- お役立ち記事
- An Easy-to-Understand Process Guide to Metal Press Workflows
An Easy-to-Understand Process Guide to Metal Press Workflows
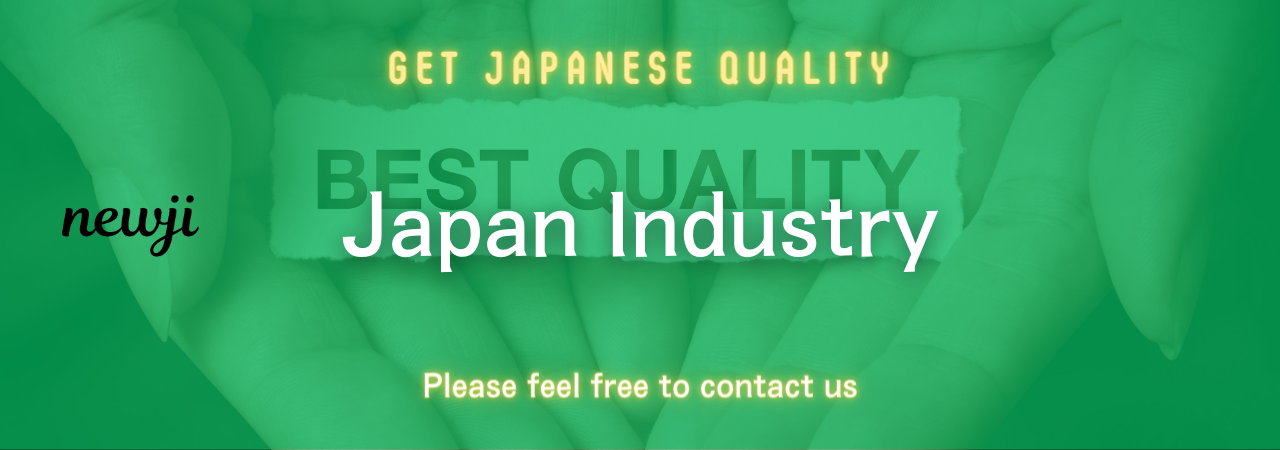
Metal pressing is essential in manufacturing, making everything from car parts to intricate electronic components.
The process transforms flat sheets of metal into a variety of shapes and sizes, using specialized tools and machinery.
Understanding this process can seem complex, but this guide will break it down into simple steps that anyone can follow.
目次
What is Metal Pressing?
Metal pressing is a technique used to shape and cut metal sheets.
It is widely used in various industries, including automotive, aerospace, electronics, and construction.
Metal pressing utilizes presses and dies, which are tools made from hard materials, to manipulate the metal into the desired shape.
Types of Pressing Machines
There are several types of pressing machines, each suitable for different tasks.
The most common types include:
1. **Mechanical Presses**: These machines use mechanical movements to exert force on the metal.
They are often used for high-speed operations, producing large volumes of components quickly.
2. **Hydraulic Presses**: These use hydraulic cylinders to generate force.
They provide a more controlled pressing action, making them ideal for more intricate and delicate tasks.
3. **Pneumatic Presses**: These presses are powered by compressed air.
They are generally used for lighter pressing tasks and are prized for their speed and precision.
The Metal Pressing Workflow
Understanding the workflow helps in appreciating how metal pressing contributes to the final product.
Here is a step-by-step look at the process:
Step 1: Designing the Press Tool
Before any pressing can begin, a press tool must be designed.
This tool includes two main parts: the punch and the die.
The punch is the part of the tool that pushes into the metal, and the die is the part that shapes it.
Designing these tools requires precision to ensure the metal is shaped correctly.
Step 2: Selecting the Metal Sheet
The next step involves selecting the appropriate metal sheet for the pressing process.
Commonly used metals include aluminum, steel, and copper.
The choice of metal depends on the product requirements, including strength, flexibility, and corrosion resistance.
Step 3: Setting Up the Press Machine
Once the tool and metal sheet are ready, the press machine is set up.
This setup involves installing the tool into the machine and adjusting settings to ensure the process runs smoothly.
The settings include pressure, speed, and the number of cycles the pressing will go through.
Step 4: The Pressing Process
With the machine set up, the metal sheet is fed into the press.
The machine then exerts force on the metal, pushing the punch into the die.
This action shapes the metal into the desired form.
Depending on the design, this action might be repeated multiple times to achieve the final shape.
Step 5: Quality Control
After pressing, the shaped metal piece undergoes quality control to ensure it meets the required specifications.
Inspectors check for any defects, such as cracks or uneven edges.
They also measure dimensions to ensure accuracy.
Applications of Metal Pressing
Metal pressing is versatile and used in numerous applications.
Automotive Industry
In the automotive industry, metal pressing is used to create parts like body panels, engine components, and bracketry.
These parts must be precise and durable, as they play a critical role in vehicle safety and performance.
Aerospace Industry
The aerospace industry relies on metal pressing to produce lightweight yet strong components.
Everything from structural parts to intricate engine pieces is made using pressed metal.
The precision required in this industry is exceptionally high due to the safety standards.
Electronics Industry
In electronics, metal pressing produces small, intricate parts for devices like smartphones, computers, and appliances.
The process allows for the high precision needed to create components that fit perfectly and function reliably.
Construction Industry
Metal pressing shapes materials used in building structures, such as beams, columns, and decorative elements.
These components need to be both strong and often aesthetically pleasing.
Advantages of Metal Pressing
Metal pressing comes with several significant advantages:
High Precision
The process allows for the creation of components with extremely tight tolerances, ensuring parts fit together perfectly in assemblies.
Efficiency
Once the press tool is set up, the pressing process can produce a high volume of parts quickly, reducing manufacturing time and costs.
Versatility
Metal pressing can be used with a wide range of metals and can produce parts of various shapes and sizes, making it adaptable to different manufacturing needs.
Durability
Pressed metal parts are generally robust and durable, especially when using high-quality materials and precise processes.
Challenges in Metal Pressing
Despite its advantages, metal pressing does have some challenges.
Initial Setup Costs
Creating the press tools and setting up the machinery can be expensive and time-consuming.
This upfront investment can be a barrier for smaller production runs.
Material Waste
The process can generate scrap metal, which needs to be recycled or managed properly to minimize waste and environmental impact.
Tool Wear
The punch and die can wear out over time, especially when working with hard metals.
Regular maintenance and sometimes replacement are necessary to ensure continuous precision.
Conclusion
Metal pressing is a critical process in modern manufacturing, providing the ability to produce precise, durable components efficiently.
By understanding the workflow and the machinery involved, one can appreciate the complexity and craftsmanship that go into this essential industrial practice.
Whether for cars, airplanes, electronics, or buildings, metal pressing shapes the world around us, quite literally.
Understanding its steps and applications helps in recognizing the value it brings to everyday products.
資料ダウンロード
QCD調達購買管理クラウド「newji」は、調達購買部門で必要なQCD管理全てを備えた、現場特化型兼クラウド型の今世紀最高の購買管理システムとなります。
ユーザー登録
調達購買業務の効率化だけでなく、システムを導入することで、コスト削減や製品・資材のステータス可視化のほか、属人化していた購買情報の共有化による内部不正防止や統制にも役立ちます。
NEWJI DX
製造業に特化したデジタルトランスフォーメーション(DX)の実現を目指す請負開発型のコンサルティングサービスです。AI、iPaaS、および先端の技術を駆使して、製造プロセスの効率化、業務効率化、チームワーク強化、コスト削減、品質向上を実現します。このサービスは、製造業の課題を深く理解し、それに対する最適なデジタルソリューションを提供することで、企業が持続的な成長とイノベーションを達成できるようサポートします。
オンライン講座
製造業、主に購買・調達部門にお勤めの方々に向けた情報を配信しております。
新任の方やベテランの方、管理職を対象とした幅広いコンテンツをご用意しております。
お問い合わせ
コストダウンが利益に直結する術だと理解していても、なかなか前に進めることができない状況。そんな時は、newjiのコストダウン自動化機能で大きく利益貢献しよう!
(Β版非公開)