- お役立ち記事
- The difference between Process Design and Product Design
The difference between Process Design and Product Design
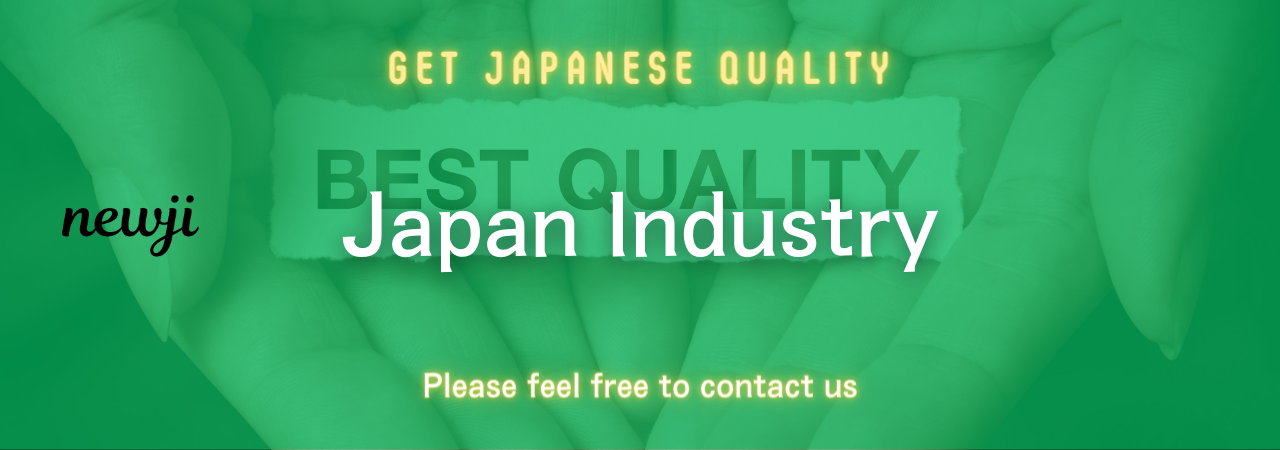
目次
Understanding Process Design
Process design is a crucial aspect of engineering and management that focuses on how things get done.
It involves planning and organizing tasks, resources, and workflows to achieve a specific goal efficiently.
In simpler terms, process design is about creating and refining a step-by-step procedure to produce a desired outcome.
A well-designed process ensures that tasks are completed in the right order, using the right resources, and within the expected timeframe.
This minimizes waste, reduces costs, and improves overall productivity.
For example, in a manufacturing plant, process design might involve arranging machinery and workstations in a way that minimizes the time it takes to assemble a product.
This kind of optimization can lead to significant improvements in efficiency and output.
The Components of Process Design
Inputs and Outputs
At the core of any process are its inputs and outputs.
Inputs are the resources required to carry out the process, such as raw materials, labor, and information.
Outputs are the final products or services generated by the process.
A clear understanding of these components is essential for effective process design.
Activities and Tasks
Activities and tasks are the individual steps that make up the process.
These steps need to be clearly defined and sequenced to ensure a smooth flow of work.
Each task should have a specific purpose and contribute to the overall goals of the process.
For instance, in a customer service process, tasks might include answering phone calls, responding to emails, and resolving complaints.
Resources and Constraints
Resources include everything required to carry out the process, such as personnel, equipment, and technology.
Constraints are the limitations or restrictions that impact the process, such as budget, time, and regulatory requirements.
Effective process design must take these constraints into account and find ways to work within them.
Metrics and Evaluation
To ensure that a process is efficient and effective, it’s important to have metrics in place to measure performance.
Key performance indicators (KPIs) can help track progress and identify areas for improvement.
Regular evaluation allows businesses to make necessary adjustments and keep the process running smoothly.
Understanding Product Design
Product design, on the other hand, focuses on the creation and development of new products.
It encompasses everything from the initial concept to the final product that reaches the market.
Product design aims to meet the needs and expectations of customers while also considering factors such as aesthetics, functionality, and cost.
A well-designed product not only looks good but also works effectively and provides a positive user experience.
The goal is to create a product that stands out in the market and meets the demands of consumers.
The Components of Product Design
Concept and Ideation
The process of product design begins with concept and ideation.
This involves brainstorming ideas and identifying potential products that could fill a gap in the market.
During this stage, designers consider customer needs, market trends, and technological advancements to generate innovative ideas.
Prototyping and Testing
Once a concept is developed, the next step is to create prototypes.
Prototypes are early versions of the product used to test and refine the design.
This stage is crucial for identifying any issues and making necessary adjustments.
Testing ensures that the final product will perform as expected and meet quality standards.
Design and Development
During the design and development phase, the product takes shape.
Designers create detailed specifications and work closely with engineers to bring the product to life.
This stage includes selecting materials, defining manufacturing processes, and creating detailed drawings or 3D models.
The goal is to develop a product that is both functional and aesthetically pleasing.
Production and Launch
The final stage of product design is production and launch.
This involves manufacturing the product, ensuring quality control, and preparing for market release.
Marketing strategies are developed to promote the product and attract customers.
A successful launch requires careful planning and coordination to ensure the product reaches its target audience.
Key Differences Between Process Design and Product Design
While both process design and product design are essential for business success, they have distinct focuses and objectives.
Understanding these differences can help companies effectively manage both aspects of their operations.
Focus and Objectives
Process design focuses on optimizing how tasks are performed to achieve a specific goal.
It aims to create efficient and reliable workflows that minimize waste and maximize productivity.
In contrast, product design is centered on developing new products that meet customer needs and stand out in the market.
Its primary objective is to create products that are functional, attractive, and cost-effective.
Components and Activities
The components and activities involved in process design and product design are different.
Process design involves defining inputs, tasks, resources, and metrics to create an efficient workflow.
Product design, on the other hand, includes concept ideation, prototyping, design development, and production.
Measurement and Evaluation
In process design, performance is measured using key performance indicators (KPIs) that track efficiency, cost, and productivity.
These metrics help identify areas for improvement and ensure that the process runs smoothly.
In product design, success is measured by factors such as customer satisfaction, product quality, and market acceptance.
Testing and feedback play a crucial role in evaluating the effectiveness of the product design.
Collaboration and Roles
Process design often involves collaboration between managers, engineers, and operations personnel to create and refine workflows.
Team members work together to identify bottlenecks, eliminate inefficiencies, and improve overall performance.
In product design, collaboration is essential between designers, engineers, marketers, and other stakeholders.
Each team member contributes their expertise to develop a product that meets market demands and user expectations.
Conclusion
Both process design and product design are vital components of business success.
While they have different focuses and objectives, they complement each other in creating efficient operations and innovative products.
Understanding the differences between them can help businesses effectively manage both aspects and achieve their goals.
By optimizing processes, companies can improve productivity, reduce costs, and enhance customer satisfaction.
At the same time, effective product design can lead to the development of new and exciting products that capture the attention of consumers and drive business growth.
In today’s competitive market, mastering both process design and product design is essential for staying ahead and achieving long-term success.
資料ダウンロード
QCD調達購買管理クラウド「newji」は、調達購買部門で必要なQCD管理全てを備えた、現場特化型兼クラウド型の今世紀最高の購買管理システムとなります。
ユーザー登録
調達購買業務の効率化だけでなく、システムを導入することで、コスト削減や製品・資材のステータス可視化のほか、属人化していた購買情報の共有化による内部不正防止や統制にも役立ちます。
NEWJI DX
製造業に特化したデジタルトランスフォーメーション(DX)の実現を目指す請負開発型のコンサルティングサービスです。AI、iPaaS、および先端の技術を駆使して、製造プロセスの効率化、業務効率化、チームワーク強化、コスト削減、品質向上を実現します。このサービスは、製造業の課題を深く理解し、それに対する最適なデジタルソリューションを提供することで、企業が持続的な成長とイノベーションを達成できるようサポートします。
オンライン講座
製造業、主に購買・調達部門にお勤めの方々に向けた情報を配信しております。
新任の方やベテランの方、管理職を対象とした幅広いコンテンツをご用意しております。
お問い合わせ
コストダウンが利益に直結する術だと理解していても、なかなか前に進めることができない状況。そんな時は、newjiのコストダウン自動化機能で大きく利益貢献しよう!
(Β版非公開)