- お役立ち記事
- Manufacturing Process of Electric Mosquito Repellents and Safety Design Improvement
Manufacturing Process of Electric Mosquito Repellents and Safety Design Improvement
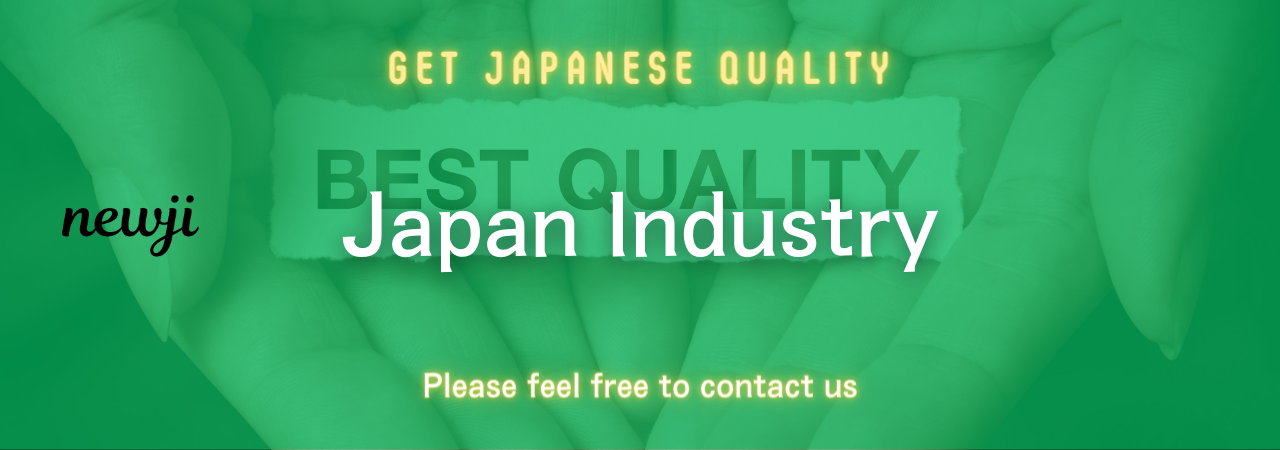
目次
Introduction to Electric Mosquito Repellents
Electric mosquito repellents have become a popular solution for combatting mosquitoes, especially in regions where these pests are prevalent.
These devices use electrical power to emit substances that repel or kill mosquitoes.
Understanding the manufacturing process and safety designs of electric mosquito repellents is crucial for ensuring their effectiveness and user safety.
Raw Materials and Components
The first step in manufacturing electric mosquito repellents is sourcing the raw materials and components.
Key materials include the repellent chemical, often a synthetic insecticide like prallethrin, and the electrical components necessary to power the device.
Additional materials include plastic for the housing and possibly ceramic for parts that require heat resistance.
Repellent Chemicals
Prallethrin is a commonly used insecticide in electric mosquito repellents due to its effectiveness.
It is a synthetic pyrethroid, which means it is derived from pyrethrum, a natural insecticide found in chrysanthemum flowers.
Manufacturers also experiment with natural repellents, such as citronella oil, though these are typically less effective.
Electrical Components
The electrical components consist of a heating element, a power source (usually a plug for electrical outlets), and sometimes a small fan.
The heating element vaporizes the repellent chemical, dispersing it into the air.
In some advanced models, a microcontroller is used for regulating the temperature and ensuring uniform distribution of the repellent.
Design and Assembly
Designing the electric mosquito repellent involves several stages, starting from conceptualization to creating a functional prototype.
Key considerations include the size, shape, and safety features of the device.
Once the design is finalized, the assembly process begins.
Prototype Development
During the prototype stage, designers create several mock-ups to evaluate aesthetics and functionality.
Computer-aided design (CAD) software is often used to draft the initial designs.
Prototypes are made using 3D printing or other rapid prototyping technologies.
Component Assembly
In the assembly process, various components are put together in a specific order.
First, the housing is usually molded and prepared.
Next, the electrical components such as the heating element, wiring, and microcontroller are installed.
These are followed by security checks to ensure the elements fit correctly and function as intended.
Testing and Quality Control
Before electric mosquito repellents can reach the market, they must undergo rigorous testing and quality control procedures.
These tests ensure that the device is both effective against mosquitoes and safe for household use.
Effectiveness Testing
To test the effectiveness, prototypes are placed in controlled environments with mosquitoes.
Different parameters, such as the concentration of the repellent and the temperature of the heating element, are adjusted to find the optimal settings.
Successful models will show a significant reduction in mosquito activity within a short period.
Safety Testing
Safety tests are crucial in evaluating the device’s reliability.
These include electrical safety tests to ensure that the device does not overheat or short-circuit.
Fire safety tests are also conducted to see whether the device can ignite under extreme conditions.
Finally, chemical safety tests are conducted to ensure the repellent substance is not harmful to humans or pets under normal usage conditions.
Production and Scalability
Once the design passes all tests, it moves into mass production.
Production facilities are equipped with specialized machinery to automate the assembly process, enhancing the scalability of production.
Automated Assembly Lines
In modern manufacturing facilities, automated assembly lines are commonly used.
Robotics and automated systems can handle tasks such as soldering electrical components and screwing the housing together.
Automation increases efficiency and reduces the likelihood of human error.
Quality Assurance
Even with automation, human oversight is critical for quality assurance.
Inspectors at various stages of the production line ensure that each device meets the predetermined standards.
Random sampling and rigorous testing are performed on units from each batch to ensure consistency.
Distribution and Market Entry
The final stage involves distributing the electric mosquito repellents to retailers and entering the market.
Proper packaging is also necessary to protect the devices during transportation and to provide essential information to the consumer.
Packaging
Packaging must meet several criteria.
Firstly, it should protect the device from damage during shipping.
Secondly, it should provide all necessary information, including safety instructions and usage guidelines.
Finally, attractive packaging can entice consumers and give the product a competitive edge.
Retail and Online Sales
Distribution channels are diversified to include both physical retailers and online platforms.
Retailers like supermarkets and hardware stores often stock these products, while online marketplaces provide a platform for direct sales to consumers.
Effective marketing campaigns are employed to highlight the product’s benefits and safety features.
Improvements in Safety Design
The safety of electric mosquito repellents is continually being improved to protect users better and enhance product reliability.
Temperature Regulation
One significant improvement is better temperature regulation.
Advanced models now come with built-in sensors and microcontrollers that adjust the heating element’s temperature automatically.
This prevents overheating and ensures consistent repellent distribution.
Child and Pet Safety
Manufacturers are also focusing on making devices safer for households with children and pets.
Features like tamper-proof locks and indicator lights that show when the device is in use are practical enhancements.
Moreover, using non-toxic, natural repellents is being explored to cater to more safety-conscious consumers.
Conclusion
The manufacturing process of electric mosquito repellents is a complex and multifaceted procedure that involves careful material selection, detailed design, rigorous testing, and quality-controlled production.
Continual advancements in safety design ensure these products not only effectively deter mosquitoes but also pose no risk to users.
As technology evolves, we can anticipate even more efficient and safer electric mosquito repellents on the market.
資料ダウンロード
QCD調達購買管理クラウド「newji」は、調達購買部門で必要なQCD管理全てを備えた、現場特化型兼クラウド型の今世紀最高の購買管理システムとなります。
ユーザー登録
調達購買業務の効率化だけでなく、システムを導入することで、コスト削減や製品・資材のステータス可視化のほか、属人化していた購買情報の共有化による内部不正防止や統制にも役立ちます。
NEWJI DX
製造業に特化したデジタルトランスフォーメーション(DX)の実現を目指す請負開発型のコンサルティングサービスです。AI、iPaaS、および先端の技術を駆使して、製造プロセスの効率化、業務効率化、チームワーク強化、コスト削減、品質向上を実現します。このサービスは、製造業の課題を深く理解し、それに対する最適なデジタルソリューションを提供することで、企業が持続的な成長とイノベーションを達成できるようサポートします。
オンライン講座
製造業、主に購買・調達部門にお勤めの方々に向けた情報を配信しております。
新任の方やベテランの方、管理職を対象とした幅広いコンテンツをご用意しております。
お問い合わせ
コストダウンが利益に直結する術だと理解していても、なかなか前に進めることができない状況。そんな時は、newjiのコストダウン自動化機能で大きく利益貢献しよう!
(Β版非公開)