- お役立ち記事
- The difference between Precision Machining and Rough Machining
The difference between Precision Machining and Rough Machining
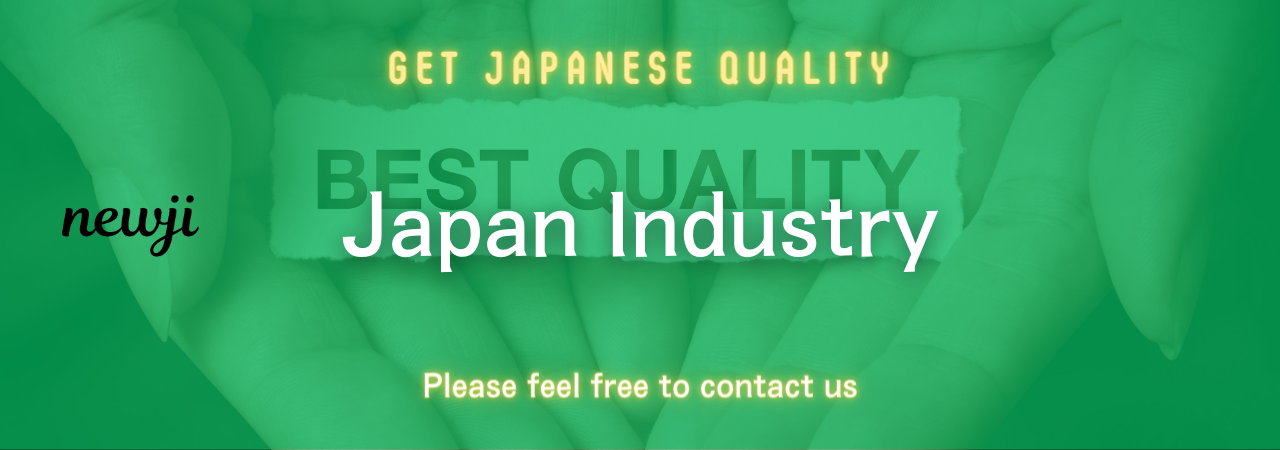
When discussing manufacturing and machining processes, two terms often emerge: precision machining and rough machining. Both methods are essential in the production of various components, but they serve distinct purposes and achieve different results.
Understanding these differences can clarify their roles in the manufacturing landscape.
目次
What is Precision Machining?
Precision machining refers to the process of cutting, milling, turning, or shaping materials into exact, detailed components with extremely tight tolerances.
This method utilizes advanced machinery like CNC (computer numerical controlled) machines, lasers, and EDM (electrical discharge machining).
These tools can create intricate parts out of metals, plastics, and other materials with extraordinary accuracy.
Precision machining is crucial in industries where even the smallest deviation can lead to significant issues, such as aerospace, medical devices, and electronics.
Applications of Precision Machining
Precision machining is employed to produce components that require high accuracy.
In the medical field, for instance, it is used to create surgical instruments and implants that must fit perfectly and operate flawlessly.
In the aerospace sector, precision-machined parts ensure the safety and performance of aircraft, satellites, and space exploration equipment.
Additionally, the automotive industry relies on precision machining for components like gearboxes, engine parts, and various electronic assemblies.
Advantages of Precision Machining
One of the significant advantages of precision machining is its ability to produce highly accurate and consistent parts.
This reduces the need for secondary operations or adjustments, further ensuring product quality.
Precision machining also allows for the creation of complex geometries that would be difficult or impossible to achieve with traditional methods.
Moreover, modern precision machining techniques offer fast turnaround times, significant cost savings in long-term production, and reduced waste through optimized material usage.
What is Rough Machining?
Rough machining, also known as roughing, is the initial phase in the machining process.
It involves the removal of large amounts of material quickly and efficiently to approximate the dimensions of the final part.
Unlike precision machining, rough machining does not focus on achieving exact tolerances or fine detail.
The goal is to prepare the workpiece for further machining stages by reducing it to a manageable size and shape.
Rough machining uses high-speed and high-power machinery, making it suitable for heavy-duty material removal operations.
Applications of Rough Machining
Rough machining finds its place in industries where large amounts of material need to be removed quickly.
For example, in metalworking, rough machining is employed to prepare metal blocks for more detailed work.
It is also commonly used in shipbuilding, construction, and heavy equipment manufacturing to shape large components before precision finishing.
Rough machining can also be seen in prototyping stages, where a rough version of a part is created to test a design concept before more detailed and precise machining is undertaken.
Advantages of Rough Machining
Rough machining has several benefits, particularly in the context of time and cost savings.
By quickly removing excess material, rough machining sets the stage for subsequent processes that require more time and precision.
This method is highly efficient for cutting through tough materials and handling large workpieces that may be cumbersome or challenging to machine with precision techniques initially.
Moreover, rough machining helps extend the lifespan of precision tools.
By doing the heavy lifting first, precision tools are preserved for the fine work, reducing wear and tear and the need for frequent replacements.
Key Differences Between Precision Machining and Rough Machining
While both precision machining and rough machining are integral to the manufacturing process, their objectives and approaches differ significantly.
Precision machining aims for exactitude and intricate details, making it ideal for final product stages.
In contrast, rough machining is about material removal efficiency, preparing a piece for further refinement.
Time and cost are other differentiating factors.
Precision machining typically requires slower, more meticulous operations, which can be more expensive due to the advanced technology and expertise involved.
Rough machining, however, is faster and generally less costly, focusing on getting a workpiece close to its final dimensions quickly.
Additionally, the equipment used in each process varies.
Precision machining relies on high-tech, often CNC-operated machines that provide fine control and accuracy.
Rough machining uses robust machinery designed for heavy-duty operations and rapid material removal.
When to Use Each Method
Deciding between precision machining and rough machining depends on the project requirements and the stage of the manufacturing process.
If a component needs to be fine-tuned to exact specifications, precision machining is the go-to method.
This is crucial when the final product must meet strict quality standards or fit within tight tolerances.
On the other hand, rough machining is best suited for the initial stages of production, especially when dealing with large, bulky materials.
It is particularly useful when the primary concern is to reduce the material size quickly before further refinement.
Conclusion
Both precision machining and rough machining play vital roles in the manufacturing industry.
Each method has its unique strengths and applications, contributing to the efficient production of high-quality components.
Understanding when to employ each technique ensures optimal results, whether the goal is to achieve fine detail and accuracy or to swiftly shape a workpiece for further processing.
By leveraging the benefits of both precision and rough machining, manufacturers can improve productivity, reduce costs, and produce superior products.
資料ダウンロード
QCD調達購買管理クラウド「newji」は、調達購買部門で必要なQCD管理全てを備えた、現場特化型兼クラウド型の今世紀最高の購買管理システムとなります。
ユーザー登録
調達購買業務の効率化だけでなく、システムを導入することで、コスト削減や製品・資材のステータス可視化のほか、属人化していた購買情報の共有化による内部不正防止や統制にも役立ちます。
NEWJI DX
製造業に特化したデジタルトランスフォーメーション(DX)の実現を目指す請負開発型のコンサルティングサービスです。AI、iPaaS、および先端の技術を駆使して、製造プロセスの効率化、業務効率化、チームワーク強化、コスト削減、品質向上を実現します。このサービスは、製造業の課題を深く理解し、それに対する最適なデジタルソリューションを提供することで、企業が持続的な成長とイノベーションを達成できるようサポートします。
オンライン講座
製造業、主に購買・調達部門にお勤めの方々に向けた情報を配信しております。
新任の方やベテランの方、管理職を対象とした幅広いコンテンツをご用意しております。
お問い合わせ
コストダウンが利益に直結する術だと理解していても、なかなか前に進めることができない状況。そんな時は、newjiのコストダウン自動化機能で大きく利益貢献しよう!
(Β版非公開)