- お役立ち記事
- Manufacturing Process of Ear Thermometers and Improvement in Measurement Accuracy
Manufacturing Process of Ear Thermometers and Improvement in Measurement Accuracy
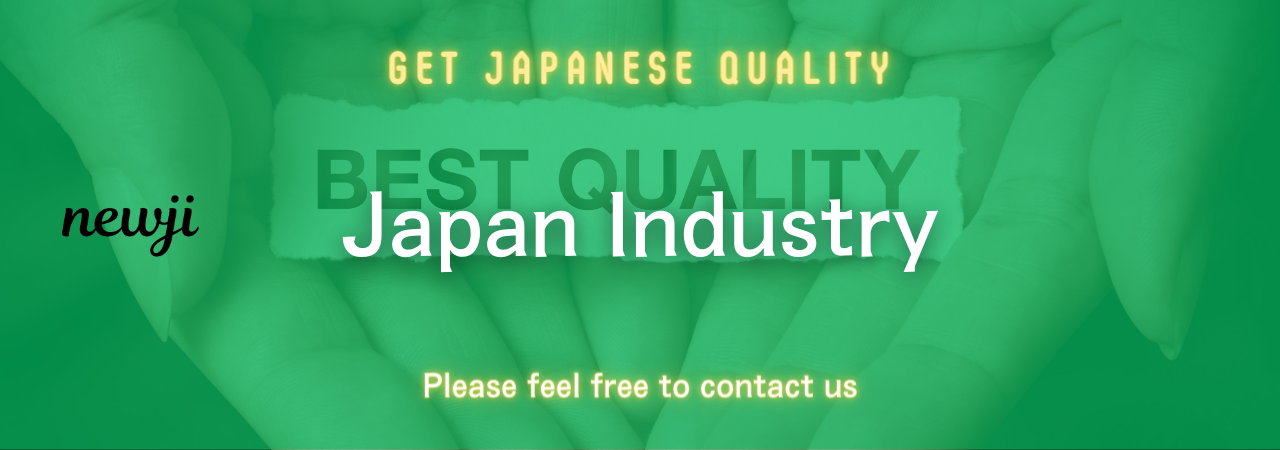
Ear thermometers have become a staple in both households and medical facilities due to their convenience and accuracy in measuring body temperature.
Understanding the manufacturing process of these devices and how their measurement accuracy is improved is essential for users and manufacturers alike.
目次
Manufacturing Process of Ear Thermometers
Design and Prototyping
The initial phase of manufacturing ear thermometers involves design and prototyping.
Engineers and designers study existing models and market needs to create a blueprint.
Using computer-aided design (CAD) software, they lay out the design and specifications of the thermometer.
Prototypes are then built using 3D printers to test the design practically.
Component Acquisition
Once the prototype is approved, the next step is sourcing high-quality components.
Key components include sensors, infrared detectors, electronic circuits, plastic casings, and display screens.
Suppliers and manufacturers work together to ensure that each part meets stringent quality standards to guarantee the accuracy and durability of the final product.
Sensor and Detector Assembly
The core component of an ear thermometer is the infrared sensor, which detects the infrared energy emitted by the eardrum.
This sensor must be assembled with care to ensure precise measurement.
The detector is calibrated to accurately convert the detected energy into a temperature reading.
Circuit Board Production
The electronic circuit board is the brain of the thermometer.
It processes the signals from the infrared sensor and displays the temperature on the screen.
Circuit boards are produced in a cleanroom environment to prevent contamination and are then populated with tiny electronic components through a process called surface-mount technology (SMT).
Case Molding and Assembly
The outer casing of the thermometer is typically made from durable plastic materials.
Injection molding machines shape the plastic into the required form.
These cases are then assembled with the circuit boards, sensors, buttons, and displays.
Quality Control and Testing
Every unit undergoes rigorous quality control checks and testing to ensure it meets regulatory standards.
These tests include calibration checks for accuracy, durability tests, and performance under different environmental conditions.
Thermometers are tested multiple times to guarantee consistent results.
Improving Measurement Accuracy
Advanced Sensor Technology
One of the key factors in improving measurement accuracy is the development of advanced sensor technology.
Modern ear thermometers use highly sensitive infrared sensors capable of capturing even the slightest variations in temperature.
These sensors are more reliable and provide faster readings compared to older models.
Enhanced Calibration Techniques
Calibration is crucial for accurate temperature readings.
Manufacturers use sophisticated calibration techniques to adjust the sensors precisely.
This involves comparing the readings from the sensor to a known reference temperature and making necessary adjustments.
Software Algorithms
The software within the thermometer plays a significant role in its accuracy.
Advanced algorithms process the raw data from the sensor and correct any potential errors.
These algorithms are designed to account for variables such as ambient temperature, user handling, and sensor position.
User-Friendly Design
The design of the thermometer also affects accuracy.
User-friendly designs ensure that the thermometer is easy to position correctly in the ear, reducing the chance of user error.
Clear instructions and ergonomic shapes help users take accurate readings consistently.
Environmental Adjustments
Accuracy can be affected by environmental factors such as room temperature and humidity.
Modern thermometers are designed to adjust for these variables automatically.
Sensors within the device measure ambient conditions and adjust the temperature reading accordingly.
Regular Updates and Maintenance
Manufacturers often release firmware updates to improve the performance and accuracy of their thermometers.
Regular maintenance, such as replacing worn-out sensors or recalibrating the device, is essential to maintain high levels of accuracy over time.
Future Innovations
The quest for improved measurement accuracy is ongoing.
Future innovations may include the integration of artificial intelligence to further refine the algorithms.
Enhanced connectivity features could allow ear thermometers to sync with other health-monitoring devices, providing a more comprehensive picture of a person’s health.
3D printing technology is also expected to play a larger role in the future, allowing for more precise and customizable components.
Additionally, ongoing research into new materials could lead to sensors that are even more sensitive and accurate.
Understanding the manufacturing process and advancements in technology can help users appreciate the efficiency and reliability of modern ear thermometers.
As technology continues to evolve, we can expect these devices to become even more accurate and user-friendly.
資料ダウンロード
QCD調達購買管理クラウド「newji」は、調達購買部門で必要なQCD管理全てを備えた、現場特化型兼クラウド型の今世紀最高の購買管理システムとなります。
ユーザー登録
調達購買業務の効率化だけでなく、システムを導入することで、コスト削減や製品・資材のステータス可視化のほか、属人化していた購買情報の共有化による内部不正防止や統制にも役立ちます。
NEWJI DX
製造業に特化したデジタルトランスフォーメーション(DX)の実現を目指す請負開発型のコンサルティングサービスです。AI、iPaaS、および先端の技術を駆使して、製造プロセスの効率化、業務効率化、チームワーク強化、コスト削減、品質向上を実現します。このサービスは、製造業の課題を深く理解し、それに対する最適なデジタルソリューションを提供することで、企業が持続的な成長とイノベーションを達成できるようサポートします。
オンライン講座
製造業、主に購買・調達部門にお勤めの方々に向けた情報を配信しております。
新任の方やベテランの方、管理職を対象とした幅広いコンテンツをご用意しております。
お問い合わせ
コストダウンが利益に直結する術だと理解していても、なかなか前に進めることができない状況。そんな時は、newjiのコストダウン自動化機能で大きく利益貢献しよう!
(Β版非公開)