- お役立ち記事
- The difference between Hot Forging and Cold Forging
The difference between Hot Forging and Cold Forging
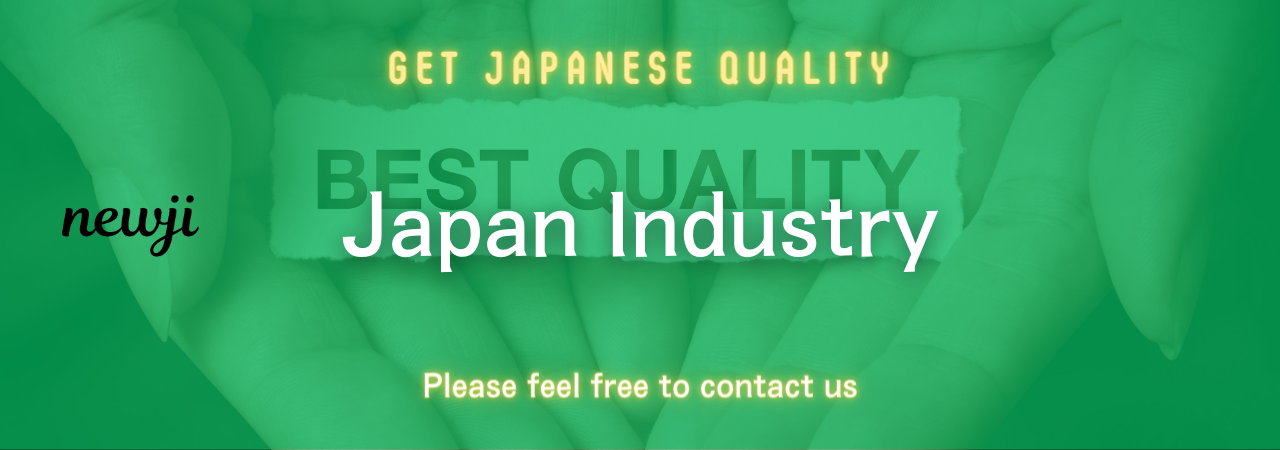
If you’ve ever wondered how metal parts are made or why some are stronger than others, you’re not alone.
The process of forging, which involves shaping metal using compressive forces, can be a bit complex, especially when it comes to deciding between hot forging and cold forging.
In this article, we’ll break down the differences between these two methods so you can understand what makes each one unique.
目次
What is Hot Forging?
Hot forging is a process where metal is heated to high temperatures before it is molded into shape.
The temperature at which hot forging occurs is typically above the metal’s recrystallization point.
For steels, this temperature is usually over 1,000 degrees Fahrenheit.
How Hot Forging Works
In hot forging, the metal is heated to make it more pliable, which makes it easier to shape.
Once heated, the metal is pressed or hammered into a die, which is a mold that shapes the metal.
This heating not only makes it easier to deform the metal but also helps eliminate internal stresses and improve the metal’s grain structure.
Advantages of Hot Forging
One of the significant benefits of hot forging is that it can produce highly complex shapes and large-sized parts.
Heating the metal above its recrystallization point allows for extensive plastic deformation with less risk of fracture.
Hot-forged parts usually have excellent mechanical properties, such as toughness and ductility.
Furthermore, this method can also eliminate some of the impurities in the metal, improving its overall quality.
Disadvantages of Hot Forging
Hot forging does have some downsides.
The high temperatures needed require more energy and more complex machinery, leading to higher costs.
Additionally, the final dimensions of hot-forged products can be less accurate due to thermal expansion and contraction.
The process can also result in surface oxidation, which may require additional finishing operations.
What is Cold Forging?
Unlike hot forging, cold forging is carried out at or near room temperature.
The metal is not heated beforehand, which introduces a completely different set of characteristics to the process.
How Cold Forging Works
In cold forging, metal is shaped by applying high pressure without the addition of heat.
The metal is placed into a die and then pressed or hammered into the desired shape.
This method requires metals that are capable of maintaining their strength even when not heated.
Advantages of Cold Forging
One of the key benefits of cold forging is its cost-effectiveness.
It requires less energy as no heating is involved, and the machinery used is generally less complex.
Parts produced through cold forging have excellent surface finishes, often eliminating the need for additional machining.
Moreover, because there is no high-temperature exposure, the dimensions of cold-forged parts are usually more precise.
Disadvantages of Cold Forging
Cold forging also has its limitations.
The process is generally suited for smaller, simpler parts as opposed to large or highly complex shapes.
Cold forging metal requires a significantly higher force, which necessitates stronger, more robust equipment.
The range of metals that can be cold-forged is also limited; harder metals like certain steels may not be suitable for this process.
Finally, cold forging can introduce work hardening, which might make the metal less ductile and more brittle.
Comparing Hot Forging and Cold Forging
Now that we have a basic understanding of both processes, let’s compare them side by side on some key aspects.
Material Suitability
Hot forging is generally suitable for a wide range of metals, including those that may be challenging to bend or shape at room temperature.
Cold forging is limited to materials that are ductile enough to be shaped without the need for heating.
Part Complexity
Hot forging can create complex and large parts because of the metal’s increased malleability when heated.
On the other hand, cold forging is more suited for simpler shapes and smaller parts due to the constraints imposed by operating at room temperature.
Surface Finish
Cold forging has the advantage when it comes to surface finish.
The lack of high heat keeps the surface smooth and clean, often eliminating the need for additional finishing operations.
Hot forging may result in a rougher surface due to oxidation and scaling, which usually requires further treatment.
Choosing the Right Method
Choosing between hot forging and cold forging depends largely on the specific requirements of the project.
Application Needs
For applications requiring high ductility and toughness, such as automotive or aerospace parts, hot forging is often the preferred method.
Cold forging is ideal when precision and surface finish are crucial, such as in fasteners and small components.
Cost Considerations
While hot forging usually incurs higher energy and equipment costs, it might be more cost-effective for large-scale, complex parts.
Cold forging is generally less expensive for smaller, simple parts but may become cost-prohibitive for larger, more complex shapes due to the higher forces required.
Understanding the differences between hot forging and cold forging can help you make more informed decisions based on your specific needs.
Both methods have their unique advantages and limitations.
Your choice should be guided by the type of material you’re working with, the complexity of the part, and your budget constraints.
資料ダウンロード
QCD調達購買管理クラウド「newji」は、調達購買部門で必要なQCD管理全てを備えた、現場特化型兼クラウド型の今世紀最高の購買管理システムとなります。
ユーザー登録
調達購買業務の効率化だけでなく、システムを導入することで、コスト削減や製品・資材のステータス可視化のほか、属人化していた購買情報の共有化による内部不正防止や統制にも役立ちます。
NEWJI DX
製造業に特化したデジタルトランスフォーメーション(DX)の実現を目指す請負開発型のコンサルティングサービスです。AI、iPaaS、および先端の技術を駆使して、製造プロセスの効率化、業務効率化、チームワーク強化、コスト削減、品質向上を実現します。このサービスは、製造業の課題を深く理解し、それに対する最適なデジタルソリューションを提供することで、企業が持続的な成長とイノベーションを達成できるようサポートします。
オンライン講座
製造業、主に購買・調達部門にお勤めの方々に向けた情報を配信しております。
新任の方やベテランの方、管理職を対象とした幅広いコンテンツをご用意しております。
お問い合わせ
コストダウンが利益に直結する術だと理解していても、なかなか前に進めることができない状況。そんな時は、newjiのコストダウン自動化機能で大きく利益貢献しよう!
(Β版非公開)