- お役立ち記事
- The difference between Make-to-order Production and Make-to-stock Production
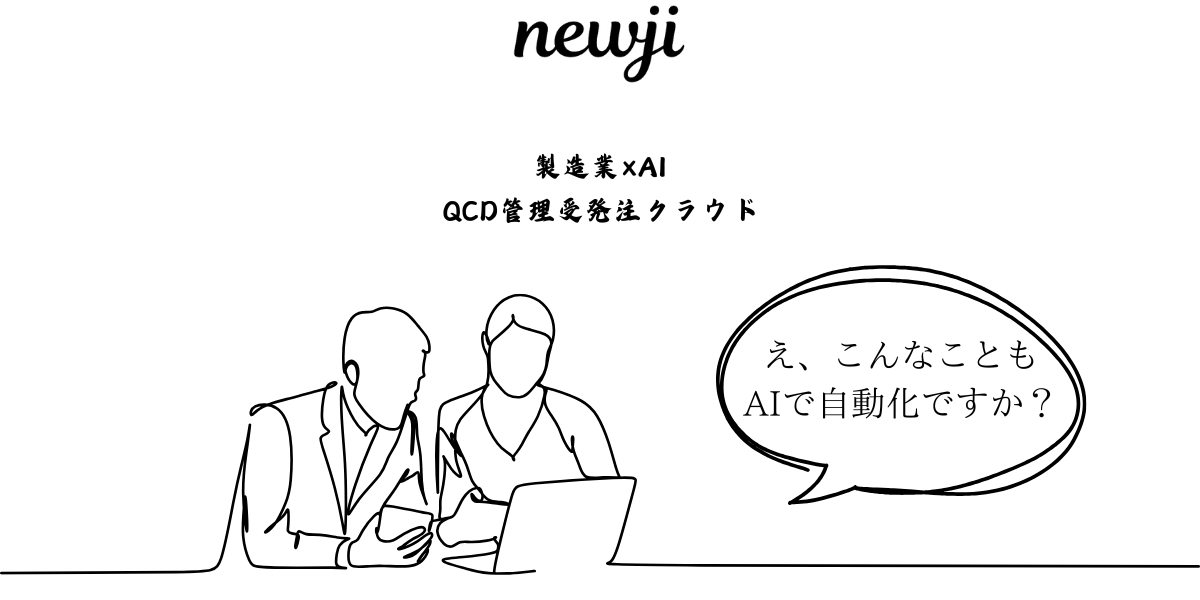
The difference between Make-to-order Production and Make-to-stock Production
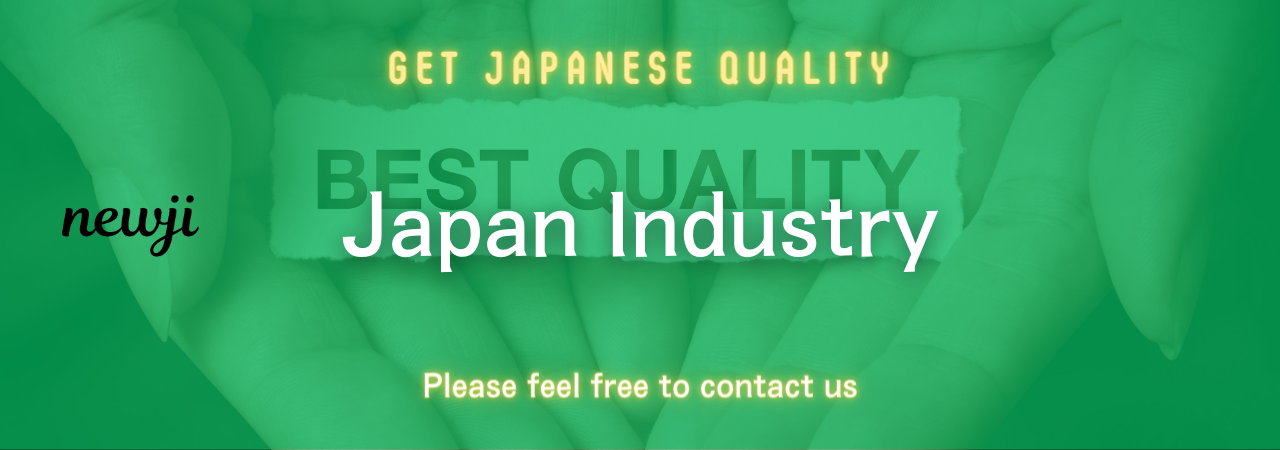
When running a business that involves production, it’s crucial to choose the right strategy.
Two of the most common production strategies are make-to-order (MTO) and make-to-stock (MTS).
But what are these, and how do they differ?
Let’s dive into their key differences and what each means for your business.
目次
Understanding Make-to-order Production
Make-to-order production, often abbreviated as MTO, is a strategy where items are produced only after an order is received.
This production method is tailored to meet specific customer requirements.
It involves a more personalized approach to manufacturing.
How Make-to-order Works
In MTO production, the process begins when a customer places an order.
Only after the order is confirmed do raw materials get sourced, and production starts.
This approach ensures that items are produced specifically for the customer, reducing the risk of unsold inventory.
Benefits of Make-to-order Production
MTO offers several advantages.
Firstly, it minimizes inventory costs.
Since products are made only after orders are received, there’s no need to keep large stocks of finished goods.
This can significantly reduce storage needs and associated costs.
Secondly, MTO allows for greater customization.
Customers can specify their requirements, leading to higher customer satisfaction.
This is particularly beneficial in industries where differentiation and customization add value.
Challenges of Make-to-order Production
However, make-to-order production isn’t without its challenges.
One major drawback is the longer lead time.
Since production starts only after an order is placed, customers may have to wait longer to receive their products.
Additionally, managing supply chains becomes more complex.
Sourcing raw materials on a per-order basis requires precise coordination to ensure timely production and delivery.
Understanding Make-to-stock Production
Make-to-stock production, or MTS, is a strategy where products are produced based on forecasted demand and kept in stock.
This method aims to have inventory readily available to meet customer needs swiftly.
It is often used in businesses where quick delivery is a key competitive advantage.
How Make-to-stock Works
In an MTS setup, production schedules are based on anticipated demand.
Companies forecast customer needs and produce items in advance.
These products are then stored in inventory until a customer places an order.
Benefits of Make-to-stock Production
The primary benefit of MTS is reduced lead time.
Since products are already made and waiting in inventory, they can be shipped to customers almost immediately.
This quick turnaround can enhance customer satisfaction and encourage repeat business.
Furthermore, MTS can lead to economies of scale.
By producing in larger batches based on forecasts, companies can often reduce per-unit production costs.
This can translate to higher profit margins.
Challenges of Make-to-stock Production
However, MTS also has its downsides.
One significant risk is overstocking or understocking.
Inaccurate demand forecasts can lead to excess inventory, which incurs storage costs and the risk of obsolescence.
Conversely, understocking can lead to missed sales opportunities.
Another challenge is the potential for reduced customization.
Since items are produced in advance, there is less flexibility to alter products to meet specific customer preferences.
This can be a disadvantage in markets where customization is an important factor.
Choosing Between Make-to-order and Make-to-stock
Choosing between MTO and MTS depends largely on the nature of your business and market demands.
Here are some key considerations to help you decide.
Nature of Products
If your products are highly customizable and unique, MTO might be the better option.
It allows for greater personalization and meets specific customer needs.
On the other hand, if your products are standardized and have steady demand, MTS could be more efficient.
Lead Time Expectations
Consider the lead time your customers expect.
If they require quick delivery, MTS can meet this need effectively.
However, if they’re willing to wait for a more customized product, MTO could offer significant value.
Cost Management
Analyze your cost structure.
MTO can help minimize inventory costs by reducing the need to store finished goods.
In contrast, MTS can help lower per-unit production costs through bulk manufacturing but may incur higher storage costs.
Market Demand Predictability
Assess how predictable your market demand is.
If you can forecast demand accurately, MTS can be highly efficient.
For more volatile markets where demand fluctuates significantly, MTO might present fewer risks.
Real-world Examples
Let’s look at a few real-world examples to illustrate these production strategies.
Make-to-order Example: Custom Furniture
Companies that produce custom furniture often use MTO.
Customers place orders with detailed specifications, and the furniture is made to those exact requirements.
This allows for high personalization and aligns perfectly with the MTO strategy.
Make-to-stock Example: Consumer Electronics
Many consumer electronics companies use MTS.
They produce standardized products like smartphones and laptops based on forecasted demand.
These items are then stored in inventory, ready to be shipped quickly when purchased.
This aligns well with the need for quick delivery in the tech market.
Conclusion
Understanding the differences between make-to-order and make-to-stock production is crucial for optimizing your business operations.
MTO focuses on meeting individual customer needs and minimizing inventory, while MTS aims for quick delivery and efficiency through bulk production.
By carefully evaluating your product nature, lead time, cost management, and market demand predictability, you can choose the strategy that best aligns with your business objectives.
Whether you opt for MTO or MTS, the key is to adapt your production processes to serve your customers effectively and efficiently.
資料ダウンロード
QCD調達購買管理クラウド「newji」は、調達購買部門で必要なQCD管理全てを備えた、現場特化型兼クラウド型の今世紀最高の購買管理システムとなります。
ユーザー登録
調達購買業務の効率化だけでなく、システムを導入することで、コスト削減や製品・資材のステータス可視化のほか、属人化していた購買情報の共有化による内部不正防止や統制にも役立ちます。
NEWJI DX
製造業に特化したデジタルトランスフォーメーション(DX)の実現を目指す請負開発型のコンサルティングサービスです。AI、iPaaS、および先端の技術を駆使して、製造プロセスの効率化、業務効率化、チームワーク強化、コスト削減、品質向上を実現します。このサービスは、製造業の課題を深く理解し、それに対する最適なデジタルソリューションを提供することで、企業が持続的な成長とイノベーションを達成できるようサポートします。
オンライン講座
製造業、主に購買・調達部門にお勤めの方々に向けた情報を配信しております。
新任の方やベテランの方、管理職を対象とした幅広いコンテンツをご用意しております。
お問い合わせ
コストダウンが利益に直結する術だと理解していても、なかなか前に進めることができない状況。そんな時は、newjiのコストダウン自動化機能で大きく利益貢献しよう!
(Β版非公開)