- お役立ち記事
- The difference between Processing and Assembly
The difference between Processing and Assembly
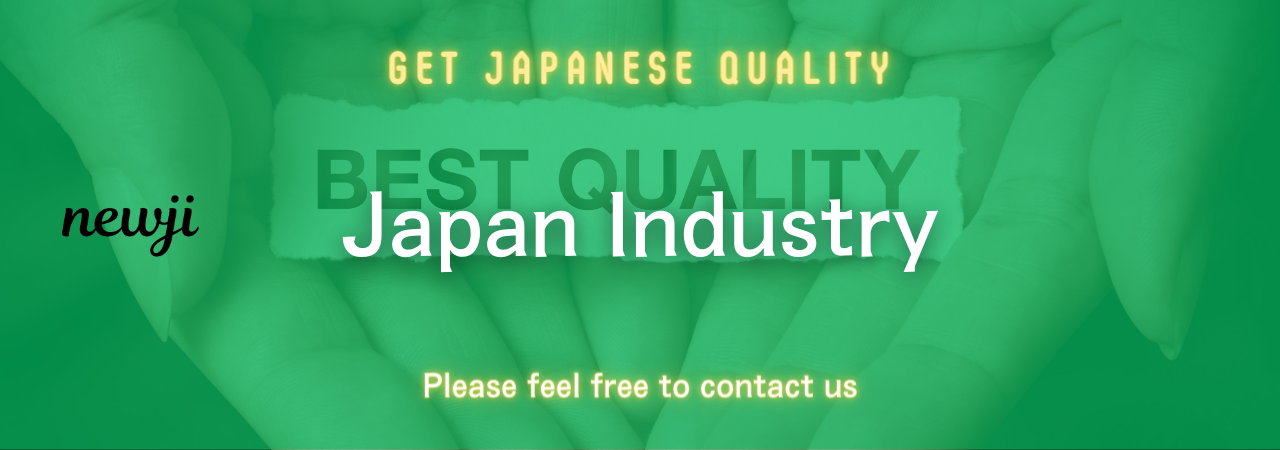
Processing and assembly are two critical stages in manufacturing that play distinct roles in bringing a product to life.
These stages are essential for transforming raw materials into finished goods, and understanding their differences is crucial for anyone involved in manufacturing or product development.
Let’s dive into the key differences between processing and assembly to better grasp their unique functions and importance.
目次
What is Processing?
Processing is the initial stage in manufacturing where raw materials are transformed into intermediate or finished products.
This stage involves various mechanical, chemical, or thermal techniques to change the material’s properties or shape.
For example, in the food industry, processing might include grinding, mixing, or cooking ingredients to create a packaged meal.
In metalworking, processing could involve cutting, shaping, or heat treating metals to produce components.
The primary goal of processing is to prepare the raw materials for the next stage of manufacturing, ensuring they meet the required specifications for quality and functionality.
Key Steps in Processing
1. **Material Selection**: Choosing the right raw materials is the first step in processing. Materials must meet specific standards to ensure the final product’s quality.
2. **Treatment and Shaping**: Various techniques like cutting, grinding, and heating are used to change the material’s form and properties.
3. **Quality Control**: Throughout processing, quality checks are essential to ensure the materials meet the required standards. This includes testing for durability, consistency, and safety.
4. **Intermediate Products**: Processing often results in intermediate products that need further assembly. These parts may require additional finishing or adjustments before moving to the next stage.
What is Assembly?
Assembly is the subsequent stage where processed components are put together to create a final product.
This stage involves combining intermediate parts, often through methods like welding, bolting, or gluing, to form a complete product ready for distribution and use.
The assembly process plays a crucial role in ensuring the product functions correctly and meets design specifications.
For example, in the automotive industry, assembly involves putting together various components like the engine, chassis, and interior parts to create a functioning vehicle.
Key Steps in Assembly
1. **Component Collection**: The first step in assembly is gathering all the processed parts required to build the final product. These parts must be inspected and verified for quality before use.
2. **Joining Methods**: Depending on the product, different techniques like welding, screwing, or adhesive bonding are used to join components together.
3. **Sub-Assembly**: Often, products are built in stages through sub-assemblies, where smaller parts are first assembled into larger sections. This helps streamline the assembly process and ensures precision.
4. **Final Assembly**: The sub-assemblies are combined and further refined to form the final product. This step includes adding finishing touches and making sure all parts fit perfectly.
5. **Testing and Inspection**: Once the assembly is complete, the product undergoes rigorous testing and inspection to ensure it operates correctly and meets all the design criteria. Any defects are identified and corrected before the product is packaged for distribution.
Differences Between Processing and Assembly
While processing and assembly are both integral to manufacturing, they serve different purposes and involve distinct techniques.
Let’s explore the fundamental differences between these stages.
1. Purpose
– **Processing**: The primary purpose of processing is to convert raw materials into usable forms by altering their properties and shapes. This stage focuses on material preparation and enhancement.
– **Assembly**: The main goal of assembly is to put together processed parts to create a finished product. This stage emphasizes combining components to ensure the final product functions as intended.
2. Techniques Used
– **Processing**: Techniques like cutting, grinding, heating, and chemical treatment are common in processing. These methods change the raw material’s physical or chemical properties.
– **Assembly**: Assembly techniques include welding, bolting, screwing, and gluing. These methods focus on joining parts together to form the final product.
3. Intermediate Products
– **Processing**: The output of processing is often intermediate products or components that require further assembly. These parts might need additional treatment or adjustments.
– **Assembly**: The result of assembly is the final product ready for use or distribution. This stage brings together all the processed components into a complete unit.
4. Quality Control
– **Processing**: Quality control in processing ensures raw materials are transformed correctly and meet the required standards. It involves testing for consistency, safety, and specific material properties.
– **Assembly**: Quality control in assembly ensures that the final product operates correctly and meets design specifications. It includes testing for functionality, safety, and overall performance.
5. Industry Examples
– **Processing**: In the pharmaceutical industry, processing involves synthesizing chemical compounds into medications. In the textile industry, processing includes weaving, dyeing, and finishing fabrics.
– **Assembly**: In the electronics industry, assembly involves putting together circuit boards, chips, and other components. In the furniture industry, assembly includes combining pieces of wood, metal, or plastic to create a finished product.
Conclusion
Understanding the difference between processing and assembly is crucial in manufacturing as each stage serves a unique and essential role.
Processing prepares raw materials by changing their properties and shaping them into intermediate products.
Assembly brings these components together to create a final, functioning product.
Both stages require meticulous attention to detail and rigorous quality control to ensure the finished goods meet the desired standards.
By recognizing the distinct functions and techniques involved in processing and assembly, manufacturers can streamline their operations, improve product quality, and increase efficiency.
This knowledge is invaluable for anyone pursuing excellence in the world of manufacturing and product development.
資料ダウンロード
QCD調達購買管理クラウド「newji」は、調達購買部門で必要なQCD管理全てを備えた、現場特化型兼クラウド型の今世紀最高の購買管理システムとなります。
ユーザー登録
調達購買業務の効率化だけでなく、システムを導入することで、コスト削減や製品・資材のステータス可視化のほか、属人化していた購買情報の共有化による内部不正防止や統制にも役立ちます。
NEWJI DX
製造業に特化したデジタルトランスフォーメーション(DX)の実現を目指す請負開発型のコンサルティングサービスです。AI、iPaaS、および先端の技術を駆使して、製造プロセスの効率化、業務効率化、チームワーク強化、コスト削減、品質向上を実現します。このサービスは、製造業の課題を深く理解し、それに対する最適なデジタルソリューションを提供することで、企業が持続的な成長とイノベーションを達成できるようサポートします。
オンライン講座
製造業、主に購買・調達部門にお勤めの方々に向けた情報を配信しております。
新任の方やベテランの方、管理職を対象とした幅広いコンテンツをご用意しております。
お問い合わせ
コストダウンが利益に直結する術だと理解していても、なかなか前に進めることができない状況。そんな時は、newjiのコストダウン自動化機能で大きく利益貢献しよう!
(Β版非公開)