- お役立ち記事
- Manufacturing Process of Automatic Soap Dispensers and Improvement in Liquid Control Technology
Manufacturing Process of Automatic Soap Dispensers and Improvement in Liquid Control Technology
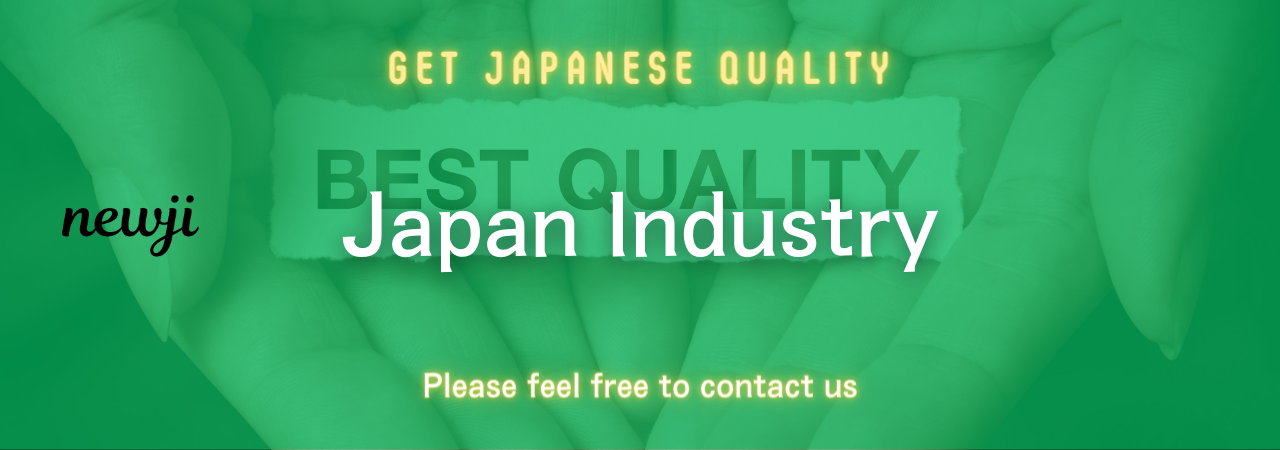
目次
Introduction to Automatic Soap Dispensers
The world of hygiene has changed dramatically with the invention of automatic soap dispensers.
These devices have become commonplace in public restrooms, hospitals, and even homes.
The touch-free operation ensures a more sanitary experience by eliminating the need to press a pump manually.
Understanding the manufacturing process and the improvements in liquid control technology behind these devices provides valuable insight into why they have become so popular.
Key Components of Automatic Soap Dispensers
Modern automatic soap dispensers consist of several crucial components.
These include a sensor, a pump, a reservoir for the liquid soap, and, often, a battery or rechargeable power source.
Each part plays a significant role in ensuring the device functions correctly.
1. The Sensor Mechanism
One of the essential components of an automatic soap dispenser is the sensor.
Infrared sensors are commonly used as they detect the presence of a hand by sensing changes in infrared radiation.
When a hand is placed under the dispenser, the sensor sends a signal to the pump to release a controlled amount of soap.
Advancements in sensor technology have enabled more accurate and responsive detection, which reduces the chances of malfunction.
2. The Pump System
The pump system is responsible for dispensing the soap.
There are various types of pumps used, such as piston pumps, peristaltic pumps, and diaphragm pumps.
Each type has its advantages and disadvantages.
The choice of pump depends on the viscosity of the liquid soap and the desired amount of soap to be dispensed.
3. The Soap Reservoir
The reservoir holds the liquid soap and needs to be designed for easy refilling and cleaning.
Materials such as plastic or glass are commonly used for reservoirs, and they are often transparent to allow users to see the soap level.
Careful design ensures that the soap does not leak and that the dispenser can be easily maintained.
The Manufacturing Process
Manufacturing automatic soap dispensers involves several steps from design to assembly.
This process ensures that the dispensers meet strict quality standards and function seamlessly.
1. Designing and Prototyping
The first step in manufacturing is designing the dispenser.
Engineers create detailed blueprints and 3D models using computer-aided design (CAD) software.
Prototypes are then produced using 3D printing technology to test the functionality and design of the dispenser.
Adjustments are made based on the performance of these prototypes to ensure efficiency and reliability.
2. Sourcing Materials
Once the design is finalized, manufacturers source the necessary materials.
This includes plastic or metal for the outer casing, electronic components for the sensor and pump systems, and materials for the reservoir.
Sourcing high-quality materials is crucial, as it directly impacts the durability and functionality of the dispenser.
3. Assembly
During the assembly stage, the various components are put together.
This is often done on an assembly line where each component is fitted into place in a step-by-step manner.
Technicians ensure that each part is correctly installed and that the final product meets quality standards.
Testing is an integral part of this stage to ensure the dispensers operate as intended.
4. Quality Control
Quality control is vital in the manufacturing process.
Each soap dispenser undergoes rigorous testing to check for defects and to ensure it meets performance criteria.
Tests include checking the sensitivity of the sensor, the accuracy of the pump system, and the integrity of the reservoir.
Only dispensers that pass these tests are packaged and shipped to customers.
Improvements in Liquid Control Technology
One of the most significant advancements in the field of automatic soap dispensers is the improvement in liquid control technology.
These improvements have enhanced the user experience and increased the efficiency of soap dispensers.
1. Precision Dispensing
Modern liquid control technology allows for precise dispensing of soap.
This means that each activation releases an exact amount of soap needed, reducing wastage.
Advanced microcontroller units (MCUs) and software algorithms play a significant role in achieving this level of precision.
2. Adaptive Dispensing
Adaptive dispensing technology can adjust the amount of soap dispensed based on various factors, such as the type of liquid soap and ambient conditions.
For instance, the dispenser can release more soap in colder environments where soap viscosity is higher.
This adaptability ensures consistent performance in all conditions.
3. Anti-Clogging Mechanisms
A common issue with liquid dispensers is clogging, especially when using thicker soaps.
Newer models incorporate anti-clogging mechanisms that prevent the soap from hardening in the reservoir or pump.
Ultrasonic vibrations and self-cleaning cycles are some of the technologies used to keep the dispenser clog-free.
4. Battery Efficiency
Battery life is a critical factor for automatic soap dispensers, especially in public areas with high usage.
Recent improvements in battery efficiency and energy management technology have resulted in longer-lasting dispensers.
Some models now come with rechargeable batteries and energy-saving modes to extend operational time.
The Future of Automatic Soap Dispensers
As technology continues to advance, the future of automatic soap dispensers looks promising.
Integration with smart home systems and the Internet of Things (IoT) is a likely development.
This would allow users to monitor soap levels remotely, receive alerts when refills are needed, and even customize dispensing settings through an app.
1. Sustainable Materials
With growing awareness of environmental issues, future soap dispensers are likely to be made with more sustainable materials.
Biodegradable plastics and recyclable components will become more common, reducing the environmental footprint of these devices.
2. Enhanced User Experience
The focus on user experience will drive innovations in design and functionality.
Touchless operation will become even more reliable, and dispensers may include features like customizable dispensing amounts and integration with other smart hygiene products.
3. Broader Applications
Beyond soap, similar technology can be applied to dispense other liquids such as hand sanitizer, lotion, and even kitchen cleaners.
This versatility will expand the usage of automatic dispensers in various industries.
Automatic soap dispensers have revolutionized hygiene practices with their innovative technology and user-friendly design.
Understanding their manufacturing process and the advancements in liquid control technology highlights the meticulous effort that goes into creating these essential devices.
With ongoing innovations, the future of automatic soap dispensers promises even more efficiency, sustainability, and enhanced user experience.
資料ダウンロード
QCD調達購買管理クラウド「newji」は、調達購買部門で必要なQCD管理全てを備えた、現場特化型兼クラウド型の今世紀最高の購買管理システムとなります。
ユーザー登録
調達購買業務の効率化だけでなく、システムを導入することで、コスト削減や製品・資材のステータス可視化のほか、属人化していた購買情報の共有化による内部不正防止や統制にも役立ちます。
NEWJI DX
製造業に特化したデジタルトランスフォーメーション(DX)の実現を目指す請負開発型のコンサルティングサービスです。AI、iPaaS、および先端の技術を駆使して、製造プロセスの効率化、業務効率化、チームワーク強化、コスト削減、品質向上を実現します。このサービスは、製造業の課題を深く理解し、それに対する最適なデジタルソリューションを提供することで、企業が持続的な成長とイノベーションを達成できるようサポートします。
オンライン講座
製造業、主に購買・調達部門にお勤めの方々に向けた情報を配信しております。
新任の方やベテランの方、管理職を対象とした幅広いコンテンツをご用意しております。
お問い合わせ
コストダウンが利益に直結する術だと理解していても、なかなか前に進めることができない状況。そんな時は、newjiのコストダウン自動化機能で大きく利益貢献しよう!
(Β版非公開)