- お役立ち記事
- The difference between Process Control and Quality Control
The difference between Process Control and Quality Control
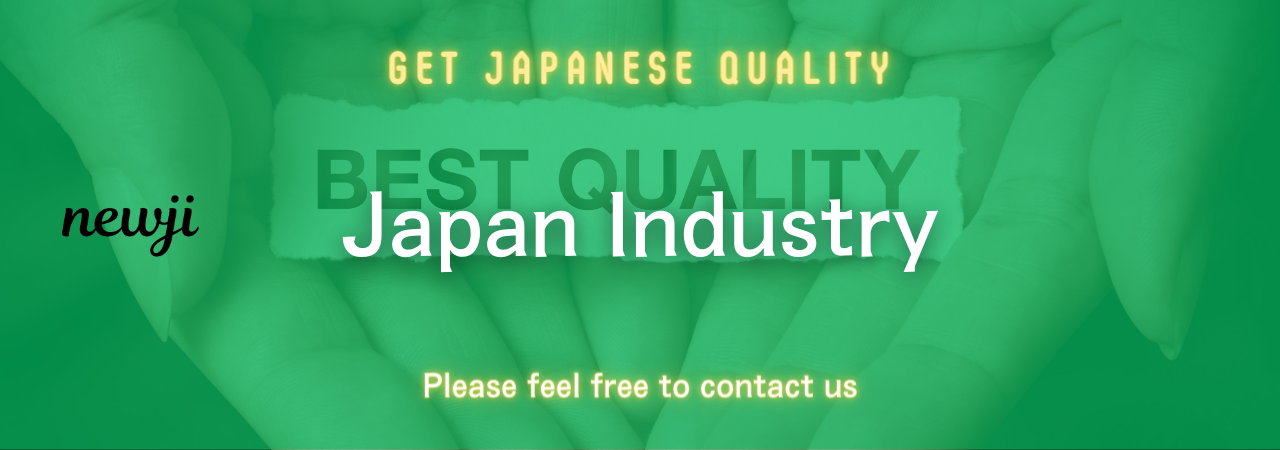
Understanding the difference between process control and quality control can greatly enhance the efficiency and output of your business.
These two concepts are fundamental to maintaining high standards and effective operations in any industry, from manufacturing to service-oriented sectors.
Knowing the distinction between process control and quality control will help you make better decisions and improve overall performance.
目次
What is Process Control?
Process control refers to the methods and mechanisms used to manage and improve processes within an organization.
The goal is to ensure that processes run smoothly and produce the intended outcomes.
In manufacturing, for example, process control involves monitoring and adjusting the machinery and production parameters to maintain optimal conditions.
It can include automation, where sensors and computers are used to regulate the production environment.
Key Elements of Process Control
One of the main elements of process control is monitoring.
This involves continuously measuring various aspects of the process, such as temperature, pressure, and flow rates, to ensure that they stay within specified limits.
Another element is feedback mechanisms.
These are systems that provide real-time data on process performance, allowing for immediate adjustments to be made.
Additionally, control strategies are crucial.
These are pre-defined methods for addressing deviations from the desired process conditions, ensuring that corrective actions are taken promptly.
Benefits of Process Control
Effective process control can lead to numerous benefits.
It can significantly enhance efficiency by reducing downtime and minimizing waste.
Improved consistency in procedures can also lead to higher-quality products or services.
Moreover, process control enables better compliance with regulations, as it ensures that processes are consistently meeting industry standards and legal requirements.
What is Quality Control?
Quality control, on the other hand, focuses on ensuring that the products or services that are produced meet specific quality standards.
This involves various testing and inspection procedures designed to identify defects and ensure that the final output is of high quality.
In essence, quality control is about validating the output rather than the process itself.
Key Elements of Quality Control
Inspection is a core component of quality control.
This involves examining products at different stages of production to identify any defects or inconsistencies.
Testing is another crucial element.
Various tests are conducted to ensure that products meet specific criteria, whether those are related to durability, performance, or safety.
Additionally, quality control involves standards and benchmarks.
These are pre-defined criteria that the product must meet to be considered acceptable.
Benefits of Quality Control
Quality control ensures customer satisfaction by delivering products or services that meet or exceed expectations.
This can lead to increased customer loyalty and repeat business.
Effective quality control can also reduce the cost of rework and returns.
By identifying defects early, corrective actions can be taken before products reach the customer.
Furthermore, strong quality control processes can enhance a company’s reputation, making it a trusted name in the industry.
The Interplay Between Process Control and Quality Control
While process control and quality control serve different functions, they are closely related and often work together to achieve overall operational excellence.
Process control focuses on the “how” – how processes are managed and maintained – whereas quality control focuses on the “what” – what the final product should be like.
Enhancing Each Other
Effective process control can improve quality control by ensuring that the production processes are optimized, reducing the likelihood of defects.
Conversely, strong quality control mechanisms can feed into process control by identifying areas where the process needs improvement.
For example, if quality control detects a recurring defect, this can inform adjustments in the process control parameters to eliminate the issue.
Integrated Approaches
Many modern businesses adopt integrated approaches that combine both process control and quality control.
This holistic approach ensures that processes are optimized for efficiency and that the final outputs meet high-quality standards.
Such integrated systems often involve sophisticated software and technologies that provide real-time data and analytics on both process and product quality.
Implementing Process and Quality Control in Your Business
Successfully implementing both process control and quality control requires a strategic approach.
Steps for Process Control
First, identify the critical processes that need monitoring and controlling.
These are often the processes that have the most significant impact on your business’s efficiency and output.
Next, implement monitoring systems.
These can include sensors, automated controls, and real-time data analytics to continuously track process parameters.
Finally, develop control strategies.
Have predefined methods for addressing deviations and ensure that these are communicated clearly to all relevant personnel.
Steps for Quality Control
Begin by defining the quality standards your products or services must meet.
These should be based on customer expectations, industry regulations, and any other relevant criteria.
Then, implement inspection and testing procedures.
Regularly assess the products at various stages of production to identify defects early.
Lastly, establish feedback loops.
Ensure that the findings from quality control are communicated back to the process control team so that they can make necessary adjustments.
By understanding and implementing robust process control and quality control mechanisms, businesses can achieve greater efficiency and higher quality in their operations.
This not only enhances customer satisfaction but also improves the overall competitiveness of the enterprise.
資料ダウンロード
QCD調達購買管理クラウド「newji」は、調達購買部門で必要なQCD管理全てを備えた、現場特化型兼クラウド型の今世紀最高の購買管理システムとなります。
ユーザー登録
調達購買業務の効率化だけでなく、システムを導入することで、コスト削減や製品・資材のステータス可視化のほか、属人化していた購買情報の共有化による内部不正防止や統制にも役立ちます。
NEWJI DX
製造業に特化したデジタルトランスフォーメーション(DX)の実現を目指す請負開発型のコンサルティングサービスです。AI、iPaaS、および先端の技術を駆使して、製造プロセスの効率化、業務効率化、チームワーク強化、コスト削減、品質向上を実現します。このサービスは、製造業の課題を深く理解し、それに対する最適なデジタルソリューションを提供することで、企業が持続的な成長とイノベーションを達成できるようサポートします。
オンライン講座
製造業、主に購買・調達部門にお勤めの方々に向けた情報を配信しております。
新任の方やベテランの方、管理職を対象とした幅広いコンテンツをご用意しております。
お問い合わせ
コストダウンが利益に直結する術だと理解していても、なかなか前に進めることができない状況。そんな時は、newjiのコストダウン自動化機能で大きく利益貢献しよう!
(Β版非公開)