン自動化機能で大きく利益貢献しよう!
(Β版非公開)