- お役立ち記事
- The difference between Quality Assurance and Quality Inspection
The difference between Quality Assurance and Quality Inspection
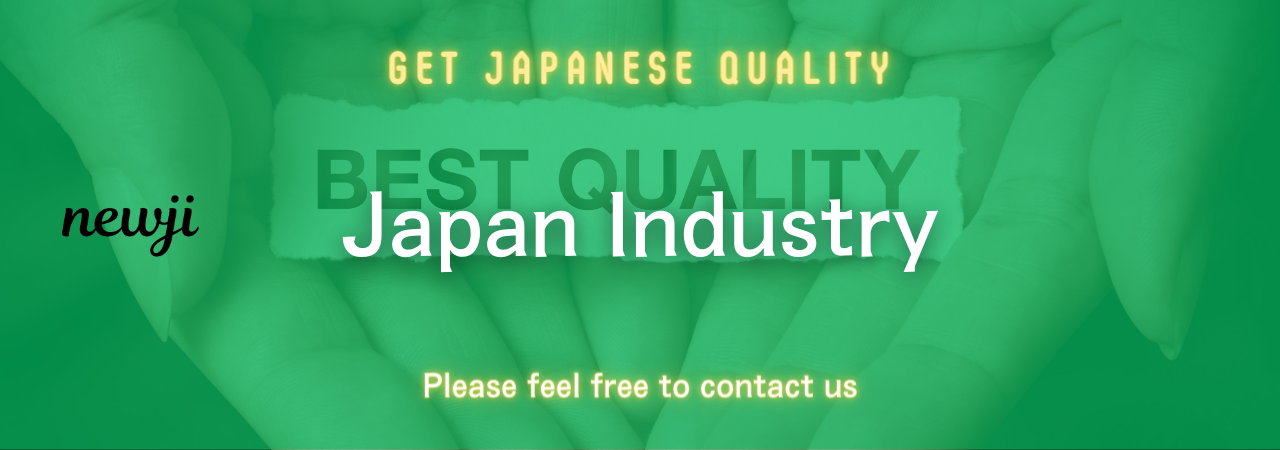
Quality assurance and quality inspection are two terms often used interchangeably, but they denote different processes and objectives within the realms of quality management and control.
Understanding the distinctions between these terms can help businesses ensure they are consistently delivering products and services that meet or exceed customer expectations.
Here, we will explore the major differences, the roles they play, and how integrating both can benefit organizations.
目次
What is Quality Assurance?
Quality assurance is a proactive process focused on preventing defects in products and services.
This systematic approach involves planned and systematic activities aimed at providing confidence that quality requirements will be fulfilled.
It is about ensuring that the processes used to design, test, and produce products or services are effective and efficient.
By adopting quality assurance practices, organizations can identify areas for improvement and implement changes before issues occur.
Reliable methodologies such as Six Sigma, Total Quality Management (TQM), and ISO standards are commonly used to establish robust quality assurance frameworks.
The Role of Quality Assurance
The primary role of quality assurance is to create and maintain the systems that ensure product integrity.
This includes documenting processes, setting benchmarks, and establishing metrics to measure performance.
QA teams conduct audits, monitor industry trends, and comply with regulatory requirements.
They interact with various departments to ensure that quality standards are integrated into every stage of production, from initial design to final delivery.
Benefits of Quality Assurance
Adopting a strong quality assurance system offers numerous advantages for businesses.
Firstly, it enhances customer satisfaction by ensuring that products and services meet quality standards consistently.
It reduces the cost of rework, scrap, and warranty claims by identifying problems early in the development process.
Furthermore, it improves productivity and efficiency as processes are continually assessed and optimized.
What is Quality Inspection?
Quality inspection, on the other hand, is a reactive process.
It involves examining products, services, and processes to identify any defects or non-conformities.
Quality inspections are typically carried out at various stages of production to catch any issues that may have been missed during initial development.
Unlike quality assurance, which focuses on process improvement, quality inspection focuses on the validation of outputs.
Inspectors use various tools and techniques to measure, test, and compare products against predefined specifications and standards.
The Role of Quality Inspection
The main role of quality inspection is to ensure that final products meet the required quality levels before reaching customers.
This involves inspecting incoming raw materials, in-process items, and finished goods.
Inspectors provide feedback to production teams, enabling corrective actions to be taken promptly.
Quality inspection serves as a line of defense, catching defects before they leave the manufacturing facility.
Benefits of Quality Inspection
Quality inspection offers a crucial checkpoint to ensure the final product meets all requirements and standards.
It helps in identifying and addressing defects, reducing the risk of customer complaints and returns.
This reactive measure can prevent potential brand damage and financial losses related to faulty products.
It also ensures compliance with regulatory standards, which is critical in many industries.
Key Differences
Although quality assurance and quality inspection are both integral to maintaining high standards, they have different focuses and methodologies.
QA is process-oriented and proactive, aimed at preventing defects by improving processes.
Meanwhile, quality inspection is product-oriented and reactive, focusing on identifying and correcting defects in the final product.
Quality assurance involves creating systems, policies, and audits to maintain a high standard, while quality inspection involves testing products and comparing them to standards.
Complementary Roles
Despite their differences, quality assurance and quality inspection complement each other.
Having a strong quality assurance system reduces the number of defects that need to be caught during quality inspection.
Conversely, the feedback gathered from quality inspections can inform quality assurance processes, leading to improved strategies and solutions.
Together, they form a comprehensive quality management system that ensures both processes and products meet the highest standards.
Integrating Quality Assurance and Quality Inspection
Integrating quality assurance and quality inspection within an organization’s quality management system can offer the best of both worlds.
Here’s how businesses can achieve this synergy:
Communication and Collaboration
Encouraging open communication and collaboration between QA teams and inspectors is crucial.
Sharing insights and feedback continuously can help both teams address issues more efficiently.
Utilizing Technology
Digital tools and technologies can streamline both quality assurance and quality inspection processes.
Automated data collection, analysis, and reporting tools can provide real-time information, reducing human errors and speeding up corrective actions.
Training and Development
Investing in training and development for employees ensures they understand both quality assurance and quality inspection processes.
A knowledgeable workforce is essential to maintaining high-quality standards consistently.
Conclusion
Understanding the difference between quality assurance and quality inspection is essential for any business striving for excellence in its products and services.
While QA focuses on process improvements to prevent defects, quality inspection aims to identify and correct defects in the final product.
Both processes are essential and, when integrated effectively, can significantly enhance product quality, customer satisfaction, and overall business performance.
By fostering collaboration between QA and inspection teams, utilizing advanced technologies, and investing in training, organizations can build a robust quality management system that stands the test of time.
資料ダウンロード
QCD調達購買管理クラウド「newji」は、調達購買部門で必要なQCD管理全てを備えた、現場特化型兼クラウド型の今世紀最高の購買管理システムとなります。
ユーザー登録
調達購買業務の効率化だけでなく、システムを導入することで、コスト削減や製品・資材のステータス可視化のほか、属人化していた購買情報の共有化による内部不正防止や統制にも役立ちます。
NEWJI DX
製造業に特化したデジタルトランスフォーメーション(DX)の実現を目指す請負開発型のコンサルティングサービスです。AI、iPaaS、および先端の技術を駆使して、製造プロセスの効率化、業務効率化、チームワーク強化、コスト削減、品質向上を実現します。このサービスは、製造業の課題を深く理解し、それに対する最適なデジタルソリューションを提供することで、企業が持続的な成長とイノベーションを達成できるようサポートします。
オンライン講座
製造業、主に購買・調達部門にお勤めの方々に向けた情報を配信しております。
新任の方やベテランの方、管理職を対象とした幅広いコンテンツをご用意しております。
お問い合わせ
コストダウンが利益に直結する術だと理解していても、なかなか前に進めることができない状況。そんな時は、newjiのコストダウン自動化機能で大きく利益貢献しよう!
(Β版非公開)