- お役立ち記事
- A Beginner’s Guide to High-Precision Machining Processes
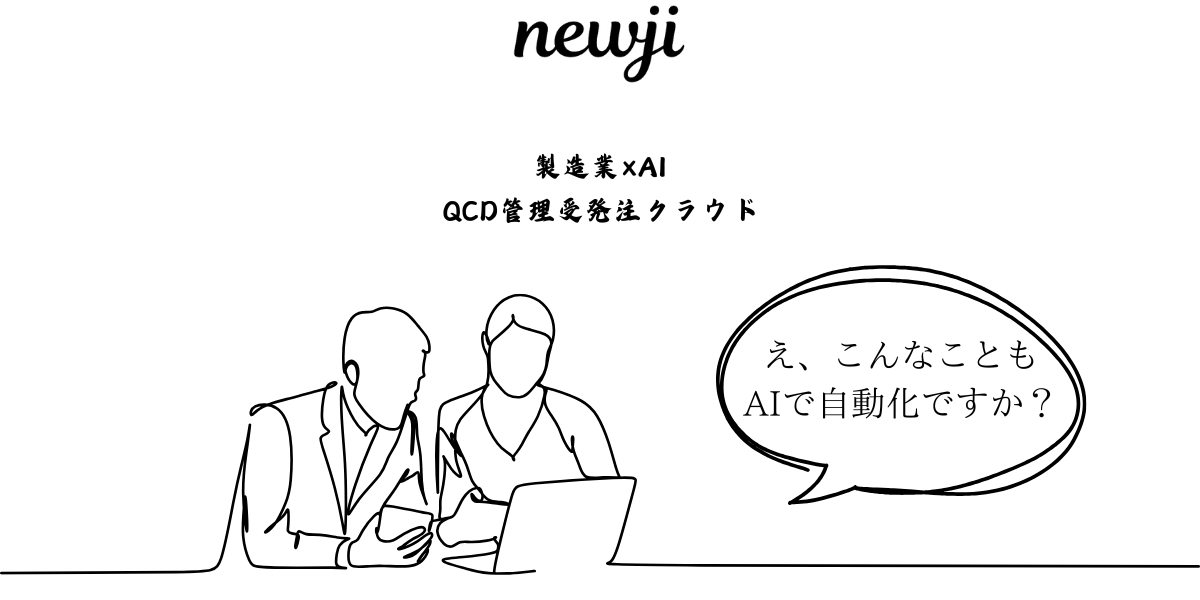
A Beginner’s Guide to High-Precision Machining Processes
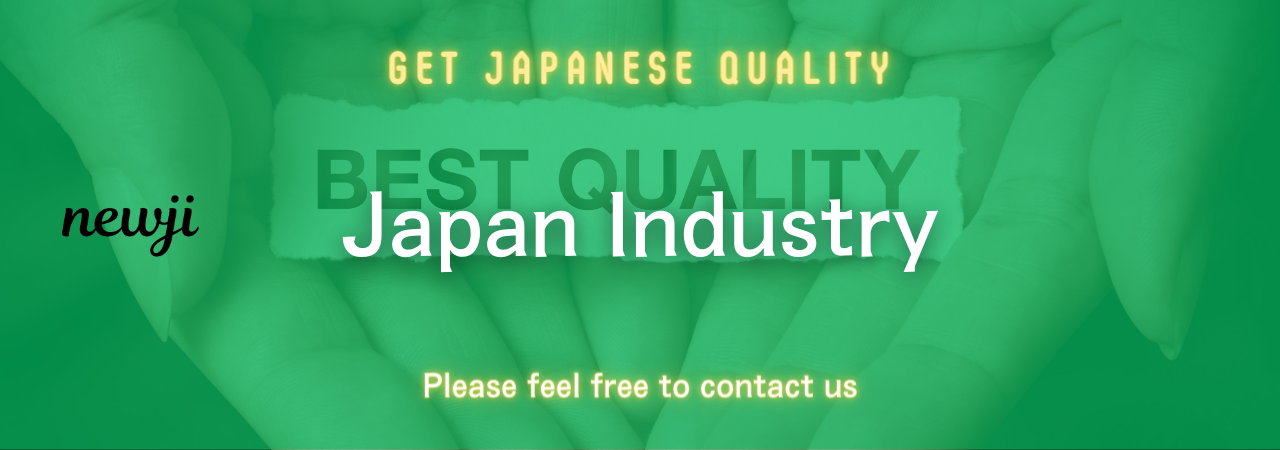
High-precision machining is a crucial part of modern manufacturing, playing a vital role in producing components that meet the stringent requirements of various industries such as aerospace, automotive, medical, and electronics.
This discipline involves using advanced tools and technologies to shape materials with incredible accuracy.
But what exactly is high-precision machining, and how does it work?
This guide will take you through the basics.
目次
What is High-Precision Machining?
High-precision machining is a process that removes material from a workpiece to create a desired shape, size, and surface finish.
It requires a high level of accuracy and consistency, often measured in micrometers or even nanometers.
High-precision machining can involve various techniques, including cutting, turning, milling, and drilling.
Given the meticulous nature of this process, specialized machines and skilled operators are essential to achieving the desired results.
The Importance of High-Precision Machining
Quality Assurance
High-precision machining ensures that parts and components meet exact specifications.
This is particularly important in sectors like aerospace and medical, where any deviation can lead to significant issues or even failures.
Cost Efficiency
While the initial investment in high-precision machinery can be substantial, the long-term benefits often outweigh the costs.
Efficient manufacturing processes reduce waste, save time, and improve overall productivity.
Innovation and Development
High-precision machining opens the door to new design possibilities, allowing engineers to create complex and innovative components that would be impossible with traditional methods.
Key Techniques in High-Precision Machining
Turning
Turning involves rotating the workpiece while a cutting tool moves in a linear fashion to remove material.
This technique is often used to create cylindrical parts and can achieve very tight tolerances.
Milling
Milling uses a rotating cutting tool to remove material from a stationary workpiece.
This technique is versatile and can be used to produce a wide range of shapes and features, including slots, pockets, and complex contours.
Grinding
Grinding involves using an abrasive wheel to remove material.
This technique is particularly useful for achieving fine finishes and tight tolerances.
Electrical Discharge Machining (EDM)
EDM uses electrical discharges or sparks to erode material from the workpiece.
This non-contact process is ideal for machining hard materials and producing complex shapes that would be difficult to achieve with traditional cutting techniques.
Materials Used in High-Precision Machining
Metals
High-precision machining often involves working with metals such as steel, aluminum, titanium, and brass.
These materials are chosen for their strength, durability, and ability to be machined to tight tolerances.
Plastics
Plastics like PEEK and PTFE are also commonly used in high-precision machining, particularly in industries where weight and corrosion resistance are key considerations.
Composites
Composite materials, which combine two or more different substances, can offer unique properties that make them ideal for specific applications.
High-precision machining techniques are often required to work with these challenging materials.
The Role of Technology in High-Precision Machining
Computer Numerical Control (CNC)
CNC technology is a cornerstone of high-precision machining.
These computer-controlled machines can execute complex instructions with incredible accuracy, allowing for highly precise and repeatable manufacturing processes.
CAD/CAM Software
Computer-Aided Design (CAD) and Computer-Aided Manufacturing (CAM) software are essential tools in high-precision machining.
They enable engineers to create detailed digital models of components, which can then be translated into precise machining instructions.
Advanced Metrology
Measuring and verifying the accuracy of machined parts is critical in high-precision machining.
Advanced metrology tools, such as coordinate measuring machines (CMMs) and laser scanners, play a crucial role in ensuring quality and consistency.
Challenges in High-Precision Machining
Material Limitations
Different materials have unique properties that can make them more or less suitable for high-precision machining.
For example, hard or brittle materials can be challenging to work with and may require specialized tools and techniques.
Tool Wear
The tools used in high-precision machining are subject to wear and tear, which can affect their accuracy over time.
Regular maintenance and tool replacement are essential to maintain consistent results.
Skill and Training
Operating high-precision machinery requires a high level of skill and experience.
Continuous training and development are necessary to keep up with technological advancements and maintain the quality of the machining process.
Future Trends in High-Precision Machining
Automation
The integration of automation and robotics in high-precision machining is set to revolutionize the industry.
Automated systems can increase efficiency, reduce human error, and allow for continuous production.
Internet of Things (IoT)
IoT technology enables real-time monitoring and data collection, allowing manufacturers to optimize their machining processes and quickly address any issues.
Advanced Materials
The development of new materials with unique properties will continue to drive innovation in high-precision machining.
Staying ahead of these advancements is crucial for maintaining a competitive edge.
Conclusion
High-precision machining is an essential aspect of modern manufacturing, offering unparalleled accuracy and consistency.
By understanding the techniques, materials, and technologies involved, you can appreciate the complexity and precision required to produce high-quality components.
As the industry continues to evolve, embracing new technologies and staying informed about advancements will be key to maintaining success in high-precision machining.
Whether you’re a seasoned professional or just starting, this guide provides a valuable foundation for understanding this fascinating and important field.
資料ダウンロード
QCD調達購買管理クラウド「newji」は、調達購買部門で必要なQCD管理全てを備えた、現場特化型兼クラウド型の今世紀最高の購買管理システムとなります。
ユーザー登録
調達購買業務の効率化だけでなく、システムを導入することで、コスト削減や製品・資材のステータス可視化のほか、属人化していた購買情報の共有化による内部不正防止や統制にも役立ちます。
NEWJI DX
製造業に特化したデジタルトランスフォーメーション(DX)の実現を目指す請負開発型のコンサルティングサービスです。AI、iPaaS、および先端の技術を駆使して、製造プロセスの効率化、業務効率化、チームワーク強化、コスト削減、品質向上を実現します。このサービスは、製造業の課題を深く理解し、それに対する最適なデジタルソリューションを提供することで、企業が持続的な成長とイノベーションを達成できるようサポートします。
オンライン講座
製造業、主に購買・調達部門にお勤めの方々に向けた情報を配信しております。
新任の方やベテランの方、管理職を対象とした幅広いコンテンツをご用意しております。
お問い合わせ
コストダウンが利益に直結する術だと理解していても、なかなか前に進めることができない状況。そんな時は、newjiのコストダウン自動化機能で大きく利益貢献しよう!
(Β版非公開)